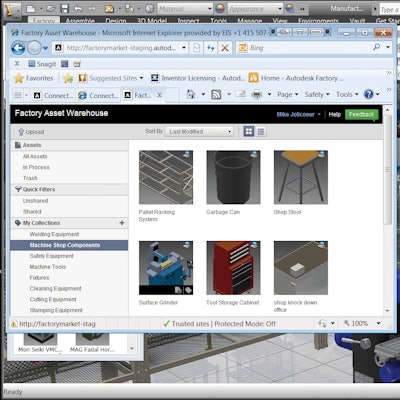
As a manufacturer of filling machines used in the food, chemical and petrochemical industries, neither Feige Filling nor its customers, have what is commonly considered to be a complex manufacturing process (such as automotive or aerospace). As a result, many would not think of Feige (based in Bad Oldesloe, Germany) and its customers as the type of companies to leverage digital manufacturing technologies to optimize production operations. But after nearly a decade of work with 3D CAD systems, Feige recently expanded its use of modeling software to go beyond designing parts and begin designing optimized production processes for its customers.
A typical customer for Feige has a factory that includes not just filling equipment, but also storage areas, conveyor systems, stacking technologies and cleaning systems, which must all work together.
Feige had been using Autodesk Inventor, AutoCAD Mechanical and Autodesk Vault collaboration software (from Autodesk, www.autodesk.com, San Rafael, Calif.) for several years to design the filling equipment it produces. In 2011, the company added Factory Design Suite to create 3D digital factory layouts that incorporate digital models of the various machines and factory components used in its customers’ production processes.
“This makes it easy to digitally explore different layout scenarios to find the optimal layout solution,” says Jörg Duus, head of design engineering at Feige Filling.
The company uses factory-specific visualization tools to provide potential clients with 3D layout proposals, rather than multilayered 2D drawings that can be difficult to interpret.
“The suite helps us to convince our customers of our professional competence,” says Duus. “To see the whole plant in 3D in the workshop is a great experience for them. Material flow analysis, TimeLiner schedule simulation and collision checks are tools with direct customer benefits. We can generate them directly out of the suite with the same database used for the plant layout. This means we have a continuous database for all steps in planning and realization of filling plants.”
Reasons for limited uptake
With the benefits of digital manufacturing becoming clear even to those companies outside of the complex manufacturing arena, it begs the question: Why isn’t digital manufacturing more widely used and fulfilling its promise to streamline manufacturing production operations across industry?
Tony Christian, director at Cambashi (www.cambashi.com), a Cambridge, U.K.-based research and analysis firm that focuses on the business benefits of IT) contends that digital manufacturing has not experienced a wide uptake yet because manufacturers are only now really getting up-to-speed with the integration of manufacturing execution systems (MES) and enterprise resource planning (ERP) systems.
“We are a long way from full deployment of digital manufacturing solutions even in the most advanced industries,” says Christian. “Progress towards integration of the facility design aspects of digital manufacturing and the operational aspects is patchy.”
Christian says that the adoption of digital manufacturing technologies is, currently, a very dynamic situation. The reason for this is because “plant floor machinery is going through a dramatic transition with control changing from custom electronics and unique communications methods to industry standard computers and networks monitoring controllers with embedded software linking to many more actuators and sensors.
“In the past 10 years we have gone from having a monthly production planning bucket defined by the enterprise planning system to now having every batch, if not every item, tracked between the shop floor and the enterprise systems,” says Christian.
As investment by both vendors and users drives the integration of ERP, PLM (product lifecycle management) and MES, the benefits of digital manufacturing will grow on a wider basis, Christian contends. When this happens, industry will be ready to achieve the full integration between data for facility design and production operations to complete the digital manufacturing picture.
Beyond the technology integration issues, another reason often cited for slowness in the application of digital technology tools is simply a lack of familiarity with the technology and concern over the usability of existing digital assets with the new tools.
“Users may have concerns about leveraging these digital manufacturing tools when they have already invested a great deal of time with another particular toolset,” says Ryan McMahon, Factory Design Suite senior program manager at Autodesk (San Rafael, Calif.). “Moving away from familiar tools is difficult even when there is a compelling return on investment associated with the new tool. Companies that have libraries of digital assets often object to new tools being introduced due to a lack of confidence in the new tools and the available translation capabilities.”
Where digital makes sense
Given the expected reservations about any new technology, but weighing that against the clear benefits digital manufacturing has been shown to have, the answer as to whether or not digital manufacturing can fulfill its promise on a broader scale lies in the technology taking further root in the most suitable applications for it.
Though examples like Feige Filling spotlight the realistic potential for digital manufacturing technology at companies outside of the complex manufacturing arena, most industry observers still agree that digital manufacturing makes the most sense in capital-intensive industries like aerospace, automotive, high-tech, industrial machinery, and medical systems.
“Even though many of the digital manufacturing benefits could be achieved in both discrete manufacturing and process manufacturing industries, digital manufacturing makes more sense in the complex manufacturing environment in discrete industries,” says Ganesh Hegde, senior director, global manufacturing solutions, at SAP (www.sap.com, Walldorf, Germany). “Generally, digital manufacturing applies less in high-volume, simple-to-build product areas and fabricated product lines.”
Tom Hoffman, director of manufacturing engineering software for Siemens PLM (www.plm.automation.siemens.com, Plano, Texas) points to applications involving high levels of automation and complexity involving both humans and equipment as being ideal for digital manufacturing technology. These applications often involve instances where robotic simulation, virtual commissioning and Lean manufacturing principles are applied to achieve optimal system configuration and eliminate potential issues before production begins.