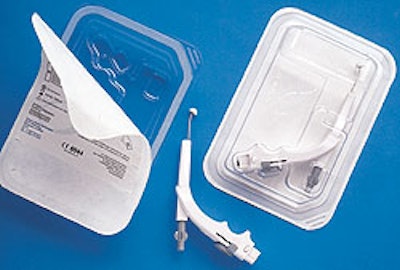
After all the time it takes to get a new product cleared by the Food & Drug Administration, medical device manufacturers are eager to bring those new products to the market. So eager that the primary package selected is often far from the most efficient. But as Somnus Medical Technologies proved recently, packaging efficiency can come after product launch.
The product in this case was a small device that connects to an electrical control unit that generates radio frequency power. The device is used in Somnoplasty, a minimally invasive procedure performed in a physician’s office that reduces excess tissue in the nose, mouth, and throat as a treatment to prevent snoring or sleep apnea.
Shortly after the device received FDA clearance in mid-’98, the sterile device was packaged in a protective pouch sandwiched between two pieces of polyurethane foam, all inside a corrugated box. “As is typical in this industry, the research and development folks were more concerned with the product itself than with manufacturing or packaging,” recalls Kevin Brand, manufacturing engineer at Sunnyvale, CA-based Somnus.
While the packaging worked well, last year the company decided to look for more efficient ways to manufacture the product, and the packaging was improved as well. A team of experts from the firm’s manufacturing, R&D, and quality departments first decided to separate from the package a reusable cable that connects the sterile handpiece to the radio-frequency generator.
With only the handpiece to package independently, the team selected the concept of a thermoformed tray, designed and manufactured by Merrill’s Packaging (Burlingame, CA). It’s made from 30-mil Pentamed® MD 8G1/15 from Klöckner Pentaplast of America (Gordonsville, VA). This blue-tinted sheet of glycol-modified polyethylene terephthalate (PETG) is thermoformed to fit the device and then sealed with Tyvek® lidstock from Du Pont (Wilmington, DE) that’s supplied by Tolas Health Care Packaging (Feasterville, PA). Manufacturing engineer Brand was familiar with thermoformed trays from his experience at other medical device manufacturers.
The new package reduced the volume of packaging materials by 71% and cut packaging material costs by 57%. Also, the more compact package permitted Somnus to develop a five-piece dispenser pack, Brand reports.
Europe drives recyclability
Brand was a strong proponent of the thermoformed tray. “There were several reasons we selected this package,” he says. “First, it reduces packaging volume, and it’s recyclable. Since we also sell into Europe, we anticipated the need to use a material that’s readily recyclable. So the marketplace in Europe really drove the material selection.
“Plus, the transparent tray provides better visibility of the product. The plastic material itself is so clear and beautiful that it gives the product a perceived higher value. And the smaller tray makes it easy to ship in five-packs, which of course boosts sales.”
While originally designed to hold the Somnoplasty device that’s used to shrink excess tissue in the patient’s soft palate, the tray can also be used to package another device that’s used to shrink tissue at the base of a patient’s tongue. A third product, for turbinates in the nose, is much smaller and can be easily packaged in a pouch. All three of the devices may be needed for patients suffering from sleep apnea, a serious condition that can close the breathing passage.
The turbinate device will likely be shifted to a tray package in the future. “It’s always desirable to have the smallest number of suppliers possible to minimize the hassle and expense of inventory and parts management,” says Brand.
A design challenge
More than 40% of Merrill’s sales volume is in packaging of medical devices, a specialty market it has served for more than 20 years.
“This package was quite a challenge,” says Brian Meltzner, sales manager at Merrill’s. “Somnus’s device has a unique shape with lots of curves to fit the doctor’s hand and inside a patient’s mouth. Plus, the handpiece has a movable part that has to be secured. So we needed to design a part with rounded corners and straight walls to hold the product and that moving part to avoid movement and damage during shipment. But then we also needed large draft angles to ensure easy and uniform manufacturability.”
For Somnus’s part, Brand developed tight specifications, indicative of a company that boasts ISO 9001 certification. “We told them we wanted a minimum wall thickness to provide protection with large draft angles to avoid thinning out the material during forming that could lead to brittleness or even create pinholes,” he says. “We also specified a three-eighths-inch-wide flange to ensure secure seals of the lidding. And we specified the transparent blue-tinted virgin material to enhance the appearance of the package and the product.”
Somnus provided Merrill’s with CAD/CAM files of the devices to be input into its computer system. The supplier then created a multiple-piece tool, or what Brand calls a modular tool of several pieces, so that certain parts could be changed without making a completely new tool. “They provided us with a prototype tray quickly, and we tested it. Once it was finalized, Merrill’s provided fast turnaround on production,” Brand says.
Material of choice
Because the device would be sterilized by gamma rays, the company felt that polyester was the material of choice. Merrill’s recommended the Pentamed that’s coated one side with silicone for easy denesting of empty thermoforms and for better mold release.
“One-side coating with silicone is becoming common for medical device packagers,” says Merrill’s Meltzner. “If silicone was on the flange, it could create adhesion problems with heat sealing of the lidding. That could compromise sterility, probably the greatest concern to device makers.”
Klöckner Pentaplast is the exclusive supplier of PETG sheet and film to Merrill’s. “Their materials have a uniform thickness and a uniform coating application so they work well with our molds. The consistency and quality of their material is unsurpassed, and they also provide excellent customer support,” says Meltzner.
The thermoformer suggested the 30-mil thickness because its rigidity would provide ample product protection after forming. In its operation, Merrill’s uses vacuum, pressure, and a mechanical plug assist to create the Somnus tray. After forming, the material is allowed to cool, and it shrinks a bit. Then the company’s proprietary die-cutting technology is used to separate individual trays from the web of material.
“It’s our design requirement that the tray edges be exceptionally smooth,” says Brand. “For a medical product, rough or sharp edges could potentially violate sterility with gloves and such.” Finished tray edges cannot have any “angel hair” or other particulate matter that could cause contamination.
Filling and sealing
At Somnus, workers load the trays with devices and place them two-up into cavities of the Model 14P impulse heat-sealing machine from EMD Products (Libertyville, IL). The lidding is placed on top of each tray, and the sliding drawer is pneumatically driven into the sealer, where heat is applied to seal the lidding to the flange of the tray.
Once the cycle is completed, the trays are removed and visually inspected for seal integrity. The sealed trays are moved to another worker, who applies pressure-sensitive labels to the lidding. These labels are color laser printed on-site with lot number, expiration date, product identification in eight languages, and graphics. Workers then load five of the completed trays into the corrugated five-pack dispenser box, to which another p-s label is affixed. Later, the boxes are sent to be sterilized.
When asked about the labeling of the lidstock, Brand explained that supplier Tolas prints the Somnus logo onto the Tyvek but that the company elected to use a label for the variable information like lot number and dating. “Because of the variable data and the opportunity to change graphics, we opted to print our own labels,” says Brand. “We didn’t want a separate operation for the variable information. We decided to do all the printing at one time, right at the point of packaging.”
While changing label “graphics” on a medical package might seem unusual, Brand indicated that it’s really a function of adding and adopting more international symbols to the labels. “Our labels already display some international symbols to help facilitate communications overseas. For example, we use the numeral two with a line through it to designate no reuse of the device. We also use an hourglass symbol with the expiration date. There are several international symbols that can really aid in communications.”
Before Somnus could market the devices, it had to complete a package validation process for the sterile barrier and shelf life. Package samples were subjected to a battery of tests simulating worst-case scenarios of international shipping conditions. Seals were tested in three ways: visually, dye penetration, and burst tests. In addition, shelf life testing was performed, and Somnus now marks its products for a shelf life of two years.
The new package passed all tests, Brand says, with flying colors.
“We’re very satisfied with the new package. Because the sterile barrier is such a critical factor, the fact that we’ve had no problems with any breach is the most important test of its success,” Brand says with pride. “In addition, we’ve reduced waste a great deal.” (AO)