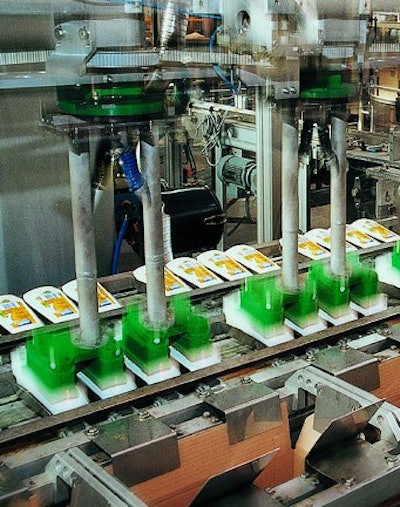
They solved it by using a TopLoader from SIG Pack Systems (Beringen, Switzerland).
SC Johnson sought to meet two major goals. First, the new packaging solution had to meet the rising demand by increasing the output per operating shift. Second, it had to deliver a more efficient means of secondary packaging for the Glade containers.
The handling of the individual containers is a challenge due to the wedge shape of the container and because the scented contents are jelly-like and wobble when the containers are handled. Every other package has to be rotated 180 deg so that they can be placed evenly to enable efficient stacking into the shipping carton.
SC Johnson replaced one of its existing robot cells with a TopLoader from SIG for the packaging task. This robot cell has two independently fed product inflows, each of which feeds an automatic grouping unit. In a simultaneous process, cartons are fed into the cell, positioned and then filled with the Glade products. The TopLoader automatically selects which of the two grouping units it takes the products from. Depending on their size, the cartons are filled with varying numbers of air fresheners.
To rotate every second product by 180 deg before insertion into the carton, SIG's engineers developed a special gripper that uses a vacuum system. This gripper ensures that, even during the rapid rotation, the products do not fly away or become damaged.
Operating efficiency has been assured using Internet connections. The operator panel is a touch screen display with a user-friendly Windows NT interface. The software links, via the Internet, to SIG's Service department. If a problem occurs, at any time of day or night, SIG specialists can log onto the machine directly and usually solve the problem without the need for time consuming site visits. ES