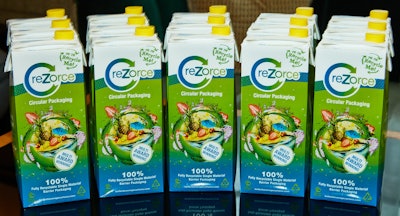
Court Johnston, president, Mucell Extrusion, a division of Zotefoam PLC, spoke to PW today about the tech.
PW: What is microcellular foaming tech, and what was its genesis? I believe an early, in-market example was the development of a lightweighted pack for Unilever brand Dove, correct?
Johnston: This really goes back to 2011 when Zotefoams acquired MuCell Extrusion. Microcellular foaming technology is where we inject atmospheric gasses into polymer, typically nitrogen and carbon dioxide, and we displace 10 to 15% of the weight, creating lighter, greener, cheaper packaging.
Fast forward to 2019. In the intervening years, you've been able to develop layers of this microcellular foam in HDPE specifically. And when laminated or otherwise stitched together, these layers can provide barrier properties. What are you doing to achieve this?
What we're doing is creating a mono-material, barrier, food-contact packaging with a layer structure. We can create up to nine layers within the gauge of a chip bag. We're able to include recycled material [HDPE PCR]. For mechanical recycling work streams, about 70% of the substrate would be rHDPE. With chemical recycling inputs, that's almost 100% recycled material.
You're able to make a lot of different packaging substrates--both rigid and flexible. You already mentioned chip bags, but stand-up pouches and other flexibles are on the menu. But you're launching into rigid aseptic cartons first. Why is that?
There was a lot of discussion. There are many markets that this technology lends itself to. We've prioritized aseptic carton for three reasons.
The first is the market size. 300 billion aseptic cartons are consumed around the world every year.
Second would be market concentration. Three players in Tetra Pak, SIG, and Elopak represent about 90% of that market.
The third reason, which I found particularly interesting when I was looking across all of the packaging segments, was the market conduct. This is the only market segment which isn't talking about recyclability and circularity. Really the emphasis was on carbon footprint only because of the nature of the composite [70% fiber, 20% PE, 5% aluminum] material. It is designed to be, and only can be, single-use.
So this is a multilayer structure, but it's a mono-material. I assume this can go into existing curbside recycling streams? Do material recovery facilities (MRFs) want this material? Have you partnered with them?
The short answer is yes. One of our strategic partners is Biffa Recycling [and Waste Management] in the UK. It's the largest recycler of mono-layer HDPE milk bottles in the United Kingdom. We've tested the circularity extensively, through their laboratories and their MRFs. They operate a closed-loop system, which is really the highest bar in mechanical recycling, and reZorce passes those tests.
So you're working with MRFs already, making sure this is a recoverable material on the backend to become a carton or other PE-based packaging again. What do input streams look like? Where are you sourcing virgin material for the virgin, food-contact layers? And do you have off-take agreements in place for the high amounts of rHDPE PCR you hope to use? Maybe Biffa is feeding back rHDPE as feedstock?
From a virgin perspective, in North America, it's ExxonMobil. In Europe, SABIC and Versalis are our key partners. From a recycled material perspective, we have a strategic partnership with Biffa, again, the largest recycler of HDPE milk jugs. We have signed allocations of rHDPE for the reZorce substrate, too.
The way I like to think about it, every single reZorce carton that is sold, is additional high-quality feedstock for Biffa or other MRF partners. So we're looking at those huge volumes across the world, talking about 300 billion cartons being consumed. If those cartons become HDPE instead of single use, that's all upside for the recycler.
![]() | END USER REFRESCO: "We are indeed working with partners to win. What we see has changed over the past years is that our customers--we work for basically all of the large retailers in Europe, North America, and Australia, as well as all the large A brands--they are all looking for more sustainable solutions. They're looking for choice, they're looking for recyclability, and they're looking for recycled content, and they're looking for a partner who is willing to be a front-runner and is looking to take some risks in order to take a step forward. This format, reZorce, allows us to be the front-runner we want to be." -- Coert Michielsen, CPO, Refresco |
Why should brand owners, CPGs, retailers, and contract packagers be interested in this technology?
Everybody, brand owners, CPGs, and retailers, are working really hard, and doing a great job in redesigning their packaging to be recyclable. A challenge is recycled content. What we're seeing are public statements and pledges from the CEOs of the biggest brands on the planet to get to 25 or 30% recycled content by 2025. But in the Ellen MacArthur Foundation Progress Report, the latest of which was issued in November 2023, the evidence shows that they're really struggling to meet those targets. And that's for a couple of reasons.
The first is the lack of availability of high-grade, even food-grade recycled material. It's scarce, It's expensive.
The second is food legislation that requires virgin material to be in contact with the food. So unless you have that multilayer substrate, that's a problem for them.
The reZorce substrate addresses both of those issues.
Can you be more specific on how, structurally, it does so? My understanding is that you're using virgin HDPE for the layers on the interior, where contact with the food is made. And you're using virgin on the outward-facing print layers for a great shelf impact. But the internal layers can be rHDPE, correct? "This package that I'm holding today actually has 30% rHDPE in the substrate," Johnston says.
That's exactly right. We actually stitch and hem the internal layers with recycled content so that there can be no contamination of the virgin layer. Imagine that the initial layer, in direct contact with the food, would be virgin polymer. Typically, you'd have a barrier agent in the next layer. We would then have a layer of nitrogen, and then as many layers of recycled content as is required. This package that I'm holding today actually has 30% rHDPE in the substrate.
What kind of equipment does this material run on? If a brand owner or contract packager were to offer this format, would they require all new equipment, or could they retrofit existing equipment? Essentially, how easy is deployment?
We recognize that for new technology adoption, there are, in principle, two issues.
One is complexity of the change, the other is the cost of the change. What's great about the reZorce technology is that it's fully scalable using the existing plant equipment with some very minor modifications. For example, the packaging that I'm holding here, the longitudinal seal, is a flame seal, per the market standard. The top seal is ultrasonic, per the market standard. The modification that we're making is to the bottom seal. Instead of being an induction seal process, it is ultrasonic.
Editor's note: The company revealed about a two-day changeover from existing liquid packaging board (LPB) to the new format, upon first changeover. Ensuing changeovers would be simpler.
You have a major juice CM/CP partner in Refresco who's helping to bring this product to market. Tell us about them, their scale, and what they do.
We signed a joint development agreement with Refresco in July 2023. Refresco is the world's largest independent packager and filler of juice. They have revenues of about €4 billion per year across 74 plants in Europe, North America, and Australia. They've given us unfettered access to one of their plants, a filling line, to enable us to test and trial reZorce packaging. We're in the final stages of that validation process, and I would expect us to be on the shelf in the next financial quarter.
Is HDPE the only material that could benefit from microcellular foaming tech?
There's a huge opportunity here. We prioritize HDPE due to the availability of high-grade rHDPE in the world. But we're now developing a polypropylene and PET version. We're developing different sizes, too. This is a 1.5 L pack. We have a 1-L and a portion pack to launch soon.
![]() | END USER REFRESCO: "If you look at the groups of customers that we have, about two thirds are the large retailers, and about one third are A brands, what we clearly see is that the A brand owners are pushing for circularity themselves. They want us to come up with a circular solution, and they are very demanding of us--rightfully so, because it's part of their brand and positioning. For the retailers, we play more of a product developer role, and we are supposed to come up with circular solutions. They compare us with other bottlers, and other beverage solutions providers and see who has the best option. So we have to offer them business solutions, we have to offer them choices, and they want them to be within a competitive price and high quality. We need to come up with a solution that brings that all, and I believe that with this reZorce pack, we have a new option that they will certainly appreciate." -- Coert Michielsen, CPO, Refresco |
The substrate is non-wicking; what does that mean?
It means it's microwavable. And that's a new category for cartons. Obviously, that's something that the current aluminum-containing composite doesn't permit.
What kinds of markets are you looking at, and where?
We're looking at juice in Europe. In North America, we'll be looking at dairy alternatives, soups, and broths. And there are a number of other categories.
What about shelf appeal? Brands and contract packagers can't ignore the consumer desire for packaging that looks good and stands out in a competitive set. Is there anything different about printing for the consumer-facing outer printed layer?
One of the things that brand owners tell us is that the current market practice is to have very long runs of printing to minimize costs. What that does is it restricts the flexibility and agility of printing decoration. With reZorce, we're going to offer mass customization. We've tested and validated all of the printing technologies, whether that be digital, flexographic, or rotogravure. We actually printed the carton in front of me with a reverse-laminate BOPE solution, so it is very flexible, and mass customization is the goal."The way I like to think about it, every single reZorce carton that is sold, is additional high-quality feedstock for Biffa or other MRF partners," Johnston says.
That begs the question, there are a lot of converters out there that could help you scale. Have you any partnerships there?
We've just announced today that we've signed an agreement with SÜDPACK in Germany. that gives us access immediately to a capacity of 100 million cartons. There are others that we're talking to both in Europe and in North America, so they're watching the space.
One link in the chain or rung of the ladder that we haven't yet discussed is the consumer. Have you done any research on consumers' appetite for this new pack format? Will you have to educate them about it and ensure they properly dispose of it?
We plan to run a 150,000-carton trial on supermarket shelves imminently. That will be our first playback from the consumers on how they differentiate the reZorce vs. the liquid packaging board (LPB). What a retailer has agreed to do is actually merchandize the package immediately next to the current LPB market standard, so we'll get some very useful market research and feedback.
How do emerging regulations play into this rollout? This new substrate, with its ability to simultaneously carry PCR in mono-material rHDPE, and be food contact. That hasn't existed before, to my knowledge.
The regulatory framework really tees up the opportunity that's presented by reZorce. What we're seeing from governments is a drive for extended producer responsibility (EPR), so we're expecting, from a P&L perspective, that this will be a big winner for brand owners and the CPGs. PW