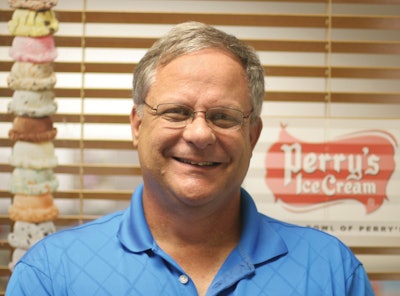
Packaging professionals undoubtedly will face many new ideas on how to bring their product to the customer. Though a new package may look appealing on the surface, a prudent professional will walk the package through the entire process, from raw material receiving to the customer, to ensure all obstacles are identified along with solutions to overcome them.
Let’s start with raw material receiving and ask ourselves, “How are we bringing this package through the door?” Do we know how the load will be unitized? Will it actually fit coming from the truck through the door? Maximizing a tractor-trailer load is desirable to save on freight costs, but it also could cause ergonomic issues downstream without an effective method for de-palletizing the load and preparing the packages to be filled with your product.
When it comes to filling machines or cartoners, does your package structure conform to what the OEM has engineered the machine to handle? I once had the unpleasant experience of discovering that a UV coating on a folding carton would not feed properly from our cartoner magazine into the filling station, no matter what adjustments we attempted to employ. Changing to an aqueous coating provided the proper COF and eliminated the double-feeding. I highly recommend testing mockup cartons in your filling machines to ensure proper form, fit, and function.
Speaking of graphics, if your line is employing bar code readers or a vision system, make sure you understand the limitations of those systems. You should allow for tolerance in your bar code placement on the package to ensure you are not expecting to read codes that are consistently at the far edge of the scanner’s range.
Walking further into your process (we will save conveyors for later), we come to unitizing and protecting products for shipment. One goal of your secondary packaging is to protect your product while in storage or shipping. To that end, you need to spend time ensuring the flute size you choose will support the stresses the package will endure in storage and distribution. Ask the following questions: How will these packages be stored pending shipment? What sort of movement can the load be subjected to prior to arriving at its final destination? What environmental conditions will the load be subjected to?
Your answers to these questions will go a long way toward deciding which design, structure, and coating will best protect your product.
Another consideration: How will the item be palletized? Will you manually palletize or will you have robotic capability? Ask yourself, what are my limitations and how can I overcome them while still maximizing the load? Ergonomics is a key factor when manually palletizing. Be mindful of your pallet configurations and design them to minimize the over-the-head placements and twisting motions.
Conveyors are the quintessential piece of machinery for moving your product from one operation to another. Be it a new installation or working with a package modification on an existing system, testing conveyors with package mockups is essential to proving the process prior to the first run. Be sure to include the actual weight of your intended product in the mockup. You can then run your mockup through your conveyor system to determine your obstacles.
Watch your package closely as the conveyor moves it. Does the package catch somewhere that may require an additional guiderail or modification to an existing one? Does your package clear any openings in walls that your conveyor system runs through? Are you accumulating correctly in the intended zones? Thorough testing of your conveyor systems will pay big dividends down the line.
What I have discussed in this article is in no way inclusive of everything you should be aware of when introducing a new package in your operation. At Perry’s Ice Cream, each of our plants has its own uniqueness, and it may require more or less areas that need to be addressed. The key thought here is the need to walk your new package through the entire cycle. Subtle things can change in your plant, and you discover them only by walking through the process and through careful testing.
About the Author: Michael Lovelace is a Material Reliability Technician at Perry’s Ice Cream.
For information about IoPP, visit www.iopp.org.