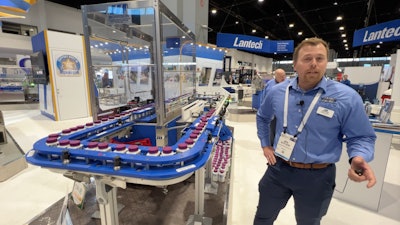
With Morrison’s Down Bottle Reject System, brands and CPGs in the beverage, pharma, beauty, and personal care spaces (among any other markets using rigid or semi-rigid markets) are finding a cost-effective system that can help to increase ROI and line efficiency. And while that's happening, they can shift their workforce to other places in the facility that matter.
"A big feature of this system is that we maintain center lines during container changeover," says Seth Licke, Aftermarket Sales and Service Manager/Project Manager at Morrison Container Handling Solutions. "So if you have, for example, 17 different containers that run on the same line, you wouldn't have to mechanically move anything during the changeover. It would just be a simple, quick change part for each container size, using tool-less removal and maintaining the centerline on your conveyor. And then, just by using the geometry of the bottle, and getting it at least 50% of its mass off of the conveyor, that allows [gravity to take over and] the bottle to reject."
Often, companies experience line inefficiencies due to containers falling over. Instead of having a person standing on the line looking for down containers, it’s more cost effective and efficient to implement a Down Bottle Reject System.
Plus, the mechanical system operates on a CPG's line with no additional operating costs. Since it relies on bottle geometry, a user will need no air, pneumatics, or electric/motor to utilize the technology.
And ultimately, by reducing down bottles, operators can increase uptime in their production and throughput of product by reducing jams on the line.
While the system is infinitely scalable in theory, the most common applications are in the 50 to 400 containers/min speed range.