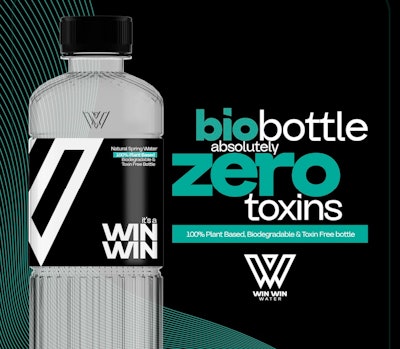
U.K.-based Win Win Water is making waves in the bottled water market with a new 100% plant-based, industrially compostable bottle. The entire package, including the cap and label, is made from polylactic acid derived from sugarcane and supplied by TotalEnergies Corbion.
“Win Win Water was established with a mission to revolutionize the bottled water industry by combining purity, sustainability, and social responsibility,” says Joshua Daley, company director at Win Win Water. “The market is demanding change, and as plastic becomes public enemy number one, we’ve taken a step toward a better solution.”
The choice of Luminy PLA was no accident. “We looked at every material available,” Daley explains. “Right now, Luminy PLA is the winner in every metric. It is the safest and most environmentally friendly option available.
![]() | Read about another compostable bottle, this one from organic grocer Erewhon and Cove, in this related article, “Biodegradable PHA Water Bottles Make Retail Debut” |
“The absolute factor for us is human health. Why are we forced to drink millions of PET microplastic particles with every bottle or can of water? PLA offers a solution.”
The bottle is made from Luminy PLA. This bioplastic is, according to TotalEnergies,100% non-GMO and produced from sustainably and ethically grown sugarcane. The cap is made from a proprietary PLA compound developed by one of TotalEnergies’ partners.
As Derek Atkinson, VP of sales and business development at TotalEnergies Corbion, explains, the bio-based material provides a 75% reduced carbon footprint compared to petroleum-based plastics, with sugarcane crops absorbing carbon during growth and storing it in the material. “The biogenic carbon from the sugarcane is transferred to the value chain, ensuring a lower environmental impact,” he says.
One of the biggest challenges with using PLA for beverage bottles has historically been heat sensitivity, but for bottled water, Atkinson says it’s not an issue. “High heat-deflection temperatures are not required for water bottles, so this is not a concern here,” he explains.
Win Win’s bottles have been designed to break down within 90 days in industrial composting facilities but are also durable enough for multiple reuses.
While the current production doesn’t include recycled PLA, Win Win Water is exploring the incorporation of rPLA in future runs. TotalEnergies Corbion operates its own chemical recycling plant that uses a depolymerization process via hydrolysis to recycle post-industrial and post-consumer PLA into lactic acid used to produce new, virgin-quality PLA.
“Our technology ensures that over 95% of the carbon in the incoming waste is returned as virgin PLA, which is far more efficient than recycling polyolefins,” says Atkinson.
As Daley relates, developing the bio-based water bottle hasn’t been without its challenges. “We have spent hundreds of thousands of pounds over the last three years to make this possible,” he says, but the response, he adds, has been “amazing.”
“The next generation of young adults gracefully demand healthy, forward-thinking innovation, and it’s great to feel the love for trying to impact the world in a positive way,” Daley say.
Win Win Water is available in the U.K. and Austria; the company has a goal of expanding worldwide by 2027. PW