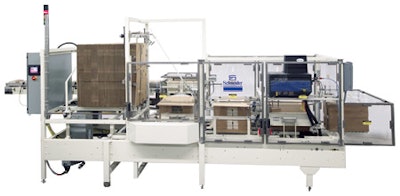
Case packer uses a power monitor to minimize energy consumption
A three-axis, side-load case packer receives up-to-the-minute information on energy use from a component mounted on the controls cabinet.
Jan 24, 2010
Machinery Basics
Annual Outlook Report: Workforce
Hiring remains a major challenge in packaging, with 78% struggling to fill unskilled roles and 84% lacking experienced workers. As automation grows, companies must rethink hiring and training. Download the full report for key insights.
Download Now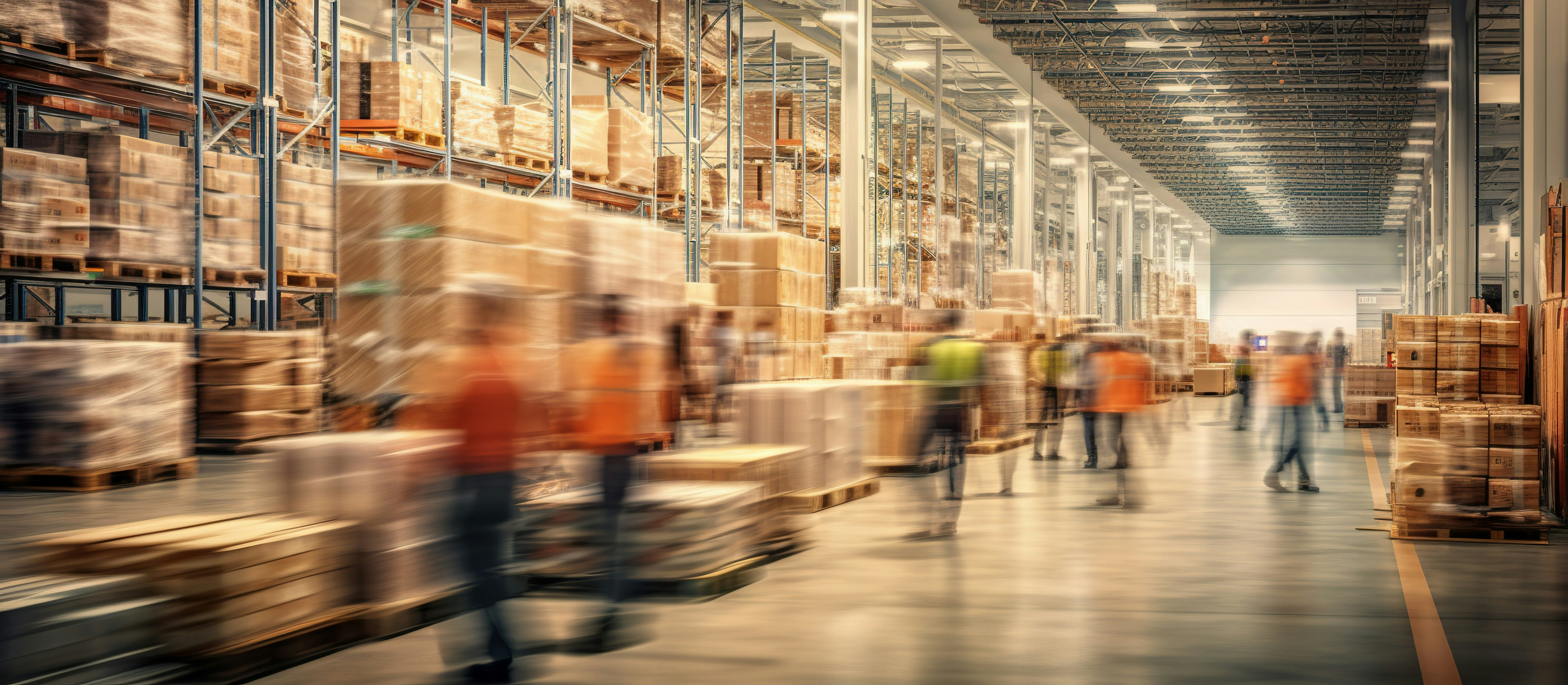
Conveying Innovations Report
Editors report on distinguishing characteristics that define each new product and collected video demonstrating the equipment or materials as displayed at the show. This topical report, winnowed from nearly 300 PACK EXPO collective booth visits, represents a categorized, organized account of individual items that were selected based on whether they were deemed to be both new, and truly innovative, based on decades of combined editorial experience in experiencing and evaluating PACK EXPO products.
Take me there