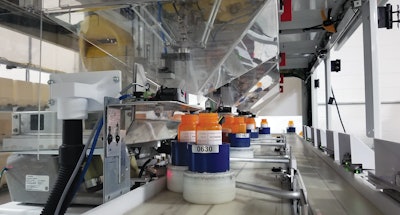
Some time ago, the Department of Veteran’s Affairs (VA) decided to automate its prescription fulfillment processes. The VA fulfills thousands of orders a week and millions over a year. To handle this, they entered into an agreement with an American integrator to help construct their vision.
The VA’s vision consisted of two separate facilities, each with several lines of modular cells, and each module with two halves. The first half would be for storing and retrieving pill canisters. An external carousel-style shelf would store canisters capable of holding up to 200 medications for later fulfillment. A 6-axis robot mounted to the module would oversee the movement of the canisters to and from fulfillment. On the other half of the module, four delta robots would fulfill orders. Once a canister was received, they would activate a vibration table and vacuum system to disperse capsules and remove lingering debris. Then, the robots would pick up the capsules and drop them into the bottles below, one by one. Upon completing an order, a series of conveyors and diverters would remove the bottles for further processing, such as labeling and sealing.
![]() | Read a related article from this year’s Robotics Report, “Pharmaceutical Industry Enlists Packaging Robotics.” |
These modules were envisioned to work in tandem to plan and fulfill orders as they came in. However, the modules designed by the integrator were far from reliable, even after seven years of design and testing. They failed on multiple levels. The robot tool could not grip some pill types, flinging them around the module. The constant flinging and accumulation led to the rapid degradation of some of the hardware due to the trapped pills and dust. Additionally, the design made basic repairs nightmarish because so many components were trapped behind layer after layer of bulky hardware, leaving maintenance workers with no way to remove the debris.
In short, after seven years, the integrator was never able to finish the project. Despite the VA’s initial investment in equipment and support services, a series of automation problems led to the non-renewal of their contract with the integrator, leaving the infrastructure unused and unsupported. However, with the massive sunk cost, the VA opted to retrofit the existing systems to address some issues. Universal Logic was awarded the job and has been working to bring the system online as soon as 2024.
Packaging robotics retrofit addresses the VA’s pain points
To effectively address the VA’s immediate problems and understand their root causes, it was crucial for Universal Logic to clearly understand its pain points. Originally, the design aimed for easy production of 20 units, resulting in a modular approach where each piece was designed to perform a specific task. However, when these pieces were assembled, they lacked compatibility, causing numerous issues. This meant that not only did Universal have to mitigate the problems of the original integrator, but they also had to fundamentally change their approach.
Universal’s initial priority was pill management. To prevent pills and dust from building up on the conveyors and inside compartments, Universal needed a solution to prevent them from falling in the first place. This change meant redesigning the robot’s end-of-arm tool (EOAT) to maintain adequate suction with each medication. Once the new tool was complete, a funnel was installed around the robot in the event of a flying capsule. If one happens to escape the funnel, it will fall into a catch pan below the robot; the catch pans act as the final defense for medications that may escape. The pan ensures that even if the tool malfunctions, dust and pills won’t accumulate on the other components.
Additionally, to prevent problems with new medications and capsule shapes in the future, Universal has designed a state-of-the-art training station that allows new pills to be trained by size and shape with Neocortex, Universal’s patented AI, for a seamless transition into production. The training station will also allow future operators to test other settings, such as robot speed and vibratory frequency, for more efficient operations and less downtime. Integrating Neocortex here and on the cell for robot picking and identification gives it more robust error handling than before. With Neocortex, the robot can identify minor differences between pills if one is in the wrong canister; it can even detect brakes or chips and avoid these pills for fulfillment.
Foundationally each change made has radically improved the process or overall efficiency. Since the improvements were made, the longevity of the system has improved. However, the system has also become more complex. One of the biggest challenges for the original design was the inability to do regular maintenance. To combat this problem, Universal removed the existing conveyor and hardware that previously handled traffic control. In doing this, they opened access to the robots, the vibratory stands, and other internal components for maintenance. Reducing the number of vibratory stands and pick locations to just one per robot further opened space so that an operator can manually intervene in an emergency. These changes improve the system’s efficiency and make maintenance more accessible, allowing for regular upkeep and uninterrupted operations.
On the canister side, the theme of simplification persists. The original rack was designed to hold almost 200 medication types on an integrated carousel shelf. While this design certainly had more storage, the rack would often become misaligned, which prevented the robot from adding new canisters and would result in hours of downtime while the robot was recalibrated with the shelf. To negate this problem and ensure appropriate alignment, Universal designed a new canister rack with fixed shelves that provides constant alignment and zero variability in the canister locations. This solution effectively addresses the misalignment issue, ensuring seamless operations and eliminating potential downtime caused by recalibration.
![]() | Read this related article, “Robots’ Hygienic Features, Precision Spur Pharmaceutical Applications,” from Packaging World’s 2022 Robotics Report. |
Universal’s retrofitting of the existing pill fulfillment automation system exemplifies the challenges and complexities associated with upgrading and improving established infrastructure. The VA’s decision to retrofit was driven by the significant investment already made, along with the potential to salvage the existing equipment. Through a strategic redesign, Universal successfully addressed various issues that plagued the original design, including pill management, maintenance accessibility, and canister misalignment. PW
![]() | Read Packaging World’s complete robotics report, “Robots 2023: Smarter, More Adaptable & More Robust.” |