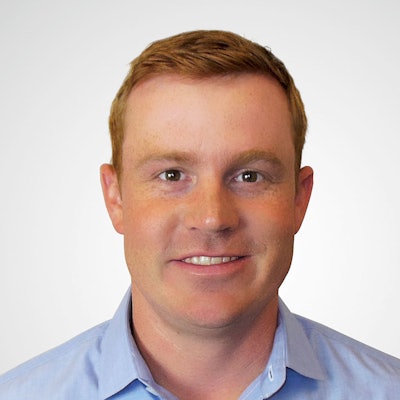
As usual, the summit provided a venue for all of the poker players at the table to briefly show their hands and begin to work in parallel. Since directly reporting on the summit is rightfully prohibited—participants need to speak candidly for this kind of meeting to work—I’ll use this space to reflect highlights anonymously.
Machine builders are always applying pressure to CPGs to integrate the latest equipment and obsolete whatever’s there now. Sometimes there are obvious occasions to do so, like the launch of a new product that legacy equipment can’t run, or a cost/benefit analysis that shows great returns.
But most of the machines in manufacturers’ facilities are on seven- to 10-year depreciation curves, and while on the curve, every case coming off the line carries cost allocated against paying off that equipment. Once that machine is off the curve, there’s a strong incentive to keep that machine running for years to come, like a lower mileage car that has just been paid off.
Packaging engineers and operators on the floor recognize when mileage is beginning to pile up. The problem is, procurement is incentivized not to recognize it as long as those machines keep purring—they delay an upgrade as long as possible. CPGs need to leverage allies at the OEMs to quantify and justify equipment replacement in terms that procurement can understand.
At a high level, CPGs absolutely recognize that reinvestment in the business is necessary. But reinvestment in packaging machinery has to be balanced against other pressing needs, from fixing a parking lot pothole to updating the HVAC. A CPG with a careful, multiyear obsolescence plan for new and existing lines, developed in conjunction with OEMs that are intimately aware of the existing equipment and the capability of emerging technologies, was agreed to be the best armor in ensuring CPGs aren’t sweating their assets, and themselves, to death.
And consider incremental obsolescence for controls on machinery. Controls suppliers are often at the mercy of third-party licensors of components within the control. When volume of an old design drops to only a few per year, they may discontinue it, thus obsoleting the whole panel or PLC. Staying up to date helps, as does moving all controls upgrade costs to the M&R (maintenance and repair) ledger instead uttering the (dirty, to some) word ‘obsolete.’ It might be smoke and mirrors, but it can keep all three parties engaged in the same goal of optimizing your machine’s life without forcing your suppliers to inventory 30 years’ worth of parts. But if you must? Consider getting some skin in the game with a sort of retainer for aftermarket support and service.
Robotics was another area of lively panel discussion. While the benefits seem obvious, installations can produce a cascade of new challenges that can be seen as more headache than they’re worth, according to CPGs at the summit. For instance, is a CPG’s safety department up to speed on codes around ANSI and ISO? Can it integrate an optimized system from a range of arm, EOAT, and vision suppliers? What sorts of training will the installation entail?
But more important, it’s about jobs. For the CPG, there’s the worry about having institutional knowledge to program and maintain the thing. And from the CPG’s workforce’s perspective, there’s a tangible sensitivity around robots taking jobs. But OEMs and CPGs converged on the idea that it’s more a framing and perception problem. The panelists—all of whom are using robots in production—said it’s not about swapping in a machine in place of a person. It’s leveraging technology to make a better working environment. As such, introducing robots isn’t automating a job out of the system, it’s building a new skillset into people there and making them more valuable. Yesterday, one person was packing a box. Tomorrow, one person will be managing multiple lines with robots on them. Gone are the dirty, dull, and dangerous jobs. Give those to the robots, and let your existing workforce go onto something more interesting, perhaps in wrangling robots.
Share best practices and swap stories with your OEM suppliers at PACK EXPO Las Vegas, perhaps at the Vision 2025 thought leadership workshop. Download results from last year’s discussion at pwgo.to/5007.