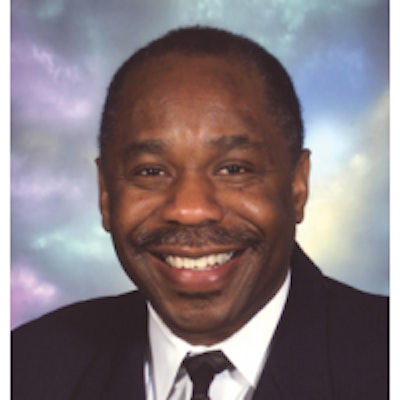
Containers made by injection blow molding (IBM) are prevalent in such major categories as food, beverage, pharmaceuticals, personal-care, household chemicals, and motor oils & other automotive products. The containers are bottles and jars in a variety of sizes made from a number of resins. To determine whether a container was manufactured by IBM, look for a gate, a nipple located bottom-center, analogous to the needle mark left by a medical injection.
A two-phase operation
Injection. Resin is melted inside a barrel-screw assembly, fed into a manifold, and then into nozzles that inject the melted resin into molds. The manifold and nozzles are major components of what's called a hot-runner system, calibrated and controlled to maintain the temperature and the flow characteristics of the melted resin within tight tolerances. Preforms (their name reflective of the fact that they are not the final shape of the container) are what emerge from the molds; however, what is final about a preform is its threaded finish, the top part that mates with a closure once the container is blown and filled. Think of preforms as resembling test tubes, with threaded finishes (not all preforms are that shape; for example, globular preforms are common with wide-mouth containers). Blow molding. The preforms make their way to molds in which the preforms will be blown into the shape of the container. The route taken can vary (more on that aspect upcoming). The process is similar to extrusion blow molding (and glass blowing, for that matter), in that it's air pressure that forces softened material (in this case, the preform) against the contours of the mold, producing a piece in the shape of that mold.
One machine or two
When the injection and blowing molding are performed on the same machine-that is to say, the preform and the container are produced on the same machine-it's known as a one-step operation. Combining the two phases is typical for small containers, such as those used for eye drops and pills. The preforms, still on the core pins that determine the interior dimensions of the preforms, are rotated to the blow molding part of the machine. By contrast, a two-step operation requires an injection molding machine for forming the preform and a blow molding machine for forming the container. The preforms are dropped into bins that hold thousands of them. The bins are taken to the blow molding area of the facility, where they are emptied into hoppers, out of which the preforms are mechanically elevated, aligned single-file, and fed into the blow molding machines. Inside those machines, the preforms travel through infra-red ovens that soften them, after which they make their way to the molds and are blown into containers. A two-step operation also can be a two-facility operation, wherein the preforms are injection molded in one facility and then shipped to another facility for blow molding. It's a practice used by the major suppliers of IBM containers, having some facilities that do injection and blow molding and other facilities that only blow the preforms received from other facilities. And there's another version of the two-facility scheme, this one between supplier and user; for example, some of the major soft-drink processors, in addition to receiving bottles from suppliers, also receive preforms and blow them at their own facilities. Those processors generate the quantities that justify the investment in blow molding machines. There's additional justification on the transportation side, in that, because of load density, the costs for shipping bins of preforms are less than those for shipping bottles. The latter is done on pallets, whereon tiers are separated with paperboard dividers, and the unit load is strapped and stretch-wrapped, resulting in a load density that's modest, at best.
IBM vs. EBM
Bottles and jars also can be manufactured by extrusion blow molding (for related reading, see Extrusion blow molding, Packaging Insights, February 27, 2012). The choice between IBM and EBM-true of all packaging-related choices-should reflect application-specifics. Conceding the contradiction in words, following are some generalizations about specifics:
•the type of container can be determining; for example, containers that have handles are better suited for EBM, while wide-mouth containers are better suited for IBM;
•if the tightest tolerances (especially in the neck finish and in wall thickness) are required, the nod should go to IBM;
•regarding coextrusions, the more complex the structure, the more it favors EBM;
•EBM generates scrap (in the forms of flash and trim), although they're fed back into the process, but IBM generates no such scrap;
•when factoring in mold costs, it should be borne in mind that IBM requires two types of molds but EBM only one; and,
•with the issue of overall costs casting its shadow, the greater the annual quantities the more conditions point to IBM.
Is the QA OK?
It's not unheard of that a user (brand-owner) partners with an injection blow molder without having set foot in that supplier's facility. Such a partnership can be forged from a Request for Proposal, with all subsequent responses-all the way up to approval of prototypes and samples from trial runs-done at the user's facility. But that convenience comes at the sacrifice of the type of knowledge that only can be gained by visiting the supplier. Seeing the machinery in operation and understanding the fundamentals is not the end-all; what's also needed is an understanding of how well quality is monitored and controlled. Evaluation of a supplier's QA should span receipt of raw materials through shipment of finished product. There should be no stand-alone operations; instead, every operation should be related to, and linked to, some other operations. That's best achieved with computerization, of such a level that IBM should share some similarities with that corporate behemoth of the same initials.
Sterling Anthony is a consultant, specializing in the strategic use of marketing, logistics, and packaging. His contact information is: 100 Renaissance Center- P.O. Box 43176; Detroit, MI 48243; 313-531-1875 office; 313-531-1972