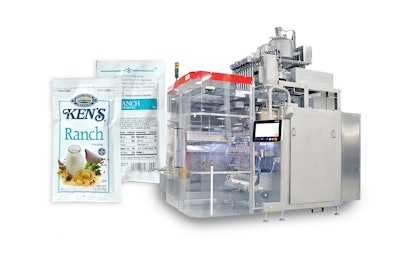
Among the more prominent names in salad dressings, sauces, and marinades, Ken’s Foods is a family-owned and operated manufacturer that has gone mainstream. With facilities in Massachusetts, Georgia, Nevada, and Indiana, the company’s two main divisions, Retail Grocery Products and Food Service, combine to produce and package more than 400 varieties of dressings, sauces, marinades, and condiments.
Thanks to an existing relationship with Ken’s Foods, processing and packaging machinery manufacturer IMA Dairy & Food USA was familiar with the equipment Ken’s was using in its daily operations when it approached the sauce and condiment producer about maximizing the performance of some of its equipment in the foodservice packaging division.
A focal point of the discussion was Ken’s sachet packages, which are used for a diverse range of condiments and dressings in food service environments. The sachets are produced in a range of sizes, including a 1.5-in. pouch, a narrow pouch, and a 3-in. wide pouch in an array of flexible packaging substrates. Used for numerous sauces and condiments of differing viscosities, the sachets require varying fill volumes based on product type and pouch size.
Proposed equipment upgrade
IMA recommended a Hassia F600 vf/f/s, which it said could optimize Ken’s production parameters, including better front and back print registration, streamlined changeover, and a substantial uptick in fill accuracy and throughput.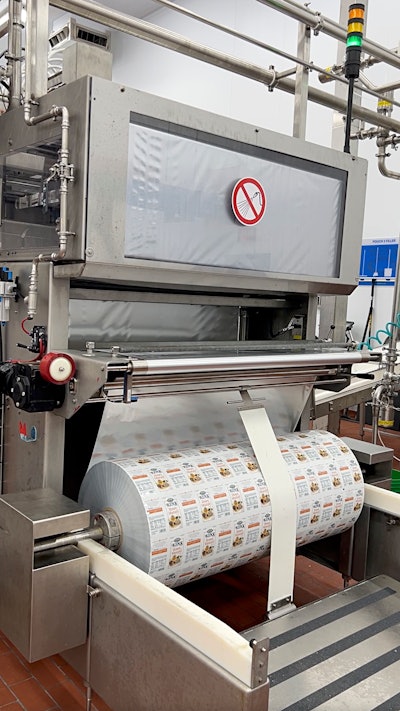
“At Ken’s, we value candid discussion,” says Jeff Murzycki, Vice President of Engineering, Ken’s Food. “The IMA sales team and the Hassia engineering team were proactive and incredibly transparent with charts, drawings, and pre-test results that supported their recommendations and responses throughout our communications. This showcased to us how well they really know their market.”
Ken’s requested a demonstration of IMA’s suggested equipment configuration. The result was reassuring enough that Ken’s purchased not just one Hassia F600, but five machines for installation across three of its facilities in Nevada, Georgia, and Indiana, all without so much as a trial period.
“As with any new equipment installation, there were some early challenges in the installation/validation process,” Murzycki says. “But the IMA team provided honest and open communication, quick resolution, and solid collaboration with our in-house team - exactly the type of response that we look for in a partner.”
Designed for single-roll sachet production, the Hassia F600 produces four-sided sealed sachets at a pace of up to 80 cycles/min on as many as 16 lanes. The unit runs a single wide roll located at floor level for easy changeover and front-and-back sachet registration, an option offering more printing choices than traditional two-roll machines. The F600 can handle rolls as wide as 1.2 m with a diameter of 800 mm and can yield up to 16 hours of run time between roll changes. This significantly reduced downtime and boosted productivity.
Ken’s also saw value in the F600’s flexibility. A range of package designs is possible, and sizes can be configured to align with production capacity. The machine’s control concepts are highly versatile and include opportunities for integration with customer-specific systems. The unit can handle all common packaging materials suitable for heat-sealing.
Results
In short order, the benefits of the new machines were evident. For one, Ken’s immediately realized improved dosing and filling accuracy. With the F600’s more exacting fill tolerance, Ken’s now has the ability to right-size its sachets, meaning there isn’t a need for excess material typically allotted for spillage. This reduced the amount of wasted product and film. Given the volume of throughput, it’s easy to imagine how much material Ken’s is saving per year. This is both an eco-benefit and a materials/product cost benefit; a penny saved is a penny earned, and limiting materials usage improves the company’s sustainability profile.Likewise, the tighter fill tolerances have also led to significantly higher throughput and increased yields for Ken’s. By installing an F600 Ken’s saw an immediate 25% gain in throughput capability. With the additional flexibility the F600 provides, the company is experiencing production gains of as much as 400-percent.
The successful implementation of IMA's Hassia F600 not only addressed Ken's immediate packaging needs, but also opened avenues for sustainability and improved messaging opportunities.The sachets are produced in a range of sizes, including a 1.5-in. pouch, a narrow pouch, and a 3-in. wide pouch in an array of flexible packaging substrates.
From a marketing standpoint, the F600 has offered significant benefits with its precise front-to-back alignment and double-sided registration. This feature gives the company the opportunity to print on both the front and back of its sachets, allowing for more comprehensive brand messaging opportunities befitting a brand of Ken’s stature. The additional, printable surface area gives the marketing team a blank canvas and overall, results in more compelling packaging.
With an advanced clean-in-place function, the equipment allows for shortened changeover times. This feature is especially valuable for a company that manufactures hundreds of different products, as Ken’s does. Not only does it provide time savings for cleaning processes, but it also reduces the amount of per-wash water and cleaning agents used, further decreasing the company’s environmental footprint.
“The Hassia equipment was robustly designed, and has been serviced well,” says Murzycki. “We have had great overall results thus far, combined with quick communication and swift responses for our service needs.” PW