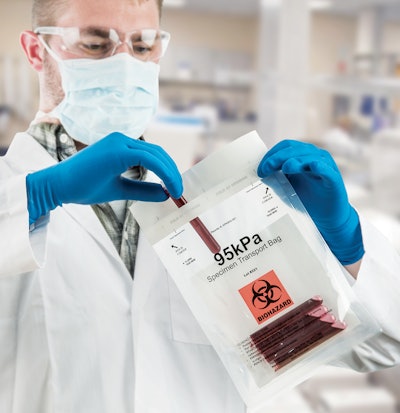
“There are lots of questions regarding infectious substances right now, including their handling and transporting,” says Tim Morgan, a partner at Vonco. “Our concern is that many of the bags being used are falling short of the requirements that have been established. This is something the industry as a whole needs to address.”
One of the bags in question is the 95kPa biohazard pressure bag. This bag, which is used as secondary protection when transporting potentially infectious samples, is designed to withstand without leakage an internal pressure that produces a pressure differential of not less than 95kPa. It must also have a permanent adhesive closure that can withstand a temperature range of -40°F to 130°F (-40°C to 55°C).
Morgan says, “As an industry, we need to provide clear evidence that the bags we are producing are safe. People and companies need to know that the work they are doing is safe. By conducting these tests, these labs will have the knowledge to make informed decisions regarding the bags they are using.”
In addition to potentially putting handlers of the bags at risk, the ramifications of using bags that do not meet DOT and IATA regulations include government fines, reshipping costs, and audits by federal and state agencies.
At a page called, “Pack Safe,” the Federal Aviation Administration’s website discusses the packaging of biological specimens, non-infectious, in preservative solutions. The site says, “Inner packagings must be placed in a heat-sealed plastic bag. Heat-sealed plastic bags must be placed in another heat-sealed plastic bag with enough absorbent material to absorb all of the contents of the inner containers. That bag is then put into a strong outer packaging with sufficient cushioning material.” For complete packaging requirements, FAA cites 49 CFR 173.4b, pwgo.to/1405