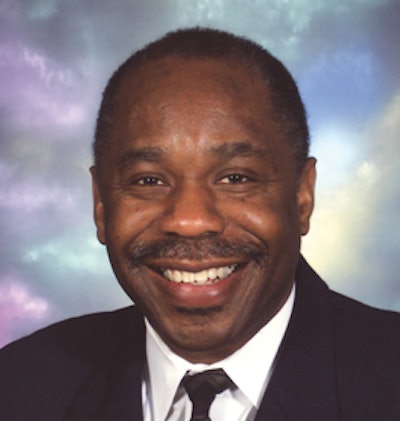
Sterling Anthony, CPP
For generations, the debate raged over whether glass was a liquid or a solid. And because glass doesn't molecularly abide by the rules of either of those states of matter, some have given up on liquid or solid and define glass as a supercooled liquid. More recently, glass has come to be defined as an amorphous solid. Let physicists continue to debate. From a packaging perspective, glass might not be supercooled, but it definitely is super cool.
No other single packaging material duplicates all of the advantages of glass: clarity (in addition to coming in a variety of colors); inert; impermeable to moisture and gases; odorless; capable of being formed into a variety of shapes; solid and reassuring to the touch; microwavable; reusable; and recyclable. The combination imparts a premium image to a wide variety of branded products. Additionally, there's a trend wherein products that once were packaged in glass but converted to other materials──plastics, primarily──are going "retro" with limited edition launches packaged in glass.
As to disadvantages, glass is relatively expensive, in the sense of purchase price. Glass also is relatively heavy, which translates to higher transportation costs. The most limiting disadvantage of glass, of course, is its fragility: it chips, cracks, breaks, and shatters. The disadvantages are interrelated; for example, source reduction (more practical for single-use containers than for multi-use ones) can reduce purchase price and transportation costs but can increase fragility (although container design and material distribution can offset, to a degree).
Ideally, glass containers come into existence pristine, a condition best for tilting the scale in favor of glass' advantages over its disadvantages. In reality, however, glass goes through figurative hell, given the temperatures of the furnace, and the stresses from molding the container and from annealing are in no way heavenly, either. So it is that glass containers can embody a variety of defects. Quality assurance, therefore, is indispensable to all three of the sequential stages of glass container manufacturing (batch house, hot end, and cold end). And since the cold end deals with the container's suitability to be shipped (or first labeled, if that's done at the facility), QA at that stage is synonymous with inspecting for defects.
Calling ‘em like you see ‘em
While in a self-defining sense defects are imperfections, they are more formally categorized as follows: critical, major, and minor. And although the lines of demarcation aren't always distinct, the categories correspond to defects that, respectively: make the container unfit for its purpose; considerably impair the container's fitness; and, are mostly of a blemish character. Furthermore, there's a nomenclature, some of it requiring no translation, such as cracks, blisters, and dirt, while some of it does, such as plugs, bird swings, and rocker bottoms.
Every glass container should undergo inspection. The issue is how that inspection is to be divided between humans and machines, that is to say, the naked eye and the electronic eye. Humans can be utilized to make visual inspections of statistically-determined quantities of containers. Laboratory measurements of the container's dimension's and relevant properties are another realm wherein humans can be utilized. Automated inspection, in complement, has capabilities that are most suited for high-output operations. Such inspection can reject defective containers (turning them into cullet to be recycled into the manufacturing process); moreover, computerization maintains real-time statistics that can be fed upstream to correct a problem, for example, a specific mold that's turning out an unacceptable quantity of defective containers.
The ever-present challenge to successful inspection is that defects can occur anywhere in the container; a bottle, for example, is subject to specific defects from top to bottom relative to its finish, neck, shoulder, body, and base. In acknowledgement, a glass manufacturing facility utilizes different inspection stations equipped with machinery of a dedicated purpose. One typically positioned at the front of the cold end is a spacer, the function of which is to minimize the chances of glass-to-glass contact. In that capacity, it's as much a defect preventer as a defect detector.
From the user's perspective
A user should have knowledge of glass inspection, not necessarily as much as that of a glass supplier, but certainly enough to evaluate a supplier's fitness in that category. The user's objective should be a relationship with a supplier wherein shipments are certified as having passed a comprehensive inspection process. That being the case, the user should be able to feed the containers into packaging line operations, confident that those containers embody the requisite quality.
Knowledge of inspection and of defects serves the user in the drafting of the document that's at the heart of the user/supplier relationship: the specification. Tolerances shouldn't be unreasonably tight; nonetheless, they should reflect state-of-the-art capabilities.
Another aspect of inspection concerns defects encountered after the container has been filled and sent into the supply chain. The user sometimes has to send someone out into the field to investigate a problem. With the right amount of experience, an investigator's "forensic" talents become almost CSI-like. Take, for example, the susceptibility of glass to stress fractures. The veteran investigator can distinguish, by the pattern, between fractures caused by internal pressure and fractures caused by external impact. And even when a container has been reduced to fragments, the fragments can reveal whether the stress occurred all at once or more slowly.
Glass protects, but it requires protection. However, the fewer the defects and the less their severity, the more a glass container can provide its many advantages. An inspection process that does the job benefits both supplier and user. It benefits consumers, too, from the standpoints of product quality and personal safety (after all, broken glass is sharp). And when all parties end up winners, that's a situation that's super cool.
Sterling Anthony is a consultant, specializing in the strategic use of marketing, logistics, and packaging. His contact information is: 100 Renaissance Center- Box 43176; Detroit, MI 48243; 313-531-1875 office; 313-531-1972 fax; [email protected]; www.pkgconsultant.com.
No other single packaging material duplicates all of the advantages of glass: clarity (in addition to coming in a variety of colors); inert; impermeable to moisture and gases; odorless; capable of being formed into a variety of shapes; solid and reassuring to the touch; microwavable; reusable; and recyclable. The combination imparts a premium image to a wide variety of branded products. Additionally, there's a trend wherein products that once were packaged in glass but converted to other materials──plastics, primarily──are going "retro" with limited edition launches packaged in glass.
As to disadvantages, glass is relatively expensive, in the sense of purchase price. Glass also is relatively heavy, which translates to higher transportation costs. The most limiting disadvantage of glass, of course, is its fragility: it chips, cracks, breaks, and shatters. The disadvantages are interrelated; for example, source reduction (more practical for single-use containers than for multi-use ones) can reduce purchase price and transportation costs but can increase fragility (although container design and material distribution can offset, to a degree).
Ideally, glass containers come into existence pristine, a condition best for tilting the scale in favor of glass' advantages over its disadvantages. In reality, however, glass goes through figurative hell, given the temperatures of the furnace, and the stresses from molding the container and from annealing are in no way heavenly, either. So it is that glass containers can embody a variety of defects. Quality assurance, therefore, is indispensable to all three of the sequential stages of glass container manufacturing (batch house, hot end, and cold end). And since the cold end deals with the container's suitability to be shipped (or first labeled, if that's done at the facility), QA at that stage is synonymous with inspecting for defects.
Calling ‘em like you see ‘em
While in a self-defining sense defects are imperfections, they are more formally categorized as follows: critical, major, and minor. And although the lines of demarcation aren't always distinct, the categories correspond to defects that, respectively: make the container unfit for its purpose; considerably impair the container's fitness; and, are mostly of a blemish character. Furthermore, there's a nomenclature, some of it requiring no translation, such as cracks, blisters, and dirt, while some of it does, such as plugs, bird swings, and rocker bottoms.
Every glass container should undergo inspection. The issue is how that inspection is to be divided between humans and machines, that is to say, the naked eye and the electronic eye. Humans can be utilized to make visual inspections of statistically-determined quantities of containers. Laboratory measurements of the container's dimension's and relevant properties are another realm wherein humans can be utilized. Automated inspection, in complement, has capabilities that are most suited for high-output operations. Such inspection can reject defective containers (turning them into cullet to be recycled into the manufacturing process); moreover, computerization maintains real-time statistics that can be fed upstream to correct a problem, for example, a specific mold that's turning out an unacceptable quantity of defective containers.
The ever-present challenge to successful inspection is that defects can occur anywhere in the container; a bottle, for example, is subject to specific defects from top to bottom relative to its finish, neck, shoulder, body, and base. In acknowledgement, a glass manufacturing facility utilizes different inspection stations equipped with machinery of a dedicated purpose. One typically positioned at the front of the cold end is a spacer, the function of which is to minimize the chances of glass-to-glass contact. In that capacity, it's as much a defect preventer as a defect detector.
From the user's perspective
A user should have knowledge of glass inspection, not necessarily as much as that of a glass supplier, but certainly enough to evaluate a supplier's fitness in that category. The user's objective should be a relationship with a supplier wherein shipments are certified as having passed a comprehensive inspection process. That being the case, the user should be able to feed the containers into packaging line operations, confident that those containers embody the requisite quality.
Knowledge of inspection and of defects serves the user in the drafting of the document that's at the heart of the user/supplier relationship: the specification. Tolerances shouldn't be unreasonably tight; nonetheless, they should reflect state-of-the-art capabilities.
Another aspect of inspection concerns defects encountered after the container has been filled and sent into the supply chain. The user sometimes has to send someone out into the field to investigate a problem. With the right amount of experience, an investigator's "forensic" talents become almost CSI-like. Take, for example, the susceptibility of glass to stress fractures. The veteran investigator can distinguish, by the pattern, between fractures caused by internal pressure and fractures caused by external impact. And even when a container has been reduced to fragments, the fragments can reveal whether the stress occurred all at once or more slowly.
Glass protects, but it requires protection. However, the fewer the defects and the less their severity, the more a glass container can provide its many advantages. An inspection process that does the job benefits both supplier and user. It benefits consumers, too, from the standpoints of product quality and personal safety (after all, broken glass is sharp). And when all parties end up winners, that's a situation that's super cool.
Sterling Anthony is a consultant, specializing in the strategic use of marketing, logistics, and packaging. His contact information is: 100 Renaissance Center- Box 43176; Detroit, MI 48243; 313-531-1875 office; 313-531-1972 fax; [email protected]; www.pkgconsultant.com.