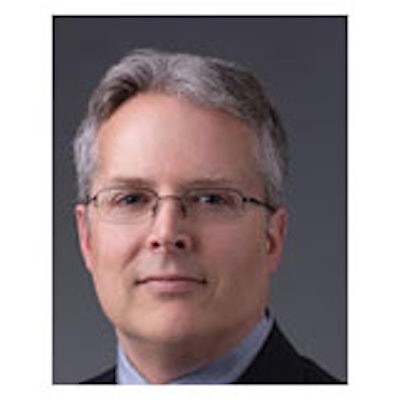
Packaging World:
Can you give us a sense of how many FATs you conduct?
John Giles:
At Amway we typically conduct at least 15 FATs each year, covering a wide range of both processing and packaging equipment. These could vary from a $50,000 labeler, up to a $2 million filling machine.
How many people are sent to an FAT?
For Amway, the complexity of the equipment will dictate how many and who attends. In the past, we sent up to 15 people but found that it can become a zoo and it’s not a good experience. Today, we send an individual from our maintenance group, a setup technician, and of course engineering giving us a total of 2-6 individuals. We love to give our guys initial exposure to the equipment with the potential for some advanced training during changeovers, and they can meet the OEM personnel. This helps establish critical relationships that can pay off during equipment start-up. We also want to make sure that we have the same group of individuals attending the FAT that will be responsible for starting up the equipment when it goes through validation and into production.
Where does safety come in?
Safety is critical, and it’s probably one of those things that was somewhat overlooked in the past. As an example, individuals would tend to ignore requirements for PPE (personal protective equipment) and become relaxed with guarding and electrical requirements. Today we pay a lot more attention to safety, and it’s something you need to discuss before you start executing the FAT. We treat the FAT as if it were an operation in our own facility and apply the same rules, bringing our own PPE equipment so there is not an issue with availability. Basically, don’t relax your standards and say, ‘we’re just going to run this quick test and then it will be over with.’ The FAT is never successful if an injury occurs, regardless of the equipment performance.
Some CPG companies speak of a FAT pretest. Do you include this?
Yes, it’s something we started over ten years ago and it’s a requirement for us today. Most of the time, it’s a two- to five-minute pretest to make sure that everything is working satisfactorily before you start running your longer 15- to 30-minute (or more) FAT run. It demonstrates that the equipment is ready and will meet the agreed-upon criteria between the OEM and CPG. For larger or critical pieces of equipment, we will send 1-2 individuals (Engineer, Technician) 2-3 weeks in advance to make sure the equipment is performing as expected and that the action plans are in place to be ready for the full FAT. This helps make sure that everything is on track before committing the expense and time to conduct the FAT.
How early in the equipment purchasing process should communication about the FAT begin?
It should start during the request for proposal (RFP) process. I can’t emphasize this enough as it helps lay out your expectations and requirements early in the process. The ability to conduct the FAT along with the cost, will influence your decision on which OEM to choose. Also, for large tests, it helps you budget appropriately as the OEM may pass on costs for executing the FAT. Another important aspect is that it starts the internal discussions much earlier in the process and helps get everyone on board with expectations for the FAT. You really want to make sure you’ve got the key individuals involved who are going to make the call on quality requirements, a specific component look, or whatever types of attributes you are going to measure.
What if significant changes are required during the project?
You should be discussing those immediately with your OEM, come to an agreement on the resolution, and document the changes as the project progresses. We have found that strong relationships and robust communication between the OEM and CPG are critical to the project success. The overall goal is to avoid surprises at the FAT and if these occur, the root cause is always related to communication.
What kind of resources are out there?
I would recommend CPGs use the OpX protocol and checklists. It’s available to help you standardize FAT executions for your organization and the OEM. Most important, it’s a common tool to help foster discussions and communication. The bottom line is that successful FATs lead to better installations, qualifications, and production start-up, which means success for everyone on the project team.
Note: The OpX protocol and checklists can be downloaded for free at pwgo.to/3821, or you can visit www.opxLeadershipnetwork.org for the FAT and other work products. Also, a September 2018 webinar featuring Amway’s John Giles, interviewed above, discussed the value and application of the OpX Leadership Network’s FAT work product through real-world examples. Watch the webinar in its entirety at pwgo.to/3820.