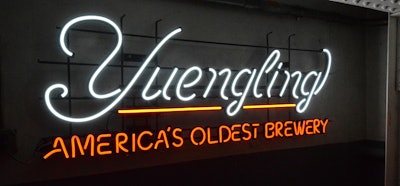
At over 150 lb, a half-keg of beer is strenuous to handle. That’s why more than 20 years ago, the D.G. Yuengling and Son, Inc. brewery—known as America’s oldest—made its first foray into automation when it incorporated industrial robots on its keg-filling lines.
Fast forward to the present, and Yuengling recently replaced those original robots with new state-of-the-art models. The replacements, installed in April 2023, are faster and even more robust, save time, consume less energy, provide easier maintenance and, like their predecessors, are extremely reliable, as well as reduce the risk of operator injuries.
![]() | Read related article from this year’s Robotics Report, “New Palletizing Solutions Incorporate Cobots.” |
“We basically wore out our original robots. Just their ages and the number of hours on them justified the need for updated automation,” says Bill Friedman, electrical services manager at Yuengling’s Tampa, Fla., facility. “Plus, people don’t want to handle kegs all day, and there’s always a risk of injury.”
In 2003, Yuengling installed two industrial robots from Kuka Robotics into the keg line at its Millcreek facility, located in Pottsville, Pa., not far from the company’s original brewery, founded in 1829 and still in operation. Then, in 2006, the company added a Kuka robot to the new keg line in its Tampa plant.
Yuengling is currently owned and operated by Jennifer Yuengling, vice president of Operations and a great-great-great-granddaughter of brewery founder D. G. Yuengling, along with her sisters and their father, Richard Yuengling Jr. According to Jennifer Yuengling, due to the brewery’s successful relationship with Kuka over the years and the quality of the company’s robot technology, when it came time to upgrade the robots, Yuengling again opted for Kuka.
Six-axis robots depalletize/palletize at 400 kegs/hr
Each of Yuengling’s keg lines uses two Kuka articulated arm robots that are identical in size, reach, and payload. Within the lines, they perform depalletization and palletization. Empty kegs enter the line stacked on pallets—four half kegs (15.5-gal capacity) and eight quarter kegs (7.25-gal capacity) per pallet. The first robot removes empty kegs from the pallets and places them on a conveyor, where they travel to a cleaning process and are then refilled. Once the kegs are removed, the robot stacks the empty pallets in a holding station/table for the second robot to use. Both robots share the pallet station.
A Kuka KR 360 R2830 6-axis robot handles 15.5-gal kegs at speeds to 400/hr.
Speed and repeatability are the keys to the success of this cell, and all of its elements must be located precisely for each cycle. “The amount of work that the two Kuka robots do and the speed at which they operate is phenomenal,” says Friedman. “They can run 24/7/365, handling about 400 full kegs per hour.”
The updated robots at Yuengling’s Millcreek and Tampa facilities are Kuka KR 360 R2830 6-axis heavy-duty robots that provide the breweries with pose repeatability of 0.08 mm and an arm extension of up to 500 mm. Kuka also offers the robots in a version designed for applications that require resistance to heat, dust, and water, and with a range of mounting position options that allows for more adaptability.
Three million kegs handled with packaging robotics, just four repairs
Although the number one criterion for the keg line is safety, number two, according to Friedman, is reliable, continuous robot operation with minimal required maintenance. And if there is a needed repair, the fix is fast and easy to make.
“We’ve stayed with Kuka because we’ve always had extremely good support, both technical and training,” Friedman says. “The other main reason we choose Kuka robots is that they are very dependable, with a simple, practically maintenance-free design. Plus, we’ve improved our cycle times from about 250 kegs per hour to around 430.”
![]() | Read related article on White Castle’s robotic path to packaging automation. |
Friedman also noted that for six years prior to its replacement, one of the robots on the Tampa facility keg line handled both empty and full kegs. He calculates that it depalletized/palletized about 3 million kegs during its six-year working life—and over that time period, it needed only four repairs, which involved typical wear components.
“If we had been using a traditional palletizer, the number of breakdowns in that same amount of time would have been a hundredfold,” Friedman points out. “Our original palletizer was limited to 200 kegs per hour and no faster. It was a basic over/under palletizing setup and was an extremely hazardous system that required massive safety caging.”
![]() | Read Packaging World’s complete robotics report, “Robots 2023: Smarter, More Adaptable & More Robust.” |
Yuengling’s new robots all feature the compact KRC 5 controller, which Kuka says consumes less energy compared to its predecessor and slots seamlessly into existing IT and cloud environments. Kuka adds that due to its modular cabinet system, the KR C5’s hardware is durable and futureproof, and can be expanded as required. “The highly integrated, compact control modules are easy to operate, and Yuengling can link them to various software products and digital services as needed,” Kuka explains. The need for increased capacity was the main reason Yuengling added its Millcreek and Tampa facilities and incorporated Kuka automation. Since then, the company has increased production from 137,000 barrels to more than 2 million barrels, encompassing nine different beer types—a growth that Yuengling attributes in large part to the addition of robotic automation. PW