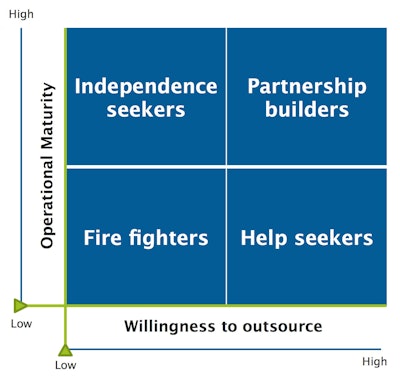
Beverage producers today are looking for optimum output and profitability from their lines. This increasingly brings far-sighted considerations on investment decisions regarding advanced maintenance programmes. Which maintenance approach can best answer those challenges?
Global trends are challenging the food and beverage industry under many aspects related to safety.
Firstly, an increasing concern for food safety: heightened consumer awareness is driving stricter legislation and control, introducing a stronger need for greater traceability all around the world, e.g. stricter labelling requirements, the obligation of displaying nutritional information etc. In the context of industrial beverage production, food safety is vital in protecting both the product and the consumer, in safeguarding the producer’s reputation and thereby in maintaining the long-term profitability and continued success of any brand. Production processes guaranteeing food safety are therefore a prerequisite for the responsible beverage production company.
The safety of people is just one of the critical elements at stake in industrial automated production, as is a safe and secure production process. Responsible for the safety of their operators and technicians, beverage producers are required to eliminate the hazards of working with faulty equipment, maintaining their production machinery according to good and safe working standards. Keeping heavily automated machines in perfectly hygienic and optimum working condition is therefore vital, both for the safety of personnel and for safe and secure production.
People safety goes hand in hand with the development of operators’ skills, especially given that the manufacturing of beverages today is more and more a highly automated process, often consisting of large, technically complex systems. Increased technological sophistication requires more sophisticated skills, thereby increasing the need for continuous operator training, skills transfer and active coaching.
Against an operational background of reduced budgets, ageing assets, a shrinking skilled workforce and rising material costs, many manufacturers are currently under great pressure to minimise the capital expenditure (CAPEX) and operating expenditure (OPEX), while maximising equipment availability and overall equipment effectiveness (OEE) - in order to get maximum return on those assets (RoA).
Leading operators have been segmented in a study performed by the Aberdeen Group (December 2013) in relation to the different balance they attribute to the above parameters, especially OEE versus ROA.
While industry average operators target 83% of OEE and 4% of ROA versus corporate plan, only 20% of market leaders would target 89% OEE and an impressive 24% of RoA. The remaining 30% of operators would be satisfied with 69% OEE, achieving a -7% of RoA. This suggest the criticality of OEE and ROA.
A forward-looking maintenance strategy can contribute to ensuring sound financial operations by preserving the availability of assets and reducing unplanned downtime to a minimum, thereby lowering operating costs and optimising total cost of ownership (TCO).
By 2030 forecasts suggest demands on our planet for energy will increase by 50%, food by 50% and water by 30%. Environmental considerations are more and more integrated into investment decisions, with the awareness that costs for energy and maintenance often outweigh the initial purchase price. Hence the maintenance of equipment and the monitoring of efficiency will become major contributors to sustainability. Concepts like lifecycle extension, minimised spare parts replacement and increased efficiency will be key to business competitiveness.
It is clear that advanced maintenance programmes can play today, and in the immediate future, a critical role in ensuring safety and reliability at production, operations, financial and environmental level.
Over the years producers have had to strike a balance between varying critical parameters: availability of skilled operators, technological complexity brought in by industrial progress, within a background of increasing market competitiveness.
In such a landscape, the importance of efficient asset management increases tremendously. Even though different approaches shape the maintenance landscape in a multi-faceted way, the objectives of maintenance remain the same: maximise productivity and OEE, production output, ROI, and ROCE (Return On Capital Employed)/RONA (return on net asset), while minimising total life cycle cost, maintenance cost, spare parts inventory and reducing fixed assets required and CapEx.
Taking as a reference parameters like equipment uptime and looking back at established trends and forecasting the developments of maintenance technologies, it’s safe to say that maintenance comes in several shapes and sizes:
Reactive maintenance:
This is maintenance undertaken only after a machine breaks down, which provides pressure on the maintenance team to rush and fix it – a practice often referred to as ‘firefighting’. This approach of purely ‘reactive’ maintenance is the result of little attention given to proper care of the machinery within the production line. When little or no maintenance is carried out, the machinery will only operate until a failure occurs, following a “run-to-failure” maintenance. At this point, experts may be called in to assess the situation and make the repairs as quickly as possible.
In adopting the ‘firefighting’ approach, while equipment maintenance entails no investment, there are other costs to consider related to high risks of secondary failure, costly production downtime, high costs of emergency spare parts supply, extra costs for external emergency intervention or operators’ overtime.
Preventive maintenance:
The 'Preventive Maintenance', or Scheduled maintenance, is an equipment maintenance strategy based on servicing, repairing or replacing items at fixed intervals, usually regardless of the exact condition at the time, with the aim of replacing components that are subject to wear, before they fail. This approach - “fix it before it breaks” - requires that machines are regularly submitted to diagnostic visits, maintenance is performed in a controlled manner, big unexpected failures are often reduced to a minimum, and there is a greater control of stored parts and costs.
Predictive maintenance:
With the advent of Industry 4.0, predictive maintenance combines original design data with available diagnostic and performance indicators. This approach analyses physical parameters against known engineering limits to anticipate problems. Based on the known condition and lifetimes of machines and components, predictive maintenance allows timely decisions to be made about possible servicing requirements and to allow for intervention before failure occurs.
One size does not fit all: different approaches to maintenance (see chart attached)
Based on their knowledge and understanding of leading market players, full solutions providers are recognising more and more frequently that approaches to maintenance are based on a combination of different criteria, such as: operational maturity, strategic business priority and willingness to outsource.
Some producers are interested in guaranteed results from their maintenance programmes and look for the reliability, predictability and productivity that contractors or their OEM (original equipment manufacturer) can supply. Those are inclined to build relationships with outside suppliers.
Those manufacturers who are more focused on cost optimisation of internal processes, often have their own systems and engineers and take care of their maintenance needs in an independent way.
They would usually be rather interested in improvement methodologies that become available to keep pace with technology advancement.
Those manufacturers who cannot count on qualified internal resources will seek help and outside support, leveraging on the technical expertise that experienced engineers can bring to fulfil their maintenance needs.
There are also those with limited in-house competence, who focus solely on minimising costs and take care of their own maintenance in a ‘firefighting’ approach. They use their own engineers for corrective maintenance, with replacement parts only being ordered as and when the need arises.
Relationship/partnership builders (group 1) would be more inclined to implement a Preventive and Predictive maintenance strategy, while fire fighters (group 4) would most probably be satisfied with a reactive maintenance programme.
Although it might not seem obvious at first sight, a purely reactive maintenance approach can result in significant losses in the long term, such as:
- extra costs for emergency work (OEM fees, overtime payments, price of emergency spare parts and shipping costs).
- productivity stoppages, possibly resulting in rising prices to customers, for inevitable customer dissatisfaction, leading in the worst-case scenario to a potential market loss.
- operators’ frustration, as productivity declines and emergencies increase.
Owners who want to secure their competitiveness in a fast-changing market and strike a balance in a tough financial landscape are increasingly seen to shift from a reactive to a proactive maintenance approach, meaning:
- fewer failures, resulting in increased uptime, thereby increasing productivity
- more accurate analysis of maintenance records
- product quality improvements
- optimised spare parts inventory
- finally, greater longevity of equipment, resulting in TCO reduction
The combined effect of these reduced costs and increased production levels will inevitably lead to higher profitability.
However, a well-designed preventive maintenance programme implemented without a special focus on flawless execution, is unlikely to be successful - just like the pit-stop teams of Formula One racing are a vital element in any race team’s strategy for success. The most successful racing teams come about when all factors involved work seamlessly and smoothly together: the cars themselves, the tools, each member in the team, the work practices and their successful implementation and the leadership provided by the management team - all focused on pre-determined, common goals.
(Author Samuel Le Guen, Maintenance and Line Improvement Director at Sidel, can be reached by emailing [email protected])