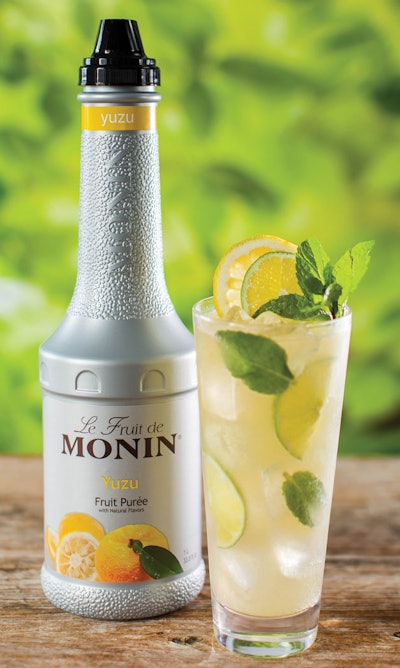
Amid a flurry of network and cable television shows introducing consumers to elevated culinary sensibilities, the American consumer is more willing to experiment with flavors. According to Food and Wine magazine, more sophisticated attitudes toward food extend to home cooks and the foodservice industry alike. In this environment, Monin Gourmet Flavorings is really hitting its stride in U.S. production.
That’s not to say that Monin, headquartered in Bourges, France since 1912, is new to the U.S. The company’s syrups and flavorings have long reached chefs, baristas, and bartenders here via import distribution. But in 1996 the company established its Monin Americas production and packaging facility in Clearwater, FL, under the leadership of Bill Lombardo, CEO. Business grew steadily since then, but recently the growth graph is resembling a hockey stick.
Mike Brewster, Chief Production Officer, Monin Americas, arrived just in time for the spike. When he joined the company in February 2014, it was running at 45,000 flavoring bottles per day. By late 2015, that had grown to 65,000 per day, and by the beginning of 2017, it had gone to 85,000 per day. Brewster says he can’t be sure what the daily output is now as it’s a moving target, but it’s north of 85,000. In 2017, the facility eclipsed 20 million bottles produced.
“The exciting thing for the team here is that they’ve accomplished this output growth on the same production shifts,” Brewster says. “We basically absorbed the higher output with the original crew. At first, we were able to handle the load with improved scheduling, and a lot of little things that collectively allowed us to improve efficiency.”
But for production to continue to grow without taking on more labor, it was clear to Brewster that a packaging equipment upgrade would be necessary. This was a two-pronged process, with preparatory upgrades to the middle of the packaging line occurring in the summer of 2015. Then in 2017, phase two began with a focus at the beginning of the packaging line. These latest changes provide nearly triple production, from less than 100 bottles/min to 240 bottles/min.
Depalletizer kicks off improvement cascade
While Monin’s flavorings, syrups, and fruit purees are available in a variety of specialty formats, the greatest volume is in 1-L bottles (PET for flavorings and syrups, HDPE for purees), 750-mL glass and also 64-oz HDPE bottles. Despite feeding interchangeably into the same two primary filling lines, both the glass and plastic formats had needed to be handled separately. Monin had used a vacuum-assisted manual depalletizing operation to feed both the plastic and the glass lines. Glass bottles were manually lifted onto conveyors via hoist, while plastic bottles were being bulk de-scrambled using a hopper and sorter. This could often be a messy process, with a lot of scrap.
“While we were doing by-hand bottle depalletizing, we had a case packer that could only run 100 bottles per minute, even after our 2015 upgrades. That was the weakest link in the chain, and even then we could barely keep up with depalletizing. It used a lot of labor, created a lot of waste, and took up lot of room.”
Monin had some specific challenges based on its available floor space, line speeds, and backlog requirements. Brewster was looking for a compact and versatile solution to supply all of the bottle styles to the production lines. He had considered various options, but was repeatedly told they weren’t viable with the space available. So in 2017, Monin contacted A-B-C Packaging Machine Corp. to work on a depalletizing solution that would speed things up while limiting line disruption and reducing waste.
Upon review of these challenges, A-B-C proposed supplying one depalletizer to feed both lines, conserving floor space for the bottle backlog that was critical to keeping their lines running smoothly. “Our Model 108 depalletizer is unique as it runs glass and plastic containers of different sizes interchangeably, without any changeover or change parts required. It senses each pallet layer height and load automatically to provide seamless operation for different bottle styles,” says Don Neher, A-B-C sales manager. The machine currently depalletizes 1-L, 750-mL, 500-mL, 375-mL, and 64-oz bottles and feeds three production lines at the Monin plant.
Another key component was a custom dual pallet transfer supplied by A-B-C to index pallets of containers as required to the depalletizer. After each layer of bottles is unloaded from the pallet, the layer is transported to the discharge table where a shifting mechanism feeds the bottles to the appropriate line while running at full speed. The new depalletizer has replaced Monin’s previous operations, eliminating labor and problems with downed and damaged bottles while providing a consistent bottle supply to all lines.
Smart conveyors and line efficiency
A-B-C configured the machine speed and layout to provide a bottle backlog that would keep the lines running efficiently. To keep the line output consistent and avoid disruption, Monin needed at least 2,000 bottles of accumulation on each primary line for top efficiency. Operators also needed enough time to switch pallets, from glass to plastic or vice versa, without stoppage.
To ensure sufficient accumulation, the depalletizer relies on information fed from downstream into its PLC. That’s where Garvey Corp. came in with a smart conveyor system to accomplish this feedback loop with the depalletizer and maintain glass and plastic accumulation levels. The new depalletizer feeds Garvey conveyors in mass, and bottles are single filed into a rinser before entering either of two primary filling lines.
But Garvey saw plenty of room for improvement well beyond the front of the line. After the two primary filling bays, the existing line had relied on two undersized bi-directional accumulators attempting to single file product to the labeler and the case packer. One of the existing case packers also had issues with laning the product, causing line control and jamming issues that lowered the overall line efficiency.
“Through a Garvey Line Analysis, we right-sized and located one Infinity accumulator between the filler and labeler,” says Tom Lauchert, regional sales manager at Garvey. “We also added a smaller multi-lane outfeed Bi-Flo prior to the case packer to solve the laning issues. Ultimately, this resulted in an increase in the number of cases per shift, the elimination of jamming issues, a reduction in label damage, and a reduction in labor.”
Without accumulation, the line is only going to run as fast as the slowest machine rate multiplied by the combined efficiency of all the machines in the line. With accumulation, the line will run as fast as the slowest machine group rate multiplied by its combined group efficiency. Garvey’s line analysis calculations showed an available 29% gain based strictly on the addition of accumulation tables, and Monin was able to realize and take advantage of these predicted efficiency gains.
Brewster uses accumulator fullness as a quick barometer of line health. “If everything is running in steady state, then there a few, but not many bottles being accumulated. I like to see some accumulation being used to be sure we won’t be starved for bottles in an event, but when the accumulation systems are pretty empty, that means the filler is running, the labeler is running, and life is good. But when there is an upstream or downstream issue, accumulation drastically smooths out the line, and gives us the elasticity we need.”
Puree bottle structure
Monin’s longstanding syrup bottles have needed to cover two different ends of the spectrum, from an end-user needs perspective. Glass bottles offer a high-end feel for consumer-facing applications, while PET plastic bottles deliver on convenience and safety in back-of-house applications or higher volume situations.
Monin’s line of fruit purees combine the two functionalities. These purees are available in 1-L, silver-colored, HDPE bottles that feature a long, textured, neck. The bottle’s shape provides a unique appearance and offers a slip-resistant grip for coffee shop baristas, restaurant chefs, and bartenders.
The bottle’s function has been further enhanced with a Monin-patented 43-mm polypropylene dispensing closure that can be activated with one finger and includes a no-glug feature. With the help of TricorBraun, Monin re-engineered the bottom parameters of the bottle to minimize rocker bottoms on the bottles after nitrogen dosing. The nitrogen assists in extending the product’s shelf life. A pressure sensitive paper label is used.
Packaging as social responsibility
Whether glass, HDPE, or PET, all Monin bottle SKUs are 100% recyclable and employ 20% recycled content and water-soluble, soy-based ink. The company also uses molded pulp packaging inserts and has abolished the use of EPS. All label paper is certified by the Forest Stewardship Council (FSC) and is Elemental Chlorine Free, two of the most important environmental qualities a paper can have, and all Monin 1-L syrups and purees are packaged in BPA-free bottles.
As a flavoring company that is particularly attuned to issues related to natural florals and botanicals, Monin has turned its attention in recent years to honey bees and the global issues surrounding the scourge of colony collapse disorder. Since 2008, Monin’s recycling initiatives have involved sending waste syrups to feed bee colonies. The program has fed 374 million bees and counting, to date.
Wise water use
Monin was recognized by the EPA as WasteWise Partner for commitment to waste reduction. Initiatives toward this designation included:
• Recycle all manufacturing and warehousing wastes
• Office recycling program
• Green packaging—water soluble soy based ink, 20% recycled content, 100% recyclable, pulp packaging inserts, zero Styrofoam
• On-site wastewater treatment for pH and temperature
• Waste syrup used for feeding bees and by the city of Clearwater for municipal wastewater treatment
• Strong focus on source reduction and water conservation