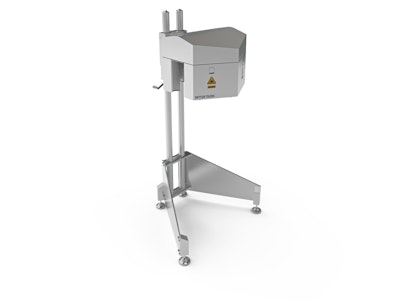
This is a critical process, since the FDA reports that more than half of packaged product recalls are due to incorrect or unreadable labels and codes.
Using six evenly distributed viewpoints and liquid lens focusing technology, the V15 conducts 360° inspections of containers to ensure both label ingredient information (such as potential allergens) and inkjet-printed codes are clearly readable. The liquid lenses adjust automatically to the distance from the target, enabling the system to inspect containers of different sizes without physically moving the cameras. Optional cameras can be added to the system to inspect the tops and bottoms of containers, where additional codes are often placed. The entire system is housed in a stainless steel cabinet, keeping it secure even in harsh washdown environments.
For many manufacturers, space on the production line is at a premium, and it can be difficult to add vision inspection equipment into the production process. The V15 system fits over the manufacturer’s conveyor rather than breaking into it, making installation on a line, and movement from line to line where required, convenient and space-neutral.
The V15 runs on Inspection Manager software. The software can be programmed to allow access to only qualified personnel, simplifying operations and limiting the opportunity for human error. Setup of inspections is easily programmed in the system to check for code variations that a product may incur. Changeovers to new product targets for inspection are also made quickly and efficiently.