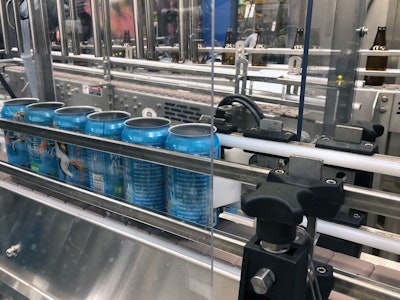
In the state that serves as the nation’s traditional home for all things beer, Madison Wisconsin’s Karben4, a 15-barrel brewhouse and taproom, serves brew aficionados from around the state with eclectically branded and lovingly crafted beer. Kegs for foodservice and bar channels, plus bottles for retail outlets, had been the name of the game since the brewery hung out a shingle in 2013, but owners sought to get in on the growing aluminum can trend in microbrewing. This would require a new depalletizer, plus a new can filler/sealer that would feed into a single manual pack-out area shared by bottle and can lines. But as a lot of microbreweries experience, space was quite limited in the facility.
Ryan Koga, brewmaster and co-owner, had to consider how to fit the new equipment into the existing layout without having to buy a bigger building. The dilemma he faced was all about layout: less the individual footprints of the existing and new equipment, and more the conveyors and material handling that would have to efficiently connect it all together in as little space as possible. Where would the canning line go, how could he get cans into the filler, then off the filler into labeling and packaging? How would he deal with the sudden influx of different sizes among the cans (12 oz, 16 oz, etc. compared to the single 12-oz bottle), and could he use a single labeler and pack-out station for everything?
The company turned to Multi-Conveyor, another Wisconsin staple located a stone’s throw away from Madison in Wisconsin’s Fox Cities, to assist with the layout. The solution was a bold one, using long stretches of single-lane conveyor for both bottles and cans instead of doubling up with dedicated lines. This meant using side-transfers to introduce either bottles or cans, depending on what is being run on any given day, to the universal conveyor sections. Multiple side transfers were installed from the rinser to the single-filer, again from the side transfer onto the existing filler. Cans were also side-transferred from the rinser and side-transferred off onto the new bottle infeed conveyor.