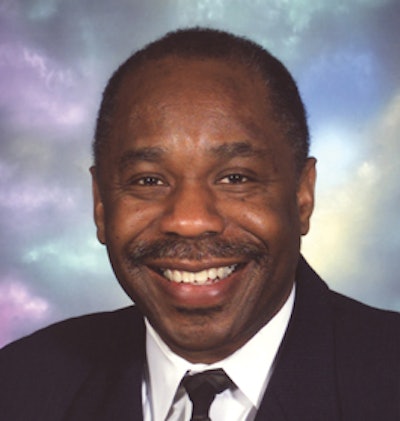
Sterling Anthony, CPP
The unit load, as a concept, is so elegantly simple that it requires no technical expertise to grasp; for, common sense informs that it’s more efficient to handle items assembled in a load than it is to handle them individually.
Assured of inherent efficiencies, many CPGC’s don’t put the strategic thought into unit load design that it deserves. Too often, unit loads are allowed to evolve from a disjointed process. First, the primary package is designed. Then, pack-counts within secondary and tertiary packaging are chosen by convention (typically multiples of a dozen). Lastly, a pallet pattern is chosen. Voila! A unit load, but not one that will fulfill its potential.
As with all matters associated with packaging, the design of a unit load should be undertaken from a systems approach. The components should be identified, their interactions understood, and trade-offs made for the optimal net effect to the system. The backdrop to all of this is logistics.
How well are you handling things?
The unit load principle is one of twenty (by traditional count) that define the discipline of material handling. The packaging and material handling kinship is the basis for the National Institute of Packaging, Handling & Logistics Engineers and was the basis for the Society of Packaging & Handling Engineers (before it merged with the Packaging Institute to form today’s Institute of Packaging Professionals).
A unit load mandates the use of material handling equipment. The load affects the operational efficiencies of the equipment and the equipment affects the integrity of the load. The most common example is the one between load and fork-lift truck. Often, critical aspects of that interdependency go unknown.
Just because the weight of the load is within the lift capacity of the truck doesn’t mean that all is well. A case-in-point is when the height of the load only allows for one-at-a-time handling, but a shorter height allows stacked-two-high handling, with the two shorter loads comprising more units than the one taller.
Regardless of whether loads are handled singly or stacked, often the fork-lift driver’s field of vision is limited. Consequently, the driver relies on: the impact of the mast against the load as indication that the forks have been inserted into the pallet; and, the impact of the pallet against a supporting surface as indication that the load has been placed and the forks can be withdrawn. Those impacts can be more than mere taps, especially given the rushed pace of most fork-lift operations. The damage from impacts can be exacerbated by conditions such as pallet overhang.
Conveyors are another type of material handling equipment that can affect unit load performance (and vice-versa). Unlike roller conveyors that contact and support the entire bottom of the pallet, a roller-skate conveyor suspends the pallet between two rails. If the pallet lacks sufficient strength and stiffness, it can bow under its load. Such deformation can, among other results, cause fasteners to loosen and makes for an unsafe load.
And, on the topic of worker safety, each year OSHA records a multiplicity of injuries attributable to unstable unit loads. Not all, though, are suffered while the load was being handled; some workers have the misfortune of being in the vicinity at the time that a load rendered unstable by previous handling, suddenly topples.
In for the long haul
The composition of a unit load affects the cube utilization within the transportation equipment (including intermodal containers). The less dense and the more lightweight the unit loads, the greater the diseconomies, as they cause the equipment to reach its cubic capacity rather than its weight capacity. Admittedly, some products offer limited opportunities for improvement---good luck making weight with paper towels, for example.
Nonetheless, as with the fork-lift example, the height of the load is a key factor. Instances abound wherein transportation equipment goes underutilized because unit loads can’t be stacked. Not that the issue is resolved at that point. Without adequate blocking and bracing, stacked loads won’t remain immobile during transit, as many a consignee has discovered upon opening the door to a jumbled mess (prayerfully, without getting injured by falling items, in the process).
A CPGC that utilizes more than one mode of transportation should design unit loads for the most imposing and restrictive mode; for example, between truck and railcar, the loads should be designed to satisfy the requirements of the truck.
Give it a rest
Neither by material handling nor transportation are unit loads always in motion, hence the storage function. Complicating matters is the fact that storage can take the form of loads stacked on one another from the floor up, to highly-automated, rack-supported facilities. Whichever the type of warehouse or distribution center, material handling is required to get the loads into and out of storage; therefore the preceding comments concerning that activity apply here. And, the previously mentioned phenomena of bowing pallets can be a concern with those types of storage racks that suspend the pallet rather than support its entire bottom.
Compression, however, is a factor more closely associated with storage. If it is foreseeable that a unit load will have other weight superimposed on it, the reality should be factored into the design of the unit load. And, since compression can be dynamic but also work its effects across time, loads should be designed with a certain targeted period of storage in mind. Incidentally, compression also is to be factored if loads are stacked in transportation equipment.
As if we needed more
Optimizing the unit load to perform under conditions of material handling, transportation, and storage is challenging enough. The prospects for success depend on whether the CPGC knows the characteristics of each component and whether that knowledge is applied to systems optimization rather than just component improvement. Otherwise, the company might find itself chasing, for example, component cost savings at the expense of increased operating costs.
There are computer programs, from various sources, that purport to model the components and their interactions. Such programs only are as effective as the inputs into them are reliable; and, therefore, do not excuse the CPGC from the necessity of being knowledgeable about its individual circumstances. Technology is not a substitute for homework.
A similar caution is in order regarding physical testing of unit loads, the relevance of which depends on how accurately it duplicates actual conditions—again placing the onus on the CPGC to know its environments.
Adding to the complexity are some recent trends at the retail level. Buy-from-pallet--the darling of club stores--is expanding into other types of retail venues. When the unit load doubles as a merchandising tool, a premium is placed on loads arriving in display condition. Beyond that, loads are expected to require the minimum work from store personnel, little more than wheeling the loads onto the floor. Then too, there’s the issue of retailer-demanded RFID at the unit load level, causing CPGC’s to decide a course relative to that technology.
And, is there anything related to packaging that isn’t affected by the sustainability movement? Hardly. Therefore, an additional challenge concerns the design of unit loads that are green without a sacrifice in performance, including disposal at the retail level.
Worth the effort
Consider a typical unit load, consisting of product, packaging, and pallet: all together, the value is in the hundreds, if not thousands of dollars. Every unit load represents an investment. Every unit load represents a means to increase cost savings and operational efficiencies throughout the logistics channel. Such is the stuff that leads to a competitive advantage.
E pluribus unit load: from many (factors), a unit load. It can prove to be a fitting motto for the currency that it generates for the company’s coffers.
Sterling Anthony is a consultant, specializing in the strategic use of marketing, logistics, and packaging. His contact information is: 100 Renaissance Center-176, Detroit, MI 48243; 313-531-1875 office; 313-531-1972 fax; [email protected]. His website is www.pkgconsultant.com.
Assured of inherent efficiencies, many CPGC’s don’t put the strategic thought into unit load design that it deserves. Too often, unit loads are allowed to evolve from a disjointed process. First, the primary package is designed. Then, pack-counts within secondary and tertiary packaging are chosen by convention (typically multiples of a dozen). Lastly, a pallet pattern is chosen. Voila! A unit load, but not one that will fulfill its potential.
As with all matters associated with packaging, the design of a unit load should be undertaken from a systems approach. The components should be identified, their interactions understood, and trade-offs made for the optimal net effect to the system. The backdrop to all of this is logistics.
How well are you handling things?
The unit load principle is one of twenty (by traditional count) that define the discipline of material handling. The packaging and material handling kinship is the basis for the National Institute of Packaging, Handling & Logistics Engineers and was the basis for the Society of Packaging & Handling Engineers (before it merged with the Packaging Institute to form today’s Institute of Packaging Professionals).
A unit load mandates the use of material handling equipment. The load affects the operational efficiencies of the equipment and the equipment affects the integrity of the load. The most common example is the one between load and fork-lift truck. Often, critical aspects of that interdependency go unknown.
Just because the weight of the load is within the lift capacity of the truck doesn’t mean that all is well. A case-in-point is when the height of the load only allows for one-at-a-time handling, but a shorter height allows stacked-two-high handling, with the two shorter loads comprising more units than the one taller.
Regardless of whether loads are handled singly or stacked, often the fork-lift driver’s field of vision is limited. Consequently, the driver relies on: the impact of the mast against the load as indication that the forks have been inserted into the pallet; and, the impact of the pallet against a supporting surface as indication that the load has been placed and the forks can be withdrawn. Those impacts can be more than mere taps, especially given the rushed pace of most fork-lift operations. The damage from impacts can be exacerbated by conditions such as pallet overhang.
Conveyors are another type of material handling equipment that can affect unit load performance (and vice-versa). Unlike roller conveyors that contact and support the entire bottom of the pallet, a roller-skate conveyor suspends the pallet between two rails. If the pallet lacks sufficient strength and stiffness, it can bow under its load. Such deformation can, among other results, cause fasteners to loosen and makes for an unsafe load.
And, on the topic of worker safety, each year OSHA records a multiplicity of injuries attributable to unstable unit loads. Not all, though, are suffered while the load was being handled; some workers have the misfortune of being in the vicinity at the time that a load rendered unstable by previous handling, suddenly topples.
In for the long haul
The composition of a unit load affects the cube utilization within the transportation equipment (including intermodal containers). The less dense and the more lightweight the unit loads, the greater the diseconomies, as they cause the equipment to reach its cubic capacity rather than its weight capacity. Admittedly, some products offer limited opportunities for improvement---good luck making weight with paper towels, for example.
Nonetheless, as with the fork-lift example, the height of the load is a key factor. Instances abound wherein transportation equipment goes underutilized because unit loads can’t be stacked. Not that the issue is resolved at that point. Without adequate blocking and bracing, stacked loads won’t remain immobile during transit, as many a consignee has discovered upon opening the door to a jumbled mess (prayerfully, without getting injured by falling items, in the process).
A CPGC that utilizes more than one mode of transportation should design unit loads for the most imposing and restrictive mode; for example, between truck and railcar, the loads should be designed to satisfy the requirements of the truck.
Give it a rest
Neither by material handling nor transportation are unit loads always in motion, hence the storage function. Complicating matters is the fact that storage can take the form of loads stacked on one another from the floor up, to highly-automated, rack-supported facilities. Whichever the type of warehouse or distribution center, material handling is required to get the loads into and out of storage; therefore the preceding comments concerning that activity apply here. And, the previously mentioned phenomena of bowing pallets can be a concern with those types of storage racks that suspend the pallet rather than support its entire bottom.
Compression, however, is a factor more closely associated with storage. If it is foreseeable that a unit load will have other weight superimposed on it, the reality should be factored into the design of the unit load. And, since compression can be dynamic but also work its effects across time, loads should be designed with a certain targeted period of storage in mind. Incidentally, compression also is to be factored if loads are stacked in transportation equipment.
As if we needed more
Optimizing the unit load to perform under conditions of material handling, transportation, and storage is challenging enough. The prospects for success depend on whether the CPGC knows the characteristics of each component and whether that knowledge is applied to systems optimization rather than just component improvement. Otherwise, the company might find itself chasing, for example, component cost savings at the expense of increased operating costs.
There are computer programs, from various sources, that purport to model the components and their interactions. Such programs only are as effective as the inputs into them are reliable; and, therefore, do not excuse the CPGC from the necessity of being knowledgeable about its individual circumstances. Technology is not a substitute for homework.
A similar caution is in order regarding physical testing of unit loads, the relevance of which depends on how accurately it duplicates actual conditions—again placing the onus on the CPGC to know its environments.
Adding to the complexity are some recent trends at the retail level. Buy-from-pallet--the darling of club stores--is expanding into other types of retail venues. When the unit load doubles as a merchandising tool, a premium is placed on loads arriving in display condition. Beyond that, loads are expected to require the minimum work from store personnel, little more than wheeling the loads onto the floor. Then too, there’s the issue of retailer-demanded RFID at the unit load level, causing CPGC’s to decide a course relative to that technology.
And, is there anything related to packaging that isn’t affected by the sustainability movement? Hardly. Therefore, an additional challenge concerns the design of unit loads that are green without a sacrifice in performance, including disposal at the retail level.
Worth the effort
Consider a typical unit load, consisting of product, packaging, and pallet: all together, the value is in the hundreds, if not thousands of dollars. Every unit load represents an investment. Every unit load represents a means to increase cost savings and operational efficiencies throughout the logistics channel. Such is the stuff that leads to a competitive advantage.
E pluribus unit load: from many (factors), a unit load. It can prove to be a fitting motto for the currency that it generates for the company’s coffers.
Sterling Anthony is a consultant, specializing in the strategic use of marketing, logistics, and packaging. His contact information is: 100 Renaissance Center-176, Detroit, MI 48243; 313-531-1875 office; 313-531-1972 fax; [email protected]. His website is www.pkgconsultant.com.