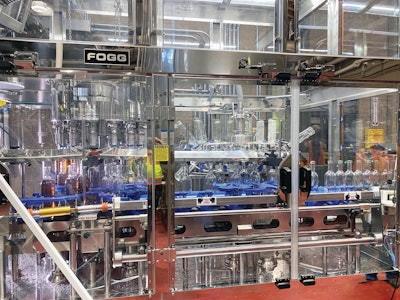
Manual filling and labeling was the method of operation until the 2019 commissioning of a Fogg Filler rinser/filler/capper. “We had a very small footprint in which we needed to fit our packaging line,” says High West founder David Perkins. “Fogg was able to incorporate the rinser, filler, and capper in one chassis, which made all the difference in the world. Three separate machines was not going to work.”
A pressure-sensitive labeler from P.E.Labeller applies either front-and-back or full-wrap labels.
The Arol capper—actually a corker—notes Perkins, is also new to the semi-automated line. So are the following:
• a P.E.Labeller pressure-sensitive labeler from that applies either front-and-back or full-wrap labels
• a 3M case taper
• a tamper seal applicator from ColloPack
• a Videojet date coder that prints lot and date code information on each bottle label
•a Weber print-and-apply thermal-transfer case labeler
“In our manual bottling mode, we needed a crew of about 28 people,” says Perkins. “Now it’s more like three—one to take empty bottles from their reshippers and place them on the conveyor leading into the rinser, one to put filled, capped, and labeled bottles back into the reshippers, and one to palletize the reshippers.”
In addition to greatly reducing the amount of hand labor required to get bottles out the door, the 14-station rotary filler runs at a steady 35 bottles/min when 750-mL bottles are in production. Previously the top speed on that size was 27/min. And, says Perkins, a 375-mL bottle is also in the mix, and when that bottle is being filled the output is more like 50/min.
Two bottle styles are filled at High West, and both come from Pavisa. A style called “rustic flint” represents the majority of the bottles the firm fills, but also in the mix is an apothecary bottle that’s amber colored.
Regardless of which bottle is being filled, the process begins with bottles being removed by hand from corrugated reshippers and placed on an infeed conveyor. The first stop is the rinser, which consists of 14 stations on a rotary turret. Each bottle is gripped and inverted so that a rinsing medium can be gently sprayed inside to remove corrugated dust and other impurities. Worth noting is that the rinsing medium, while largely water, also contains a certain percentage of whatever whisky is being filled. If it were pure water it might alter the percentage of alcohol by volume.
Gravity-feed filler
By the end of the rinsing process, each bottle is returned to its upright orientation. A starwheel and feedscrew combination now transfers the bottles to the gravity-feed filler, which also has 14 stations. Each filling valve is polymer-tipped so that should the valve make contact with the glass as it enters, the chance of glass being chipped is eliminated.
High West Distillery focused on the operations side of the business. Go here to see how another spirits brand designed a presentation box with double-door design that opens to a stunning, gold foil menagerie fit for a queen.
Filled bottles move through another feed screw exchange to enter the single-head pick-and-place corker. Corks move from a floor-level hopper up to an overhead position and then are fed down a chute to a reciprocating device that picks one cork at a time and presents it to an insertion device that lifts the cork out. As the reciprocating device strokes back to get another cork, a freshly filled bottle arrives beneath the insertion device, which strokes down to put cork into bottle. The filled bottles then are conveyed out of the Fogg system.After cases are taped shut, a print-and-apply labeler brings the line to a close.
Two last observations on the Fogg system. First, the whole rinse/fill/cap block is fully enclosed by a roof of sorts. This is to keep plant dust from making its way back into a bottle after it’s been rinsed. Second, a very efficient “de-dusting” system is in place. Cork is notorious for generating dust, so vacuum hoses attached to the enclosed block do a good job of removing cork dust that might otherwise make its way into a bottle or might even cause machine downtime if given enough time to build up.
Once out of the Fogg system, bottles are conveyed through the pressure-sensitive P.E. Labellers machine. Next is a unit from Collopack that applies a tamper-evident seal around the neck. Then bottles are manually placed back into their corrugated reshippers. The 3M case taper and Weber print-and-apply labeler bring the line to a close.
“What we were doing in the past just wasn’t sustainable,” says Perkins. “Now we have equipment we can leverage for the foreseeable future—and it fits our space. Fogg was very good at setting us up for success. They’ve given us all the information and guidance we need for optimizing preventive maintenance. And they’ve been great about helping us with anything we can’t work through. The attention to detail they apply to their equipment and customers matches what we apply to what we do here at High West.”