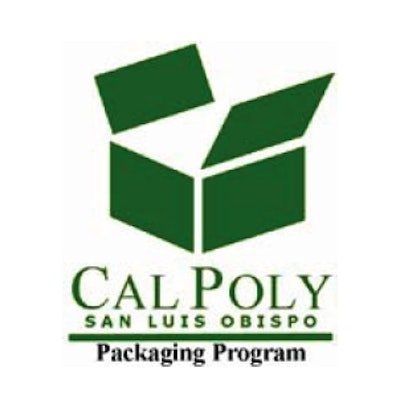
Much has happened since our on-site visit to California Polytechnic State University (Cal Poly, www.calpoly.edu), San Luis Obispo, CA, in fall 2003 (see Smooth changeover at Cal Poly ). At that time, Michigan State University (www.msu.edu) School of Packaging graduate Jay Singh, Ph.D., had just joined the faculty as the head of the packaging department, replacing long-time program director Larry Gay.
More recently, in the pages of Packaging World magazine, Dr. Singh authored an Academic Food Stuff column for the Oct. 2008 issue on Nanotech and food.
Around the same time that article was published, Dr. Singh was formalizing the creation of the first packaging research consortium in the Cal Poly packaging program. Dr. Singh says the idea of the consortium was to pool resources—and funding—around several projects of interest for the members, which number 12. Members include Microsoft, Tanimura & Antle, Safeway, TricorBraun, Bolthouse Farms, and others.
"It's a typical consortium where members pay a fee upfront, and then they get to approve the projects and share their results," says Dr. Singh. "We decided to conduct several scientifically centered key projects where everyone benefits."
The packaging program continues to operate a fee-based, per-project test facility on-campus, but the consortium represents a strategic shift from numerous small projects to fewer larger ones, according to Dr. Singh. The first round of R&D centers on the following four projects:
1. Valuation of sustainable recycled and biodegradable substrates in packaging
"We’re basically looking at samples submitted by the 12 member companies that they are either using or considering using," explains Dr. Singh, "and we are evaluating the claims made by the vendors."
Singh says they have perfected a test procedure to substantiate recycled content claims, such as "made of 100% recycled content."
This particular project, headed by Cal Poly professor Keith Vorst and supported by a graduate student, has a strong analytical chemistry aspect that includes the use of gas chromatography and mass spectroscopy.
The year-long project that will evaluate approximately 30 packaging materials is due to be completed by early summer 2009, which is the completion time frame for all four of these consortium projects.
Dr. Singh says the inclusion of a grad student in the cost model was a new tactic at Cal Poly. "We didn’t have a system like this in our program at Cal Poly till last year," says he says. “Students had to work on their Master-level research projects with the burden of paying tuition and other fixed expenses”
Dr. Singh says the benefit is that the student can spend more time working on projects rather than working off-campus to help pay for tuition.
Several samples that were received were analyzed for their recycled content claims, and the claims were found to be false. This emphasizes the need to verify claims by converters and distributors of plastic film and sheeting. With respect to the sustainable packaging substrates, after complete evaluation, questions to be discussed will include:
• Can we minimize material use?
• Can we find improved material choices (biopolymer vs. recyclable plastics)?
• Can we redesign for disassembly and ease of collection and sorting?
2. Evaluation of modified-atmosphere packaging plastic film
This project is self-explanatory: It involves the study and assessment of MAP films for fresh-cut salads or other produce drawn from samples provided by consortium members.
Dr. Singh says this project is the perfect example of the applied research conducted by the consortium.
"We're not looking to invent a new material," asserts Dr. Singh. "We assess available materials to see how they rate, and for which specific applications they perform best."
3. Life cycle inventory as a tool for packaging sustainability
Led by Dr. Singh with the assistance of a grad student, this project centers on the use of a purchased copy of SavvyPack™, a software program engineered for packaging life-cycle assessment.
"There are other LCA software programs available, but they do not focus primarily on packaging," explains Dr. Singh. "SavvyPack has more than 100 packaging substrates preprogrammed. Another of the key benefits of this software is it’s also an economic tool. And the database is updated regularly, about monthly."
Five licenses of the software were purchased for a discount.
One of the efforts within this project is the assessment of a gallon milk bottle. The sponsor consortium member company wanted to compare three possible options.
"The idea is to take an existing packaged product and redesign it using a different material or dimensions," says Dr. Singh. "By working directly with the sponsor, we can take it from the theoretical to the actual of what will work within their system."
In addition to different polymers, the team is also looking at the effect of any changes to the secondary packaging.
"If, for example you use a flat-top design and can eliminate using milk crates but need corrugated sheeting between layers, is that cost-effective if you can reuse milk crates for 30 or more times?" Dr. Singh asks. "And what if you eliminate a few grams from the bottle, what impact does that have throughout the distribution cycle?"
Although the results are for a one-year period exclusive to consortium members, one thing was found that Dr. Singh can share: "Pallet loads of milk containers on a truck weigh out before they cube out, so it doesn't really matter if you are using less space with the container design."
4. RFID tag-embedded distribution packaging solutions
This project centers on assessing three approaches to this, one of which is the HIDE-pack[tm] (see RFID smart boxes, published Feb. 2009).
"We want to see the effects of temperature and humidity and different forklift and conveyor belt speeds to see how the HIDE-pack performs compared to the other two designs that we are assessing," states Dr. Singh.
Another part of this project looks at RFID technology from Sirit used in Returnable Plastic Containers (RPCs). "Sirit's technology enhances the readability of tags placed on RPCs," points out Dr. Singh, who was involved with a recent RFID project of the Returnable Packaging Association (see RPC RFID field trials, published Dec. 2007).
The third project will have to remain mostly secretive for now because Dr. Singh is planning to patent it. "It involves corrugated and is another way of embedding RFID tags in distribution containers," he discloses. "These containers arrive with an inlay inside that you can program at the point of application."
The program uses RFID readers from Symbol Technology that is now part of Motorola and Alien Technology and a number of RFID tags.
Dr. Singh says that that he and instructor Vorst have collaborated to write packaging-specific grants totaling approximately $2 million over about the last two years, with most of them related to recycling or sustainability.
The recession has had little effect on the program, according to Dr. Singh: "We were lean to begin with, and the extra funding we’ve generated has been through our own efforts."
Gains ISTA accreditation
In other news, Cal Poly received International Safe Transit Association (ISTA, www.ista.org) certification as an ISTA-approved testing site in early 2009.
"We’ve probably invested more than $750,000 in the lab and equipment," boasts Dr. Singh. "We have a new compression tester, a 30,000-pound pressure compression tester from Lansmont, a new shock table, and a new drop tester. We also have two new environmental chambers for conditioning packages.
"Our corrugated material testing equipment has grown significantly at this point. I don’t think there are too many tests we cannot do at material testing levels for paper-based packaging."
However, Dr. Singh says they do not take on per-project testing unless there is an R&D component to it. "The university cannot take away market share from another company," he explains.
Dr. Singh says the ISTA certification is a big deal: “With certification, we have access to the ISTA database and the latest standards."
Another recent change is that industrial technology students—who number about 100 yearly—are now required to take at least four packaging courses in the period 2009 through 2011 to graduate with an industrial technology degree. That's enough to earn a minor in packaging, Dr. Singh points out. The upshot is that Dr. Singh expects the packaging enrollment to rise significantly, to around 100. The Cal Poly packaging program has been graduating about 45 students yearly.
For further information, contact Dr. Jay Singh by phone at 805/756-2129 or via email at [email protected].
More recently, in the pages of Packaging World magazine, Dr. Singh authored an Academic Food Stuff column for the Oct. 2008 issue on Nanotech and food.
Around the same time that article was published, Dr. Singh was formalizing the creation of the first packaging research consortium in the Cal Poly packaging program. Dr. Singh says the idea of the consortium was to pool resources—and funding—around several projects of interest for the members, which number 12. Members include Microsoft, Tanimura & Antle, Safeway, TricorBraun, Bolthouse Farms, and others.
"It's a typical consortium where members pay a fee upfront, and then they get to approve the projects and share their results," says Dr. Singh. "We decided to conduct several scientifically centered key projects where everyone benefits."
The packaging program continues to operate a fee-based, per-project test facility on-campus, but the consortium represents a strategic shift from numerous small projects to fewer larger ones, according to Dr. Singh. The first round of R&D centers on the following four projects:
1. Valuation of sustainable recycled and biodegradable substrates in packaging
"We’re basically looking at samples submitted by the 12 member companies that they are either using or considering using," explains Dr. Singh, "and we are evaluating the claims made by the vendors."
Singh says they have perfected a test procedure to substantiate recycled content claims, such as "made of 100% recycled content."
This particular project, headed by Cal Poly professor Keith Vorst and supported by a graduate student, has a strong analytical chemistry aspect that includes the use of gas chromatography and mass spectroscopy.
The year-long project that will evaluate approximately 30 packaging materials is due to be completed by early summer 2009, which is the completion time frame for all four of these consortium projects.
Dr. Singh says the inclusion of a grad student in the cost model was a new tactic at Cal Poly. "We didn’t have a system like this in our program at Cal Poly till last year," says he says. “Students had to work on their Master-level research projects with the burden of paying tuition and other fixed expenses”
Dr. Singh says the benefit is that the student can spend more time working on projects rather than working off-campus to help pay for tuition.
Several samples that were received were analyzed for their recycled content claims, and the claims were found to be false. This emphasizes the need to verify claims by converters and distributors of plastic film and sheeting. With respect to the sustainable packaging substrates, after complete evaluation, questions to be discussed will include:
• Can we minimize material use?
• Can we find improved material choices (biopolymer vs. recyclable plastics)?
• Can we redesign for disassembly and ease of collection and sorting?
2. Evaluation of modified-atmosphere packaging plastic film
This project is self-explanatory: It involves the study and assessment of MAP films for fresh-cut salads or other produce drawn from samples provided by consortium members.
Dr. Singh says this project is the perfect example of the applied research conducted by the consortium.
"We're not looking to invent a new material," asserts Dr. Singh. "We assess available materials to see how they rate, and for which specific applications they perform best."
3. Life cycle inventory as a tool for packaging sustainability
Led by Dr. Singh with the assistance of a grad student, this project centers on the use of a purchased copy of SavvyPack™, a software program engineered for packaging life-cycle assessment.
"There are other LCA software programs available, but they do not focus primarily on packaging," explains Dr. Singh. "SavvyPack has more than 100 packaging substrates preprogrammed. Another of the key benefits of this software is it’s also an economic tool. And the database is updated regularly, about monthly."
Five licenses of the software were purchased for a discount.
One of the efforts within this project is the assessment of a gallon milk bottle. The sponsor consortium member company wanted to compare three possible options.
"The idea is to take an existing packaged product and redesign it using a different material or dimensions," says Dr. Singh. "By working directly with the sponsor, we can take it from the theoretical to the actual of what will work within their system."
In addition to different polymers, the team is also looking at the effect of any changes to the secondary packaging.
"If, for example you use a flat-top design and can eliminate using milk crates but need corrugated sheeting between layers, is that cost-effective if you can reuse milk crates for 30 or more times?" Dr. Singh asks. "And what if you eliminate a few grams from the bottle, what impact does that have throughout the distribution cycle?"
Although the results are for a one-year period exclusive to consortium members, one thing was found that Dr. Singh can share: "Pallet loads of milk containers on a truck weigh out before they cube out, so it doesn't really matter if you are using less space with the container design."
4. RFID tag-embedded distribution packaging solutions
This project centers on assessing three approaches to this, one of which is the HIDE-pack[tm] (see RFID smart boxes, published Feb. 2009).
"We want to see the effects of temperature and humidity and different forklift and conveyor belt speeds to see how the HIDE-pack performs compared to the other two designs that we are assessing," states Dr. Singh.
Another part of this project looks at RFID technology from Sirit used in Returnable Plastic Containers (RPCs). "Sirit's technology enhances the readability of tags placed on RPCs," points out Dr. Singh, who was involved with a recent RFID project of the Returnable Packaging Association (see RPC RFID field trials, published Dec. 2007).
The third project will have to remain mostly secretive for now because Dr. Singh is planning to patent it. "It involves corrugated and is another way of embedding RFID tags in distribution containers," he discloses. "These containers arrive with an inlay inside that you can program at the point of application."
The program uses RFID readers from Symbol Technology that is now part of Motorola and Alien Technology and a number of RFID tags.
Dr. Singh says that that he and instructor Vorst have collaborated to write packaging-specific grants totaling approximately $2 million over about the last two years, with most of them related to recycling or sustainability.
The recession has had little effect on the program, according to Dr. Singh: "We were lean to begin with, and the extra funding we’ve generated has been through our own efforts."
Gains ISTA accreditation
In other news, Cal Poly received International Safe Transit Association (ISTA, www.ista.org) certification as an ISTA-approved testing site in early 2009.
"We’ve probably invested more than $750,000 in the lab and equipment," boasts Dr. Singh. "We have a new compression tester, a 30,000-pound pressure compression tester from Lansmont, a new shock table, and a new drop tester. We also have two new environmental chambers for conditioning packages.
"Our corrugated material testing equipment has grown significantly at this point. I don’t think there are too many tests we cannot do at material testing levels for paper-based packaging."
However, Dr. Singh says they do not take on per-project testing unless there is an R&D component to it. "The university cannot take away market share from another company," he explains.
Dr. Singh says the ISTA certification is a big deal: “With certification, we have access to the ISTA database and the latest standards."
Another recent change is that industrial technology students—who number about 100 yearly—are now required to take at least four packaging courses in the period 2009 through 2011 to graduate with an industrial technology degree. That's enough to earn a minor in packaging, Dr. Singh points out. The upshot is that Dr. Singh expects the packaging enrollment to rise significantly, to around 100. The Cal Poly packaging program has been graduating about 45 students yearly.
For further information, contact Dr. Jay Singh by phone at 805/756-2129 or via email at [email protected].