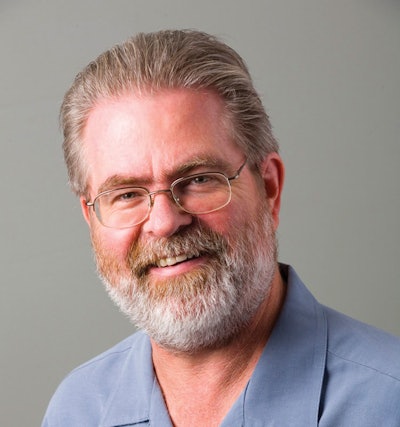
With this issue, we heartily welcome Ben Miyares back into our editorial fold. As you may recall, Miyaresβ Insider column was a monthly fixture when we first launched Packaging World in January of 1994. He later worked with PMMI as vice president of industry relations, and his editorial contributions regularly graced the pages of that organizationβs PMT magazine. Now he heads up his own packaging consultancy and still contributes editorially to PMMIβs many and varied projects. But with his return to the pages of Packaging World, youβll find his column every other month next to our inside back cover.
In this monthβs column, Miyares looks at how shrink-sleeve labeling is being challenged by direct bottle decorating. Thatβs not the only challenge that shrink-sleeve labeling is facing. NAPCOR, the National Association for PET Container Resources, issued a position paper this past March decrying the increased percentage of full-wrap shrink-label material in the PET recycle stream. βWhat was formerly a nuisance,β says NAPCOR, βhas become a crisisβ¦as reclaimers, particularly those focused on manufacturing RPET for use in packaging applications such as bottles and thermoforms, have had to remove these full-wrap label bottles, either manually or by reprogramming autosort equipment.β
Despite all efforts to remove shrink-sleeve labels from the PET recycle stream, some of them get through and cause a number of problems that all lead to one thing: the overall quality and reusability of the RPET is negatively affected. The solution, says NAPCOR, is to use a label material other than the ones used most commonly today: OPS, PETG, PLA, and PVC. These all become problematic if they reach the part of the recycling process where bottles are ground into flake that gets sent through a float/sink system to remove impurities. Since the specific gravity of these label materials is so similar to that of the PET, they sink with the PET flake and contaminate that otherwise pure source of PET.
So what does NAPCOR recommend? A label material whose specific gravity causes it to float in the float/sink system, while PET flake sinks. This, says NAPCOR, would make it easy to separate the potentially contaminating label materials from the valuable PET flake.
Flash forward to Octoberβs Pack Expo. What to our wondering eyes should appear but three exhibitorsβExxonMobil, Printpack, and MRIβall featuring sleeve labeling materials that address NAPCORβs concerns. ExxonMobilβs Label-Lyte 50TD200 modified OPP is a shrink-sleeve material, Printpackβs Ecoskin LDPE is a shrink-sleeve material, and MRIβs C-Fit high-elastic PE is a stretch-sleeve material that doesnβt even need to be heat shrunk. All three have a specific gravity that causes them to float to the top when PET flake sinks to the bottom.
Among the first commercial users of the MRI stretch-sleeve material is Producers Dairy of California. Theyβre using a stretch application machine from PDC International to apply this new-generation label to single-serve bottles of milk products. Does this new stretch-sleeve label material permit the graphic brilliance that was attained when Producers Dairy of California was using a shrink-sleeve label? No. But the new label is said to cost anywhere from 30 to 50% less than a shrink-sleeve label, and it makes it easier for processors to put more RPET back into the marketplace.
Though I didnβt happen to encounter them at Pack Expo, another producer that has come up with a label material that floats free from PET flake is Polysack Plastics Industries, an Israeli firm whose Polyphane Fit material is available in the U.S. from Avery Dennison.
For a visual reference on this whole float/sink proposition, take a look at this video I shot at ExxonMobilβs Pack Expo booth: www.bit.ly/pwe00447.
Do you find it as fascinating as I do that sustainable packaging principles are now driving packaging innovation in this fashion?