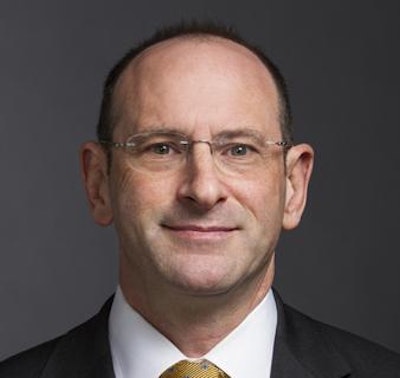
In this Q&A, Legal + Regulatory Columnist Eric Greenberg gains the insights from Troy Fugate, Vice President, Operations at Compliance Insight, Inc., the Cincinnati-based medical products compliance consultants, into some the interplay of packaging, especially changes in packaging, with a company’s overall manufacturing and quality programs. The theme of his answers: To avoid regulatory or customer issues, don’t assume anything, and check for any unintended consequences.
Healthcare Packaging: We know that validation of processes and formulations is a key component of GMP and quality system programs. When or how must re-validation be performed for packaging materials, machinery or processes?
Fugate: There are two aspects to revalidation with any system—whether they are equipment, processes or formulation. The first aspect is in relation to change control. Any system that has an impact upon GMP operations must be controlled via a change control program. Changes have to be assessed for potential impact upon a myriad of items including, but not limited to, regulatory filings, procedures, forms, training and…validation. The assessment of potential impact due to the change can be tricky. For instance, if a packaging material is changed, how do you know there is no impact to the functionality of the packaging equipment? The incorrect assessment of the change as having no impact has led to many FDA observations. What may be initially considered as a minor change has often resulted in unintended consequences. Be very careful with the assessment of change impact—if nothing else, have some data gathered to reflect the basis of your decision.
The second aspect of revalidation is time. Over time, things change.Even small changes that have no impact can be accumulative on the overall process. Revalidation over some time frame as defined by the company is typically performed. Some firms select a general time period—say three years. Others select a time period based upon a risk assessment of the process—with critical functions being performed more regularly than non-critical functions. Either way, document your strategy in a procedure and verify that you follow it.
Would your answer be any different for occasions when packaging structures or materials are changed for an existing product?
Fugate: For revalidation of these changes for existing products, it becomes even more important to control the changes as the products are more readily sent to the market prior to the identification of issues. Remember, validation is the process by which documented evidence is available that the process has a high probability of successfully meeting predetermined criteria.If that process changes, the probability always increases that it will NOT meet acceptance criteria. Once you make the change and the product makes it to the market prior to an issue being identified, you have to answer the question, “What is the impact to the product on the market?” All you need is to have customer complaints, investigations and problems with product on the market to trigger an audit. If the audit findings can connect the dots of issues related to changes, then you have a mess on your hands.
Would you expect the growth of personalized medicine or therapies will add to the needs for packaging validation? If so, might that point a company toward using a specific packaging type or technology to avoid infinitely complex validation steps for each new product?
Fugate: There is every expectation to think that growth of personalized medicines will add to the complexities of packaging validation. Different medication formulations—being either different raw materials or different concentrations—can result in potential concerns for packaging configurations. Stability, leaching or extraction complexities are the first to come to mind. If there is a potential for a company to identify and utilize a standard packaging type or technology, it would certainly be prudent to consider the business and compliance ramifications in utilizing them.
Editor’s note: Troy Fugate is VP, Operations at Compliance Insight, a compliance service provider for the pharmaceutical and medical device industries worldwide. The company focuses on quality, regulatory and clinical compliance. Fugate serves in various roles, including GMP compliance, FDA mitigation, compliance assessment for risk, and tactical growth and development.