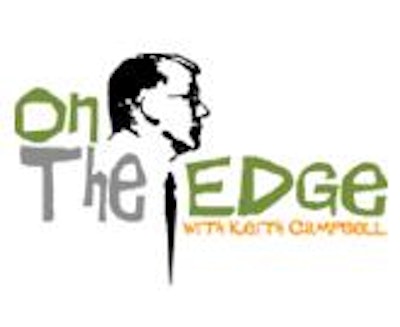
For companies doing business internationally, a web of different standards and laws must be daunting. For machine builders, machines may never be out of warranty where safety is concerned. As a manufacturing end user, I often found warranties counterproductive. We could wait on a service representative to show up to resolve a legitimate claim, or we could repair or redesign the machine ourselves and reap an immediate productivity improvement. Warranty claims are increasingly software-oriented, opening up whole new areas of discussion and responsibility.
Those of you who regularly read OnTheEdgeBlog, know that I am a sailor. Sailors seem to be blessed with suppliers that are accustomed to going above and beyond the terms of their warranties. Testimonials from sailors who have experienced outstanding customer service are regularly printed in journals like Practical Sailor, a publication that evaluates products and accepts no advertising. Perhaps that is why boating products are so expensive, but on the other hand, faulty products put sailors' lives at risk. Faulty processing or packaging machines may put consumers' lives at risk, but generally there are well-established good manufacturing practices and quality processes in place that obviate the impact of machinery that may be faulty.
The subject of warranty is not one that we've taken up here before. I've recently had reason to think about it, and maybe you have too. As we contemplate buying new machines in the halls of PackExpo or as we walk through the Fall boat shows, are warranty terms going to affect our decisions? Are warranties useful or not? Are they honored or not? How are they different between mass produced and custom machines? What happens after the warranty period, especially if faulty design is involved? Should a well-established history of failure alter expectations? I think that my readers would be interested in your thoughts and experiences.
Comments
Agree / disagree are not really appropriate choices.
You are on the right track Mean time to failure and mean time to repair, and mean cost of repair are information that help evaluate risk and need for warranty. this information is rarely given even if requested.
Posted by: Robert Petrach on September 28, 2012
Keith,
Not sure that I agree or disagree, but if the point is that warranties are "obsolete"from an equipment provider's perspective, I don't agree. I do agree with the statement that software is a much bigger driver for machinery and of course automation. As a result, we have made it standard practice to equip all of our machinery with remote monitoring capability. This has allowed us to keep a smaller staff of service techs and saved our customers countless downtime waiting for our tech to arrive. It is not a cure all and sometimes it appears to make our customers a bit lazy in their own troubleshooting, but software overall has eliminated many elements of a machine that do wear out - software does not
Craig
Posted by: Craig Souser on September 28, 2012
The intricacies of "warranty" are a very complicated matter . However this word is being used very lightly by manufacturers. The impact of the manufacturer waaranty is not fully understood by end retailers, especially those in the global chain.
Posted by: Sivaraman Subramanian on September 28, 2012
Hi,it is very good.I'm interested.may I use it to translate and issue in a packing magazine?
Posted by: nasser on September 29, 2012
Difficult topic. The best warranty protection is to do a fairly thorough FAT (Factory Acceptance Testing) at the vendors plant. It is worth the cost and time. Most design issues and functioning issues should surface and be dealt with at the vendors expense then and there. Too many times the FAT is not done or very poorly done and issues corp up on the production floor which is extremely costly and time consuming for all parties. Longer term issues can surface, but if you have good data to help both sides, then the vendor will (better)support, learn and improve his equipment for all and the customer gets their improvement plus an improved vendor in the future. Without good data and evidence a warranty is basically useless, because everyone argues from opinion.
Posted by: Paul Zepf on October 1, 2012
i agree with this it should be the thinking of supplier to their customer, not only to sell but to help them grow.
Posted by: joel on October 2, 2012
I am very much confused by these two words guarantee and warranty after reading your points my some doubts are clear and why is it necessary .I really say for a proper retailer-customer interaction these points to be learned....
Posted by: darren sam on November 16, 2012