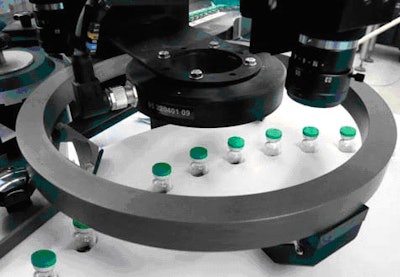
This content was written and submitted by the supplier. It has only been modified to comply with this publication’s space and style.
The transition period for implementing the new Annex 1 regulations regarding the provisions for capping of freeze-dried vials will end by March 1st, 2010. Point 121 says:
121. Vials with missing or displaced stoppers should be rejected prior to capping. Where human intervention is required at the capping station, appropriate technology should be used to prevent direct contact with the vials and to minimise microbial contamination.
With regard to Annex 1, Seidenader Vision, one of the leading suppliers of optical inspection systems for the pharmaceutical industry, have launched a variety of solutions for the automatic inspection of caps and closures. They all comply with the new requirements and are adaptable to the individual needs of the customers:
- high-stopper detection
- crimp-cap inspection
- high-stopper detection and crimp-cap inspection combined in one machine
- all solutions for isolators or clean-rooms
- gas-proof design (e.g. H2O2 resistant)
- customized solutions with one or more cameras
The cost effective and reliable systems can be integrated onto new capping machines as well as existing lines. Besides, Seidenader offer the mechanical platform for a separate machine that accommodates camera station, product handling and reject system on a very compact footprint. The solutions use either the reject integrated in the existing machine of the customer or the system developed by Seidenader, and fulfill the requirements of the Annex 1 not to have direct contact with the product.
The camera modules are integrated before the final application of the aluminum cap, to check the proper seating of the stoppers. A second station has been developed to verify the correct crimping and seal.
The technology has been well-proven in numerous cosmetic defect inspection stations that Seidenader have installed with great success on a worldwide basis.
The advantages of the Seidenader solutions are:
- no discussions with authorities regarding compliance with Annex 1, point 121
- same camera module for capping or inspection machines
- experience of over hundred integrated stations in operation
- documentation and testing available as to FDA expected levels
121. Vials with missing or displaced stoppers should be rejected prior to capping. Where human intervention is required at the capping station, appropriate technology should be used to prevent direct contact with the vials and to minimise microbial contamination.
With regard to Annex 1, Seidenader Vision, one of the leading suppliers of optical inspection systems for the pharmaceutical industry, have launched a variety of solutions for the automatic inspection of caps and closures. They all comply with the new requirements and are adaptable to the individual needs of the customers:
- high-stopper detection
- crimp-cap inspection
- high-stopper detection and crimp-cap inspection combined in one machine
- all solutions for isolators or clean-rooms
- gas-proof design (e.g. H2O2 resistant)
- customized solutions with one or more cameras
The cost effective and reliable systems can be integrated onto new capping machines as well as existing lines. Besides, Seidenader offer the mechanical platform for a separate machine that accommodates camera station, product handling and reject system on a very compact footprint. The solutions use either the reject integrated in the existing machine of the customer or the system developed by Seidenader, and fulfill the requirements of the Annex 1 not to have direct contact with the product.
The camera modules are integrated before the final application of the aluminum cap, to check the proper seating of the stoppers. A second station has been developed to verify the correct crimping and seal.
The technology has been well-proven in numerous cosmetic defect inspection stations that Seidenader have installed with great success on a worldwide basis.
The advantages of the Seidenader solutions are:
- no discussions with authorities regarding compliance with Annex 1, point 121
- same camera module for capping or inspection machines
- experience of over hundred integrated stations in operation
- documentation and testing available as to FDA expected levels
Companies in this press-release