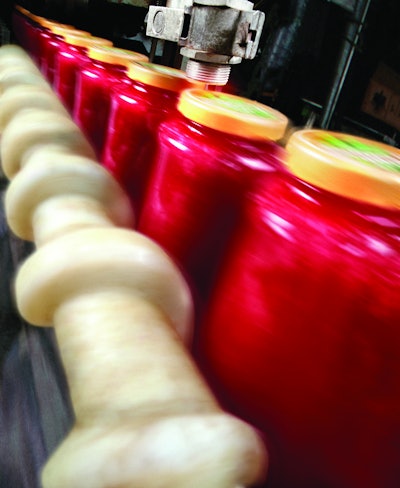
Show Daily Exclusive - Metal shards are the last things you want to encounter when biting into a burger or sipping a cold glass of milk. Unfortunately, foreign object contamination is not uncommon. Between 2012 and 2015, the USDA Food Safety and Inspection Service recalled more than 2 million pounds of food for containing “extraneous material.”1
METAL CONTAMINATION
While food recalls due to disease-causing contaminants often receive maximum media coverage, foreign object contaminations can be just as damaging—and disturbing. Due to the mass industrialization of our food manufacturing, processing, conveying and packaging systems, objects such as glass, metal chips, plastic, bone, wood or small rocks can sometimes find their way into food products. With more and more automation and higher line speeds, extraneous material slips through the cracks (sometimes literally).
Equipment is frequently the culprit behind such mishaps. Food processing, conveying and packaging involve a lot of moving parts—scrapers, paddles, pistons, valves, spools, grippers, sliding bearings, plates and screws. Metal parts sliding against each other for prolonged periods cause friction and wear. Breakage and wear of metal-on-metal equipment generates metal particulate, flakes and dust that ultimately ends up on or mixed into the food product. Aggressive chemicals used in clean/sterilize-in-place procedures can corrode metal, causing it to become brittle and more prone to flaking.
Lubricants, often required to ensure that metal parts move seamlessly, are another potential contaminant. With stricter regulations on water consumption for processing and lubrication, due to environmental concerns (coupled with an ongoing focus on hygiene and contamination), selecting, applying and disposing of food manufacturing lubricants is a growing liability.
Beside the obvious (consumers becoming ill or injured), foreign object and extraneous material contaminations are bad for business. According to the FDA2 and major news sources, Kraft Foods’ recent voluntary recall of 6.5 million boxes of Mac & Cheese cost the company $6–$10.8 million dollars in lost retail revenue alone.3 Media coverage of the recall caused a drop in company stock price and an overall loss of customer confidence. What parent is going to buy a box of Mac & Cheese after seeing a news report about the potential of metal pieces inside?
More recently, ConAgra Foods expanded a voluntary recall of P.F. Chang’s Home Menu brand products due to the potential presence of small metal fragments (2–9mm) in the sugar used in the sauce.4 According to ConAgra’s press release, “Foodborne foreign objects that are not hard and sharp and less than or equal to 7mm in length may cause minor injuries such as temporary reflexive choking and irritation of the gastrointestinal system.” The expanded recall totals more than 195,000 lb. of chicken and beef.5 The negative press alone for such a mishap could put a smaller company out of business.
ENHANCING SAFETY
In 2011 the Food Safety Modernization Act updated Good Manufacturing Practices in regard to manufacturing, processing, packaging and holding of human foods, shifting the focus from responding to contamination to preventing it.
Foreign materials are a concern not only in terms of customer complaints and financial damages, but also as factors impacting the effectiveness of the company’s overall food safety program. Good food plant personal hygiene policies, practices and standard sanitation operating procedures can provide an excellent foundation for eliminating foreign objects. Separation and detection strategies, including sieving, screening, filtration, float tanks and magnetic separation, can identify and remove contaminants from product streams.
Many companies have redesigned lines to minimize the number of metal-to-metal moving parts. These changes have created a growing demand for polymeric replacements for metal parts and metal-detectable plastics. Another tactic is the use of metal or x-ray detectors to check raw materials or packaged, ready-to-ship products. Measuring density, x-ray machines (when coupled with computer analysis) can find dense, sharp-edged contaminants including glass, stone, bone and plastic.6
ENGINEERING THERMOPLASTICS
Advanced engineering plastics from Quadrant Engineering Plastic Products (Quadrant EPP) (Booth E-9437) not only reduce the risk of foreign object contamination, but also improve productivity. Plastic-on-plastic components (or even plastic-on-metal components) outlast metal-on-metal with less debris, noise, wear and lubrication while consuming less energy.
With a complete line of metal and x-ray-detectable polymers,7 Quadrant EPP offers manufacturers the comfort of knowing that even if plastic debris finds its way into the product, it will be caught by standard detection equipment (material additives allow detection of particles as small as 27 cubic mm).
Quadrant EPP’s FDA- and EU-compliant8 self-lubricating polymers replace metal wear components in the most aggressive applications, including environments exposed to high temperatures and aggressive cleaning chemicals.9 These advanced plastics offer high strength-to-weight ratios and are designed to run against mating components without lubrication, often significantly increasing component life. Self-lubricating polymers also help food manufacturers adhere to regulations regarding lubricant contamination of washdown runoff.
Quadrant EPP’s polymer materials offer improved impact resistance resulting in less breakage of parts and increasing the mean time between repair. With 25% of production costs related to maintenance, that’s no small savings.
When considering the risks of metal contamination, it makes sense to consider advanced engineering plastic parts. Quadrant EPP supplies stock shape materials globally as well as finished parts for food processing, packaging and conveying with a portfolio that includes TIVAR® HPV ultra-high-molecular-weight polyethylene (UHMW-PE) plus internal lubricant, TIVAR MD UHMW-PE, ACETRON® MD POM-C polyoxymethylene-based material and KETRON® MD polyether ether ketone.
The right plastic alternative could save millions in recall costs and a lot of bad press.
For more information, visit www.quadrantplastics.com. SD
1www.fsis.usda.gov/wps/portal/fsis/topics/recalls-and-public-health-alerts/recall-summaries
2 www.fda.gov/Safety/Recalls/ucm438700.htm
3www.cbsnews.com/news/kraft-macaroni-cheese-recalled-due-to-metal-fragments/
4www.conagrafoods.com/news-room/news-ConAgra-Foods-Expands-Recall-of-PF-Chang%E2%80%99s-Home-Menu-Brand-Meals-Available-in-Grocery-Retailers-Due-to-Potential-Presence-of-Foreign-Material-2185959
5www.foodsafetynews.com/2016/07/conagra-expands-recall-of-chicken-and-beef-over-metal-fragments/#.V6DCV442tjU
6www.foodsafetymagazine.com/magazine-archive1/augustseptember-2009/food-safety-insider-testing-solutions/x-ray-contaminant-detection/
7http://media.quadrantplastics.com/fileadmin/quadrant/documents/QEPP/EU/Brochures_PDF/Food/Food_MD_Products_Br_E_0311.pdf
8 https://en.wikipedia.org/wiki/Food_contact_materials
9www.quadrantplastics.com/na-en/support/chemical-resistance-information.html