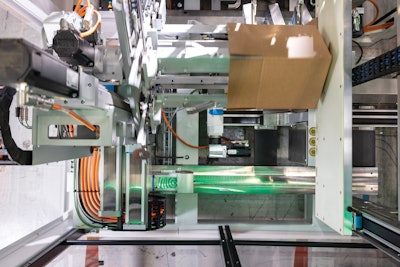
When Bill Crutchfield founded his company in the family garage in his hometown of Charlottesville, Va., in 1974, he was trying to fix a problem he’d experienced as a customer: how do you figure out which aftermarket car stereos and speakers will work in your vehicle? He realized that expert information, shared by people who really cared about problem-solving, was the answer. More than six million customers later, those principles continue to drive the business, which now serves the entire audio/visual device and consumer elecronics technology space.
Crutchfield has since grown to employ more than 700 people, and now runs the vast majority its business as D2C out of two 120,000 sq. ft. facilities, both in Virginia. Crutchfield’s impressive offering of online sizing tools and online customer support dovetails nicely with e-commerce and D2C sales, which have grown exponentially over the past decade. Since 2013, the A/V equipment and device company has been growing and evolving its D2C operations with Packsize (see sidebar). But an all-new installation, the Packsize X5, is the next evolution of that journey.
As Packaging World recently reported, Walmart was an early adopter of Packsize’s new X5 system for right-sized packaging on-demand that the supplier says efficiently produces ready-to-pack, right-sized erected cases. The retail giant uses this system within proprietary Ultra5 machines. Now, the full Ultra5 machine equipment was designed for, and remains exclusively available to, Walmart. This equipment is being rolled out to its next generation of fulfillment centers. But the X5 system the Ultra5 is modeled after is available for any Packsize customer. Given Crutchfield’s nearly 10-year history with the e-comm specialist, it wasn’t long before they chose to capitalize as well.
“I was a pretty early adopter, myself,” says Chris Groseclose, chief fulfillment officer, Crutchfield. “As soon as they were starting to offer them out of the beta environment, I was one of the first people that had my name on the list for one. I had a good relationship with their sales rep. She’d been with us for several years and there’s a lot of trust since they’ve been strong business partners over the years. She showed me some demo videos, and I was ready to sign up for one.”
Labor savings and flexibility
It wasn’t that big of a leap for Groseclose, either. The Crutchfield facility had already been running a handful of Packsize’s X4s, which Groseclose describes as the supplier’s first version of a more automated box-sizing system, and predecessor to the X5.
“And that equipment carried our business for three or four years,” Groseclose says. “But they start to age out, and repairs and upkeep are needed. When I saw that they had taken everything they learned from the X4 and put it into the X5, that was reassuring.” Packsize’s X5 equipment at Crutchfield runs at about 425 to 450 erected, bottom sealed cases per hour, each cut specifically for a unique order.
For instance, the X4 allows for two different corrugated tracks, or fanfold widths, on the corrugated input feed. The X5 doubles that number to four, and Crutchfield currently uses all four of them on the new system. The corrugated spec used in this facility is 32 ECT with standard fluting.
“Having more fanfold width options really helps you dial in your box size and reduce your waste,” Groseclose says. “Also, they’ve simplified this model where the corrugated just runs straight through the line and just doesn’t move as much as it did in the legacy equipment. And the cutting head system on the X5 is simpler. All in all, they’ve simplified the machine, increased the fanfold widths that you can input, and increased the output. And frankly, with the equipment itself being able to inject a box onto the conveyor, with a bottom that’s fully glued with the Box ID label already on it, they’ve really eliminated two- or three-people’s worth of labor. Those people were involved with getting boxes out of the previous versions of the machine, folding them, taping the bottoms, and putting the labels on. Packsize has taken a big jump toward a value-added automation.”
The new equipment
The new X5 equipment provides right-sized cases for Crutchfield orders in all three dimensions: length, width, and height. This equipment is capable of more than 500 cases per hour, but considering the size of the cases used and Crutchfield’s specific needs—it has other case erecting equipment—the facility more commonly averages 425 to 450 cases per hour.
As Groseclose mentioned, the system uses the four corrugated fanfold infeed tracks in varying widths to optimize case sizes during erecting. The machinery operates by connecting with the CPG or fulfillment centers’ WRS or ERP systems—the X5 receives specific case size information for each order, and then executes on cutting and erecting to that size. Size availability ranges from 8 x 6 x 3 in., to 30 x 20 x 20 in., and the equipment can produce the largest size immediately after the smallest or vice versa without any variation in production rate, much less need for changeover equipment. Cases are essentially formed from rollstock of contiguous corrugated, with four different fanfold widths being infed into the system.
After cutting the 2D corrugated to the correct dimensions, the system then erects and closes case bottoms with adhesive. Then, pressure-sensitive print-and-apply Box IDs with the item’s dimensional information—unique to every single case—are automatically tamp-applied to the erected corrugated cases.
Notably, right-sizing cases results in some scrap corrugated. This is minimized by optimizing the fanfold width, but small pieces remain. The removal of these excess scraps is also automated, with a conveyor carrying them to a gaylord that can be managed throughout the day during production and recycled with any other outgoing corrugated material.
Downstream equipment
At the Crutchfield facility, erected cases exit the Packsize equipment onto a 24-volt Intelliroll conveyor from TGW Conveyor Systems, which serves as the base of the whole system of pick zones that ensues. Scanners from Cognex read the individual Box IDs, which connect with Crutchfield’s systems and builds the pick path for any given case. Once that pick path is constructed, which is almost instantaneous, that information is fed back to the conveyor’s PLC, and the conveyors “decide” into which pick zones each case needs to travel.Pressure-sensitive print-and-apply Box IDs with each item’s dimensional information—unique to every single case—are automatically tamp-applied to the erected corrugated cases.
“Through COVID-19, I had to add extra pick zones, so now I’ve got 12 of them. We use six scanners at the induction to each zone,” Groseclose says. “And [the system] knows whether to direct a case into each of the zones. As the case travels by the set of scanners at the front of each of the zones, the case gets scanned and the conveyors recognize ‘Yes, it needs to go in here,’ and it does. Or ‘No, it doesn’t need to go here,’ and it will pass that zone by. The cases that go through that system come to a final scan that says, ‘Yes, everything is in this order, we’re going to pass it down to shipping,’ or, ‘No something went wrong. We’re going to recirc it through the whole system and let it have another chance at getting it right.’ Sometimes, if a zone is completely full, a case will wait 10 seconds, and then it’ll pass around and do a recirc of the whole system until it comes back around to the zone, usually then there’s an opening for it.”
Once a case is cleared to ship, it first passes manual void fill application stations. The company uses water-soluble, packing peanut-style fill made entirely of starch.
Why would perfectly cubed and sized cases require void fill, you might wonder? That’s a good question. Crutchfield runs the Packsize equipment to an 80% fill spec. That means the cases are designed to be cut to a size that’s filled to 80% of its available space, once all the products are picked and placed to the case. But why 80% and not 100%? That’s another good question. The answer lies in the fact that this Crutchfield facility is a fulfillment center that receives custom orders—multiple differently sized and shaped products are often expected to fit into a single case.
“At 100%, when there’s one single item going into the box, it will cube that box out absolutely perfectly,” Groseclose says. “But we’ve found that with two or three items, if you go with 100%, it can become too much of a game of Tetris for operators trying to figure out how to place items in the box in such a way that optimizes the use of space. So today, we run it at 20% void, I guess you’d say.”
Plus, according to Groseclose, the Packsize X5’s PackNet Cube software is smart enough to know when there is a rectangular single item, like a Sony receiver in a rectangle-shaped primary package. On those occasions, the Packsize reverts to the 100% fill, bypassing the 80% request. The result is a perfectly cubed secondary corrugated case, and the primary package fits snuggly within, with no need for void fill.
After void fill is added as needed, the cases travel through one of two Pearson case sealers. Groseclose says these are are fully randomized, automatic case sealers ready to accommodate any case sizes that the Packsize could throw at them.
“We had manual, pneumatic sealers, but the Pearsons run three cases to every one case that ran through the manual, so we just switched over to letting two Pearsons run the case-top sealing,” Groseclose says.Cases potentially get a manual application of void fill, when necessary, before top closing, weighing, rates shopping, and routing to the correct carriers.
After each Pearson, the closed cases run across a weigh-in-motion (WIM) system, and another Cognex vision system reads both the Box ID and the weight. That begins a process of rate shopping for a carrier to get the best shipping price for a given case.
“Our system does a theoretical weight, and then matches it to the actual weight,” Groseclose says. “If a certain percentage threshold of variance is met, it’ll kick it to an exception line and won’t let it ship. Once the rate shopping is complete—we do a bunch of different sorts for UPS, FedEx, postal, and air shipments—they run by two print-and-apply systems that attach shipping labels, and the case then travels to a 10-lane TGW belt sorter.”
What’s next for Crutchfield packaging
“I think not too far over the horizon, we would add another X5 system,” he says. “Where I am right now, I have three EM7s [simpler Packsize case erectors], one X4, and one X5 in this facility. I’d like to get rid of the X4 and one or two of the EM7s, and just have two X5s running the front end of it. If I had two of those in place, that puts me close to 1,000 cases an hour just with those two, and then generally that’s enough to get us through the day. I would keep some EM7s around just for supplemental volume during the holidays.”
Groseclose is also in the beginning stages of looking for Automated Storage and Retrieval System (ASRS), also called a goods-to-person system, that could potentially replace the whole conveyor piece of the existing systems.
“And I think this X5 will play in really well with that,” he says, “It’ll be a great fit.” PW