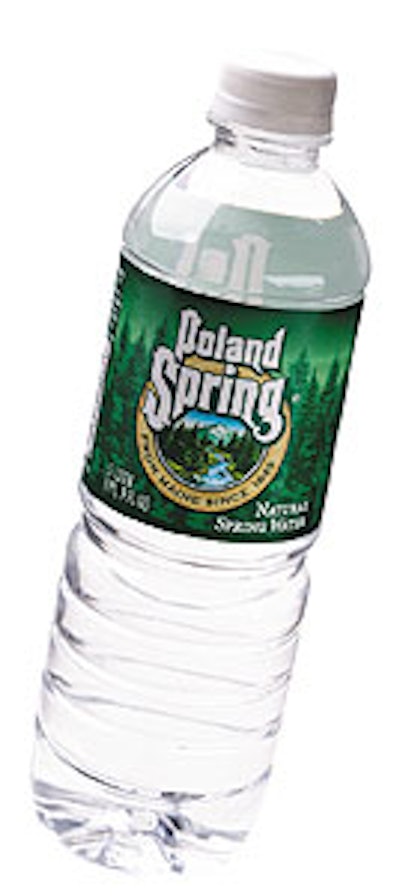
Traditionally, training’s been a ‘stand here, watch me, don’t touch that or I’ll break your fingers’ environment,” asserts Val Lovelace, training manager at Poland Spring Bottling Co. in Poland Spring, ME. But at Poland Spring, that negative training perspective simply doesn’t exist. Credit top management’s progressive long-term thinking for creating a corporate environment that values training for its role in increasing packaging equipment efficiency and developing and retaining skilled employees. “The training program at Poland Spring is a total team effort,” Lovelace points out. Hired in 1998 as the blow-mold supervisor at this bottled water company, Lovelace was later promoted to training manager and put in charge of training and development at the plant. Lovelace brought 20 years of U.S. Navy experience in electronics, maintenance, and curriculum development. She also worked as a production supervisor at a hot cereal plant for Nabisco in Minneapolis, where packaging was a key responsibility. Lovelace helped the Poland Spring plant initiate its on-the-job packaging training program (OJT) in 1999. Training at the plant extends beyond packaging, encompassing everything from leadership for top management to procedures for floor sweeping. In other words, it’s a “wall-to-wall” training approach, in which OJT plays a leading role.
A closer look at OJT Since Poland Spring initiated its OJT program, about 140 people have taken part. OJT is available to all hourly manufacturing personnel, which number around 320 employees. If an employee already has the skills necessary to perform his or her job, OJT is not necessary. An employee would go through OJT to learn how to operate a machine in which he or she had no previous experience. OJT is for blow-molding machine workers, those who operate and maintain packaging machinery, and forklift drivers. Lovelace is responsible for training and personnel development. Donna Hendry and Randy Browne assist her as technical trainers. Beneath them on the plant’s training hierarchy are 25 to 30 “certified trainers,” chosen from the plant “through a selection process that brings out the best and the brightest,” Lovelace says. OJT curriculum and testing is developed in-house by Poland Spring and Perrier Group of America. Lovelace explains that it is based on Robert F. Mager’s Criterion-Referenced Instruction (CRI) methods, which she learned during her 20 years in the Navy. Lovelace describes the methods in simple terms as “a structured, organized version of show-and-tell. We show you how to add a label roll to a labeler, for instance. Then we let you practice that until you’re comfortable doing it. When you’re ready to do it on your own, you must demonstrate that skill back to us. It’s a pass-fail test that shows if you can do it. When you do, we sign you off as having acquired that skill. There is no written test,” she notes. The curriculum is divided into safety, operations, quality training segments, and basic troubleshooting. From these four subjects, specific packaging training modules might last anywhere from a day to a month. Modules teach employees on equipment such as blow molders, fillers, box erectors, case packers, case sealers, multipackers, shrink wrappers, and palletizers. OJT is necessary for workers when they’re assigned to operate a machine that’s new to them. “An operator may end up having to run four or five different machines on a line,” Lovelace asserts. “So OJT would provide training for basic equipment operations, troubleshooting, and quality check procedures on each of the machines.”
Driven by market growth “The need for training was recognized here—back in the ’95-’96 timeframe,” says Lovelace. This plant went from running seven packaging lines to 10 pretty quickly, in an effort to participate in the fast-growing market for water in single-serve PET bottles.” She continues, “at that time, the company sales were growing at an annual rate of 40 to 50 percent, and it had made a huge capital investment in expanding this facility and in purchasing equipment for it. Two new packaging lines were installed in ’98, as were eight new blow-molding machines to produce bottles from preforms.” (For a look at the role of equipment vendors in training mechanics at Poland Spring, see story, p. 69). Unfamiliarity with that new equipment resulted in machine efficiencies of a mere 35% at the start, Lovelace estimates. Poland Spring, owned by the Perrier Group of America, knew it had to get its plant operators and mechanics up to speed on the new bottling and blow-molding machinery. Poland Spring management also was convinced that training its employees would deliver broader benefits, though they wouldn’t be as measurable as equipment efficiency numbers. These include company morale and retainment. Retainment of skilled employees isn’t so much a concern because of a small labor pool in a city as sparsely populated as Poland Spring, according to Lovelace. Instead, it’s a concern because skilled workers may be approached with job offers from other businesses.