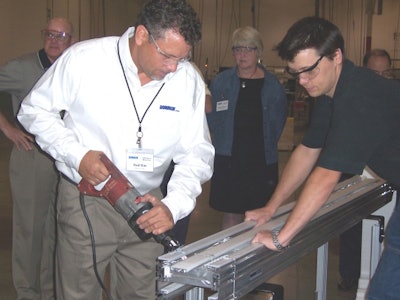
At the late-August Dorner media event, Dorner personnel demonstrated how the Dorner 5200 conveyor could be shortened as necessar
Here are a few insights, as observed during an August 2007 media tour of the company’s cell manufacturing process at its Hartland, WI, plant.
Dorner Manufacturing Corp. (www.dorner.com) believes these strategies helped at the 100,000-sq-ft Hartland plant. The company says the plant shipped 24,200 orders last year, achieving 98.5% on-time delivery. That’s up from a less than 90% before 2000.
One Dorner representative told touring editors that manufacturing changes made in the plant since 2000 have resulted in producing more output on one shift than was done on two shifts—and with nearly 40 fewer people.
Interestingly, the lean manufacturing concepts employed by Dorner doesn’t necessarily require the latest electronic bells and whistles. Employees rely on color-coordinated signs and cards to help make and ship conveyors and related equipment to awaiting customers on a just-in-time basis. An orange, green, pink, or yellow card signals that the order needs a part or component from another cell within the plant.
The signs and cards are central to the Kanban concept, where "kan" means visual, and "ban" means card or board, notes online encyclopedia Wikipedia (http://en.wikipedia.org/wiki/Kanban).
The August 24 plant tour was part of a Dorner Industrial Conveyor Line Media Tour highlighting the introduction of the company’s new 5200 Series modular plastic belt conveyor platform targeted for use in industrial, automation, and packaging applications.
- In the cell manufacturing concept, workers are rotated to different job functions within the cell during the day. This staves off potential boredom and helps increase their knowledge, making them more valuable to the company.
- Many of today’s students are going to college “to learn to become vice presidents,” not to learn manufacturing skills. With that in mind, the need to train new employees is more important than ever. Job-floor apprenticeships could again become a valuable way to help employees develop these skills, therefore becoming more valuable to the company and to the industry they work in.
- Since skilled workers are in demand, current employees are rewarded financially for recruiting qualified hires. Although husband-and-wife teams aren’t encouraged, these hires could be relatives or friends of current employees.
- There is no substitute for helping employees achieve a genuine feeling of ownership. The more employees contribute to, and are rewarded for the company’s success, the more valuable they become.
- A product (a conveyor in this instance) is not built until all of its parts are ready in the cell. That’s opposed to having, say, 32 conveyors partially assembled at once, with all of them missing parts.
- The system helps workers quickly move materials through the plant to complete and ship orders.
Dorner Manufacturing Corp. (www.dorner.com) believes these strategies helped at the 100,000-sq-ft Hartland plant. The company says the plant shipped 24,200 orders last year, achieving 98.5% on-time delivery. That’s up from a less than 90% before 2000.
One Dorner representative told touring editors that manufacturing changes made in the plant since 2000 have resulted in producing more output on one shift than was done on two shifts—and with nearly 40 fewer people.
Interestingly, the lean manufacturing concepts employed by Dorner doesn’t necessarily require the latest electronic bells and whistles. Employees rely on color-coordinated signs and cards to help make and ship conveyors and related equipment to awaiting customers on a just-in-time basis. An orange, green, pink, or yellow card signals that the order needs a part or component from another cell within the plant.
The signs and cards are central to the Kanban concept, where "kan" means visual, and "ban" means card or board, notes online encyclopedia Wikipedia (http://en.wikipedia.org/wiki/Kanban).
The August 24 plant tour was part of a Dorner Industrial Conveyor Line Media Tour highlighting the introduction of the company’s new 5200 Series modular plastic belt conveyor platform targeted for use in industrial, automation, and packaging applications.
Companies in this article
Videos from Dorner