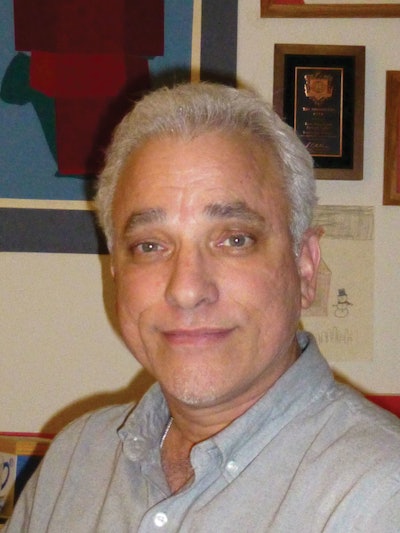
Last September, I presented a webinar for the Institute of Packaging Professionals entitled “Sustainability: Step 1 = Better Design.” Though the focus was on reducing environmental impact via smarter design, the discussion went far beyond packaging. Through multiple examples of a variety of products and components, it was shown that packaging engineers are truly unique in their abilities and knowledge to greatly influence their organizations in ways that few have yet tapped.
This column will demonstrate how packaging engineers can contribute far more, and therefore increase their value, in companies willing to accept a higher level of collaboration between packaging, product design, manufacturing, and supply chain logistics.
Having worked for literally dozens of companies, I’ve noticed some common themes that lead companies to fall short of maximizing their profitability. Perhaps the biggest problem is the silo effect, where each department is responsible for some portion of business, but doesn’t have someone providing tradeoff assessments that could lead to lower landed costs. For instance, if a product is particularly fragile, or if the geometry or overall size leads to a particularly large package, who should conduct the cost tradeoff of providing this large package vs. doing some product redesign?
From my experience, I think packaging engineering is the most capable of conducting these kinds of financial analyses. They’re in the middle between product design and supply chain, providing the needed protection required for a product to survive distribution. The fact is, the larger the package, the higher the logistics costs for shipping, storage, and handling. These logistics costs commonly can be five to 10 times greater than the packaging material costs for electro-mechanical products.
In conjunction with size and weight of the package is environmental impact. Global companies spend incredible amounts of money on shipping costs, so they spend lots of effort negotiating with carriers on rates, and also an inordinate amount of time considering things like the number and location of distribution centers. However, simply focusing more on product density per ocean container or truck can far outstrip any reduction in freight rates. Very few organizations have either engineers in the supply chain logistics group to help influence product design or mechanical engineers working on product designs who have knowledge of distribution hazards their products must typically survive. This is where packaging engineering can really shine!
It seems to me that packaging engineering is too commonly held in low esteem in large corporations, seen more as a necessary evil rather than a place where tremendous cost-saving insights can be generated. Why? Well, from the perspective of electro-mechanical products, the direct material costs for packaging normally are a small fraction of the direct material costs for the product. But if companies were to account for the total dollar influence of packaging, then everything would change. Unfortunately, many companies pigeonhole packaging people into thinking only about packaging, whereas more sophisticated companies are open to considering various tradeoffs between spending money on packaging versus material handling techniques versus product design.
Let’s consider an example. A company uses a bearing in a product. The company was experiencing damages to the inside edge of the bearing. Nicks and scratches on this edge led to catastrophic failure of the product. The damage was caused by the protrusion on the opposite side of the component when the bearings were vibrating and rubbing against each other inside a carton during transit.
The company’s packaging solution was to wrap each component individually in polyethylene microfoam. This approach increased material costs by the amount of the new material. In addition, the solution required three times as many cartons, pallets, trucks, storage space, and trips between the warehouse and the manufacturing line. Surprisingly, the company still experienced product damage after implementing this solution when line workers unwrapped each bearing and let them fall on each other in a bin.
A better solution was to eliminate the packaging by slightly redesigning the component. The male feature causing the problem on the bearing did not contain a critical dimension, in contrast to the female side. Reducing this feature allowed the parts to stack like Lego blocks.
This concept is encapsulated by a term known as DfD, Design for Distribution. With the help of knowledgeable packaging people, components and entire products can dramatically reduce packaging while also simultaneously reducing damage and environmental impact.