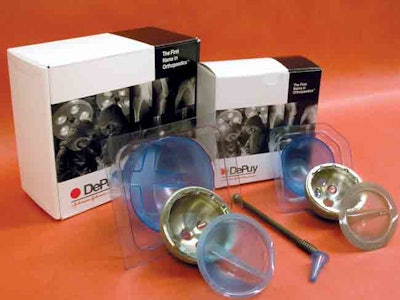
Warsaw, IN-based DePuy, a Johnson & Johnson Co., ships its hip and knee products in a conventional folding carton. Inside each carton, a sterilized product is hermetically sealed in a PETG thermoform with a polyolefin lidding material heat-sealed to its flanges.
The surfaces of the products themselves are given a relatively rough coating that is engineered to be a “fixation surface.” This surface facilitates the process by which the implant integrates itself with surrounding bone and tissue. But the roughness of the surface coating can abrade the PETG thermoform that holds the product, leading, at the very least, to marring of the package from an aesthetic standpoint. It might even damage the PETG material or the polyolefin lidstock to such an extent that sterility could be compromised.
To prevent this, DePuy had used die-cut pieces of PU that prevented abrasion of either the PETG package or its polyolefin lid. While the PU die-cuts performed satisfactorily enough, says Rod Patch, a manager in packaging development at DePuy, a recent switch to thermoformed PU from Barger Packaging has brought a marked improvement.