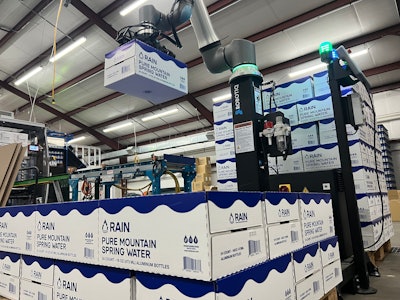
Rain Pure Mountain Spring Water, a producer of naturally sourced water that uniquely bottles exclusively in aluminum, was born with an eye on packaging’s role in sustainability and recycling. During his early days as a mechanical engineer, Mark Majkrzak, founder and CEO, took note of the increasing volume of plastic used by single-serving drinking water brands.
“I used to consult for big bottling companies as an automation engineer. My role, I'm sometimes ashamed to admit, was to take a plastic bottled water facility from 1500 bottles a minute to 1600 bottles a minute. Generally, my scope was to do that with low or no capital. We would look for the fringe opportunities where there were incremental savings. Those small improvements would stack up pretty quickly when you're talking about 1500 bottles a minute. I did that for a long time, and that's what drove me to have a profound appreciation for the plastic problem,” Majkrzak says.
While aluminum is more expensive, it’s much more frequently recycled by consumers. It also often consists of a high content of recycled material, and doesn’t degrade over recycling cycles. For those reasons, it can be said to be more circular, and a certain set of consumers are willing to pay more to participate in a circular packaging economy. The recyclability and economic viability of aluminum, along with the material’s aesthetic (printed cans) and functional (gets cold quickly) perks, drove Majkrzak to start a company that bottles water in aluminum.
Rain sources water from its own spring and bottles it at its facility in Tiger, Ga. The company’s earlier target markets have included upscale institutional and hospitality locales like hotels, college campuses, and foodservice operations, but Rain is expanding into more of the traditional retail market as well.
Now that he’s working with a product and package that he feels better about from an environmental standpoint, Majkrzak continues to flex his engineering muscles at Rain. He recently improved automation across an entire packaging line, but palletizing was a big pain point that required some extra help. The company found it with Robotiq’s integrated palletizing solution that included a six-axis articulated arm from Universal Robots (UR).
Palletizing hybrid benefits Rain at end of line
The Robotiq PE20's integrated solutions align with Rain's operations and standards.Image provided by Rain
Rain previously performed its end-of-line palletizing manually, where employees stacked corrugated cases of aluminum water bottles. This required the company to manage more SKUs and presented physical challenges to employees. Still, space constraints meant that adding a bulky machine to automate case stacking was not ideal.
But Majkrazk took note of software implementation, ease of use, and convenience improvements in the robotic palletizing market, which led his company to acquire a Robotiq PE20 palletizer equipped with a UR20 arm.
Majkrazk says Rain considered buying a UR arm directly and developing its own palletizing system. But Robotiq’s turn-key integrated PE20 solution, which included an articulated arm, a palletizing platform, and a user-friendly system was the best fit.
In addition to the palletizer being cost-effective and easy-to-deploy with a short lead time, it allowed Rain to increase efficiency and upskill its existing workforce.
“[Manual palletizing] was an ergonomically unfriendly task. These cases are 30 pounds when they come off the line, at six cases per minute. We had two operators doing that job, and on a shift, they might lift a hundred thousand pounds… And it’s beyond the ergonomics. It’s such a mundane role,” Majkrzak states. “Those operators now have forklift certifications and have been reallocated to other areas of the plant where they were needed.”
The PE20 palletizer runs only on 120 VAC and compressed air. In addition, it is compact enough to fit within Rain’s space constraints and features a safety scanner that eliminates the need for bulky additional guard rails or caging. The safety feature allows Rain to comply with OSHA regulations, but Majkrzak says employees are also trained on the robot’s operation path to ensure safety.
The palletizer also has a “grouping” feature that optimizes and reduces space between cases as it packs. The wrist of the palletizer’s robotic arm uses a force sensor to intentionally collide with a stacked case to gauge unnecessary space and eliminate it, as seen in the video below:
The palletizing solution’s software capabilities and paired support reinforced Rain’s decision to add it to the packaging line.
“I think Robotiq has a really effective solution and great support. And it’s fine for a do-it-yourself-er of integrated solutions, like me. We didn’t have anyone come out to our facility. We called their tech support a couple of times when we were setting it up, but we had that robot palletizing the day it arrived,” Majkrazk says.
Rain’s end-of-line palletizing process has been a major boon to Majkrazk’s company, but it wasn’t the lone improvement on the line. In fact, the entire line is less than a year old, allowing for increased throughput and speeds across the board.
Upstream improvements
Rain sources its printed aluminum bottles, which are transported to RAIN’s facility by the truckload, from Ball. Each truckload contains roughly 130,000 cans, and the company brings in around eight trucks, or a million cans per week, according to Majkrzak.
The bottles enter a warehouse and are unloaded with a high-level GR-X Machinery (acquired by Ska Fabricating) depalletizer equipped with an s-curved, side-grip lowerator. Majkrzak notes the lowerator is better suited for Rain’s aluminum bottles than a traditional twist cage commonly seen in aluminum canning operations since the aluminum bottles have a tapered neck.Depalletized bottles are single-filed and lowerated before air rinsing and filling.Image provided by Rain
Next, Rain rinses the aluminum bottles with ionized air and conveys the bottles into BevCo bidirectional mass accumulation tables. The bottles travel to a positive-pressure room that contain high-efficiency particulate air filter (HEPA) handlers, which blow clean, dry air into the room 24 hours day. Here, the bottles make their way toward a 24-valve GAI rotary filler, which disperses sourced spring water. Rain previously used an 18-head filler but needed an upgrade.
“We were finding that we needed a little more speed. We don’t have a monoblock here, and the [new downstream] capper can [now] outrun the 18-head filler, so we upgraded valves. We also got some better material handling. The 24-valve filler has a longer screw, so we can take control of the bottles a little earlier coming off the mass accumulation. It’s technically a light depression filler, but it’s being used as a gravity filler because this is still water with no carbonation,” Majkrzak says. Filling on a 24-head rotary filler.Image provided by Rain
Majkrzak further explains that there is less of a need to cap bottles immediately like breweries do.
“It’s not [a worry] because it’s still water, and we’re not worried about any oxygen pickup, and then we're going to dose it with liquid nitrogen to remove that oxygen in the head space regardless. We have some dwell time, maybe 15 conveyor feet, probably around 10 or so seconds of conveyer time between the filler and the capper. And so, there’s a small accumulation coming out of the filler and the head of the capper,” Majkrzak adds.
Once the bottles make their way to a new five-head Arol rotatory capper, they receive a treatment from a Chart liquid nitrogen injector, which sits on the inside frame of the capper. The nitrogen flushes oxygen from the bottle’s headspace ahead of capping and ensures quality while adding rigidity to the lightweight can.
Majkrzak says the capping machinery is unique due to the aluminum bottles’ special requirements.
“The capper is the single most specialized piece of machinery to bottle this container,” the CEO states. “Because it’s a lightweight aluminum bottle, you can’t apply too much torque. You’ll ovalize it. So the capper is a dual pass, sometimes called a dual cam system.”Bottles receive an inert gas headspace flush before caps are gently torqued into place.Image provided by Rain
The first pass is a process that causes the bottle minor deformation and creates threads on the bottle’s top for ROPP capping heads to sit on. The second pass is the precise application of the cap to the bottle.
The bottle exits the filling room, receives a date code and lot number from a Markem-Image inkjet printer, and enters another accumulation area ahead of a PC-2000 intermittent motion wrap case packer from Arpac, a Duravant company. The packer cases roughly 130 cans per minute (CPM) and has helped Rain save in costs.
“What’s good about the case packer is that it uses a flat blank of corrugated, and so our packaging costs came down significantly. We were using a drop packer, and that meant two things. One, there was an operator erecting cases feeding that machine, and two, it was a more traditional retail slotted case (RSC), which meant it was folded and glued. The blank size is similar case to case, but the cost is quite a bit different, about a 40% price difference, because our vendor no longer has to fold these boxes, they’re just cutting them on a rotary die, stacking them on pallet, and shipping us printed blanks,” Majkrzak explains. “We used to get 400 boxes on a pallet. Now we get 700 on the same inbound pallet of cases, and we can put about 40,000 cases on a truck.”
The Arpac PC-2000 case packer's speed and efficiency has helped Rain to increase its throughput.Image provided by Rain
The Arpac case packer handles 12 and 24 packs of Rain water. Eventually, the packed cases get sealed and ready to be palletized by the Robotiq solution. Each completed pallet contains 70 cases of water. Employees forklift the pallets to an Orion stretch wrapper for concealment, marking the end stage of the production line.
Rain’s aluminum water-bottling process is intricate, and several pieces of machinery, including the PE20 Robotiq palletizer, are helping the company meet demand and experience growth.
As consumers stay on the hunt for sustainable bottled water solutions, RAIN intends to continue to develop and refine its production process to ensure high-quality, eco-friendly products while expanding its capacity to serve more customers. PW