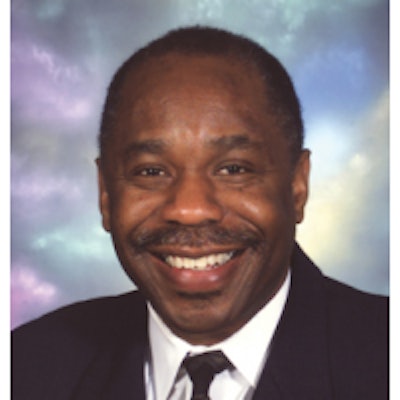
Plastic threaded closures (hereafter, closures) have wide applications with bottles and jars, sure; however, not to be forgotten are applications with tubes (metal and plastic), cartons (gable-top and aseptic), and flexibles (single-layer and multi-layer bags). With closures being a key component in so many packaging systems, considerable thought and planning are required for the optimal compatibility between that component and the other components of the system.
There are two categories of plastics used for closures: thermoform and thermoset. Their major distinction is how the formed closure is affected by subsequent exposure to heat. A thermoform closure will deform, and even melt under sufficient heat, but a thermoset closure will not.
Closures serve other functions beyond the obvious one conveyed by the term itself. So whereas all closures must perform the function of containment, they also can perform protection, communication, and convenience. There are not strict lines of demarcation among the aforementioned functions; to the contrary, they overlap, so much so that a particular feature can be categorized under more than one.
•Containment. Once applied, the closure must remain in place, preventing the escape of the contents, throughout all reasonably foreseeable conditions, until the closure is intentionally removed.
•Protection. The closure must prevent adulteration or other compromise of the contents by not serving as a means of entrance for undesired elements (oxygen and moisture, for examples) or as a means of escape for desired elements (moisture, flavor components, and active ingredients, for examples). And with some types of products, protection of the user is essential, hence the need for child-resistant, tamper-evident, and other forms of safety closures.
•Communication. The closure, when size allows, can carry print, whether of an instructional nature, or simply of a product-identification nature. The latter also includes being of a signature color, or alternatively, of a color that complements the other colors of the container and labeling.
•Convenience. The closure needs to facilitate use of the product. Easy-opening and easy-resealing may come most readily to mind; however, other features that can favorably differentiate the product include measuring and dispensing. Depending on the product, those features can equate to safety (as in the proper dosage) or to economy (using only the desired amount). Sometimes, what's required is a more complex design-multi-component, for example-or, even a one-piece that allows dispensing in more than one way, such as sprinkling and spooning. Specialty closures (anything other than the conventional, stock varieties) typically are an innovative marriage of function and aesthetics.
The supply side
The designation of features is an early step, ultimately leading to design and manufacture. Sourcing can be approached by soliciting bids and then comparing the proposals, factoring in such considerations as reputation, time in business, experience with similar clients, references, etc. Even so, it would be highly unusual for a bidding firm to not make mention of its manufacturing technology, making that another factor to consider. Plastic closures are manufactured by either of two technologies: compression molding and injection molding.
In the not-so-distant pass, the conditions that favored one over the other were more clear-cut. More recently, advances in both technologies have blurred many of those conditions. Claims and counterclaims fly like shrapnel regarding how the two compare across such parameters as economies-of-scale, mold costs, cycle-times, energy consumption, maintenance, changeover, waste generation, and dimensional tolerances, among others. If all of that adds up to greater flexibility of choice for the end-user, it comes at the price of acquiring the requisite knowledge to evaluate those claims and counterclaims.
•Compression molding. A preheated, softened amount of plastic is dropped into an open mold. A mating part presses down into the mold, and it's that pressure, along with continuous heat, that causes the plastic to flow (that is, be compressed) to the shape of the mold. The process is marked by high output, especially when the machinery is rotary.
Thermoplastics (i.e. polypropylene, polyethylene, polystyrene, and PET) are compatible with compression molding; however, the technology is the best choice when it comes to thermosets. Thermosets result in a sturdier closure, having a heftier feel, important if the desire is for a higher-end presentation. Additionally, thermosets are the practical choice for heat-intensive applications, such as retorting and even when the packaged product is expected to encounter ambient temperatures hot enough to deform thermoplastics. Color is a factor that influences the type of thermoset used: phenol formaldehyde yields dark colors; urea yields lighter colors.
•Injection molding. Resin melted inside a barrel-and-screw assembly is shot (that is, injected) through nozzles into molds, wherein the plastic takes shape and cooled before being ejected. The process is mostly the same as what was described in Injection blow molding (Packaging Insights 1/9/14), with the exception of those aspects that apply solely to the manufacture of containers, as opposed to closures.
Tight but not too tight
No factor is more critical to the performance of closures than that of torque. Application torque is the amount of force necessary to achieve a sufficiently tight sealing of the closure. Insufficient torque can result in product leakage and all the headaches it engenders, not just with the consumer, but throughout the distribution channel. On the other hand, excessive application torque also can result in product leakage, if threads are stripped. Then again, excessive application torque increases the required amount of removal torque, triggering the frustration that accompanies difficult-to-remove closures.
The determination of a proper application torque and the ability to maintain it within tight tolerances are at the core of an effective capping operation. High-speed, automated capping operations make direct measurement of application torque difficult; therefore, machinery calibration and scheduled checks should be supplemented with sealed containers being taken off the line and having their removal torques measured. That way, the measurement of the removal torque becomes a proxy for the measurement of the application torque, with the objective being the development of a reliable, formulaic relationship between the two.
No way this caps it
There's much more to consider in making decisions about closures, liners being one, thread designs being another. But space limitations can be tyrannical, so for now, it's time to assign this article closure.