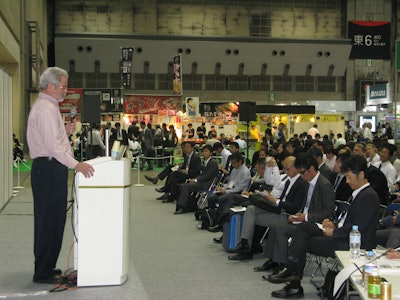
But there was much to see at the Big Sight exhibition hall earlier in the day.
• Update on China
Six packaging journalists belonging to the International Packaging Press Organization (including yours truly—see photo) delivered presentations on their various markets. Stuart Hoggard, publisher of PackWebasia.com and president of IPPO, shared a number of insights into what makes China tick these days. Since the global recession, Hoggard noted, which put U.S. and European markets in a tailspin, the Chinese government has focused on promoting consumption in those parts of China where it has thus far lagged. China now views these areas as well as the SouthEast Asian trade zone known as CAFTA as the market that will replace the U.S. and Europe. As for western Consumer Packaged Goods companies, they have reached a stage in their China strategy that Hoggard called the China Plus One strategy—by all means participate in the Chinese market, but think of SouthEast Asia as the place in which to get your manufacturing done because wages there are much more attractive than in China. Hoggard also noted that there is a shortage of skilled engineers in China and that staff retention is in the range of just two years.
• Microwave pasteurization
Fujicco, a large food company based in the Japanese city of Chiba, has announced a range of five refrigerated ready meals (see photo) that are packaged and microwave pasteurized by the MicVac system. A Swedish firm, MicVac is represented in Japan by Dai Nippon Printing Co. The items have a 30-day shelf life and sell for about $5.00. Compared to other conventional methods of pasteurization, which are usually thermal processes in which the food is subjected to heat, microwave pasteurization is said to produce a finished product whose flavor and nutrition profile are optimal because the food’s exposure to heat is minimized. (For more on MicVac, go here.)
• Augmented reality
Also at the Dai Nippon booth was a 120-g bag of Milky brand candy from Fujiya Food Service Co., Ltd. that featured augmented reality functionality. Thanks to a Dai Nippon app, when consumers scan the bag with a smart phone their screen comes alive with colorful animation and music, which in turn leads them to the home page of the Fujya Web site.
• Automated void-fill case packing equipment
Distribution centers serving E-commerce companies like Amway or Amazon have unique needs when it comes to case packing. Case counts vary wildly, and the idea of inventorying a case for every shipment is not a good one. Also, with so many variations inherent in the operation, it’s been a difficult thing to automate. But B+ Equipment has come up with two systems called Ultipack and I-Pack that make it possible for a distribution center to bring a considerable amount of automation to its operations and still get away with minimal case varieties. While B+ Equipment, a French firm, has offered both machines for a number of years, they were on display for the first time in Japan at the Tokyo Pack booth of Rengo Co., Ltd. B+Equipment will also be exhibiting at Pack Expo at the Sealed Air booth.
For both Ultipack and I-Pack, insertion of items to be shipped—clothing, books, whatever--is still done by hand. But once the operator places a case on the infeed conveyor, the rest is automated. The Ultipack senses the height of the items in the case and then presses a corrugated “wedge” down on top of the items at just the right height. This wedge is hot melt glued on all four sides so that the items are immobilized without any need to add void-fill material. In a subsequent station, a corrugated lid is formed from a flat blank and hot melt glued to the case.
The I-Pack system takes a slightly different approach. Once again the height of the items in the case are sensed. But this time there is no corrugated wedge inserted. Instead, the case is scored according to where the product height is detected. Then, in a subsequent station, the freshly scored case top is folded closed. Finally, in a third station, a flat blank is formed around the top and hot melt glued in place. Both systems are rated at speeds of 12 cases/min.