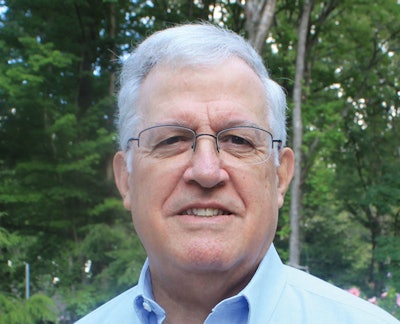
There’s more humor than truth in that observation by the late management guru, Warren Bennis. One development that’s making sure that human factory workers will be doing real work in the future, not just feeding the dog, is the collaborative robot, or “cobot,” a robot engineered to interact with humans in a shared workspace.
Globally, the market for cobots is expected to grow at a whopping CAGR of 56.94% between now and 2023. That would put the market at just over $4 trillion, according to a just released study by Markets and Markets (pwgo.to/3136).
Packaging applications are one of the biggest demand drivers for collaborative robots.
Cobots debuted at PACK EXPO about five years ago. Among the more than a hundred exhibitors showcasing their robotic capabilities at the Las Vega show last month, there were about half a dozen touting their cobots. The number of robots and cobots is going to rise at the show and in manufacturing operations in the years ahead. The reason is clear:
“About half the activities people are paid almost $15 trillion in wages to do in the global economy have the potential to be automated by adapting currently demonstrated technology,” according to A Future that Works: Automation, Employment and Productivity, a January 2017 study by the McKinsey Global Institute (MGI). MGI examined more than 2,000 work activities across 800 occupations. “While less than 5% of all occupations can be automated entirely using demonstrated technologies, about 60% of all occupations have at least 30% of constituent activities that could be automated,” say the MGI analysts. “More occupations will change than will be automated away,” they conclude.
Their analysis suggests that almost 60% of certain types of manufacturing activity—including “packaging products and loading materials on production equipment”—could be automated. “Performing repetitive physical activities or operating machinery in a predictable environment” represents one-third of such workers’ overall time, the study notes. (pwgo.to/3137)
“We’re going to see more people working alongside machines, whether you call that artificial augmentation or augmented intelligence, but we’re going to see a lot more of that,” comments MGI chairman and director James Manyika. “That’s quite important because it raises our whole sense of imperatives. It means that more skill is going to be required to make the most of what the machines can do for the humans.”
Developing the skills to “make the most of what the machines can do” is going to demand that assembly line workers and operators get the know-how, training, and practice to be able to effectively manage their mobile, cobotic partners.
There is some urgency to this task. The engineered precision of the robot-enabled processing and packaging lines workers will be working on tomorrow demands that they develop the required interfacing skills today. Packaging operations managers, robotic equipment developers, and packaging technology educators alike need to increase the number, quality, and accessibility of both on-line and hands-on courses they offer on collaborative robot operations management if the rising need for skilled computer and robot-savvy workers is to be filled.
Workers who develop and perfect their collaborating-with-robots skills will prosper and find higher pay grade positions open to them. Those who don’t will lose their jobs, even as more (albeit higher-skilled) operator positions open up.
Ben Miyares, Packaging Sherpa, is a packaging market and tech-nology analyst and is president of The Packaging Management Institute, Inc. He can be reached at [email protected].