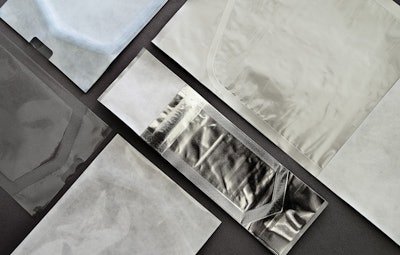
Rollprint Packaging Products expected to be the first sterile packaging manufacturer to convert pouches in a certified cleanroom environment in the U.S., with the construction of a 6,000-sq-ft cleanroom expected to be fully operational in the second quarter of 2012.
The ISO Class 8 cleanroom will be enhanced via Rollprint’s vertical integration, which means that the rollstock from which the pouches are made is also produced at the same facility in Addison, Ill. The company says no other pouch manufacturer has both vertical integration and cleanroom capabilities in the United States, making it another “first” for Rollprint.
A cleanroom environment has a controlled level of contamination that is specified by the number of particles per cubic meter at a specified size. ISO Class 8 Cleanroom certification dictates the following maximum concentration limits for airborne particulate (particles/m3) according to ISO 14644-1: 3,520,000 at 0.5 μm; 832,000 at 1 μm, and 29,300 at 5 μm.
“We started preparing for this two years ago with investments in vision systems, web cleaners, and other equipment and procedures to minimize particulates in our film converting area. We wanted to properly address upstream criteria before taking the next step,” says Dwane Hahn, the company’s vice president of sales and marketing.
The upgraded capability has been driven by customer demand for domestic supply that has been produced in a cleanroom environment. Pharmaceutical, medical device, and diagnostic/life science manufacturers are constantly looking for ways to reduce the number of contaminants that come in contact with their products, says Rollprint.
“There is a big difference between ‘cleanroom environments’ that some manufacturers claim they have, and actual cleanroom certification. In a few months time, we expect to be able to announce to the industry that we have met the rigorous certification criteria and are producing pouches in our cleanroom,” Hahn explains.
The cleanroom will house five production lines capable of producing a variety of pouch structures for which Rollprint is known, including header bags, chevron, vented, three-side weld seals, corner peels, etc.
“Many of the packaging structures used today for pharma and medical device applications—such as film and foil header pouches, coextruded, peelable heat-seal films and silicon oxide/aluminum oxide composites—were first introduced to the industry by Rollprint. The new cleanroom capability builds on that legacy,” says Hahn.