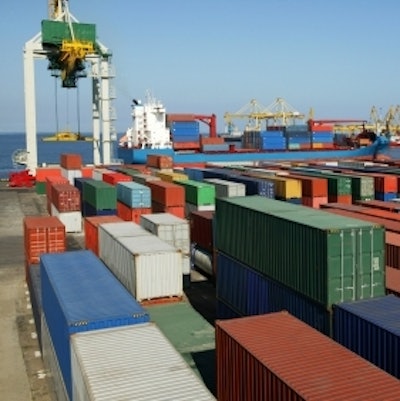
The twin trends of global markets and extended supply chains account
for the many container ships crisscrossing the oceans, each loaded with
thousands of containers and combined cargo worth hundreds of millions
of dollars. Consumer packaged goods (CPG) companies in the U.S. are
traveling both lanes of this transoceanic traffic, importing goods from
offshore manufacturers and exporting goods (especially to markets
wherein a devalued U.S. dollar makes their products more
price-competitive). As with all forms of transportation, proper
packaging for containerized ocean shipment is essential to cargo
arriving in acceptable condition; but lack of knowledge regarding what
constitutes proper packaging can result in unnecessarily high rates of
damaged cargo.
Unique Distribution Hazards. An ocean container is subject not only to
the hazards of surface transportation, but also to those unique to
water. An oceangoing container ship undergoes a variety of motions:
roll, pitch, yaw, heave, sway, and surge. We landlubbers need not be
versed in such seafaring terms, only appreciative that they describe
motions that are up and down, forward and back, side to side, rocking
and rolling---occurring in all possible combinations, depending on the
tides and weather.
In further illustration of the uniqueness of such hazards, it’s not
unusual for a container ship to roll 35° from vertical to one side,
return to vertical, then roll 35° to the other side, during which a
container stacked center-deck travels a sweep of more than 60 feet.
It’s not that the container slides along the deck; the travel is due to
the roll of the entire ship. By contrast, no truck or railcar undergoes
such pendulum swings, and couldn’t, without overturning.
Something else not done to trucks and railcars is the lifting and
stacking that’s done to containers to get them on and off the ships.
During the process, containers can undergo tilts and sudden
accelerations and decelerations, as they are raised and lowered.
Water is a hazard, often underestimated, because a container is thought
of as a secure enclosure that shields its cargo from the
elements - true, under perfect conditions. A container with the
slightest hole in its roof, sidewalls, or floor is not watertight, and
cargo can end up sitting in a puddle, particularly if the container
makes the journey stored on the deck of the ship. Even if stored below
deck, damaged containers can allow entry to high levels of condensation
and ship sweat. Incidentally, damage also can result from water
entering through faulty door gaskets, in an otherwise structurally
sound container.
Bad enough in their individual rights, physical and environmental
hazards can work in concert, such that cargo arrives at the destination
port a wet, crushed mess.
Protective Packaging. Distribution packaging (a.k.a. transit packaging)
is optimized when its protection capabilities are equal to the
anticipated hazards, because when less than, damage occurs, and when
greater than, added costs are incurred for overpackaging. For all its
theoretical simplicity, however, the equation poses practical
challenges, in that the more far-flung the logistics, the more
difficult it becomes to map hazards with precision, and the more
difficult it is to know from observations and measurements what to
anticipate, in what sequence, and to what degree. Adding to the
challenges is that damaged cargo from overseas can’t be replaced
rapidly, exposing a company to supply disruptions, lost sales, and poor
customer relations.
To err on the side of caution and accept the probable overpackaging
might seem a reasonable approach; however, sustainability has
introduced constraints. The clamor, especially farther down the
distribution channel, is for less packaging on all levels, not just the
primary packaging, but secondary, and tertiary (distribution
packaging)—corrugated boxes, film wrap, etc. Not that the levels are
independent from one another, far from it. Each should contribute to
overall protection and unit load integrity in a systems fashion.
Cubic Space Utilization. Whatever the design of the packaging and its
engineered capabilities, efficient use of the cubic space inside the
container is essential to protection. The cargo should be rendered as
immobile as possible. Ideally, unit-loads should be dimensioned for the
most snug fit. Realistically, however, those dimensions often are by
default, the product of factors more reflective of marketing concerns
than of transportation concerns: primary package and secondary package
designed for shelf-facing; case-pack quantity determined by tradition;
or unit load case count determined by order quantity.
Matters would be even less ideal, if not for the wide use of
standardized pallets that bear some relation to container width and
length. Another help is the availability of software that calculates
the most efficient pallet patterns, given the case dimensions.
Still, there will be voids within the container that have to be filled
with dunnage designed for that purpose. Also, it might be necessary to
use blocking and bracing to keep the cargo immobile. Dunnage, blocking,
and bracing consume space that might otherwise be occupied by cargo,
but, their use is justified by increased protection, as well as
increased safety because the container should not be so loaded that
cargo rests against the doors where it may fall out when the doors are
opened.
As long as the weight limitations of the container are not exceeded,
the objective is to fit as much cargo into the cubic space as is
feasible. For products so lightweight that weight limitations of the
container are not a factor, space utilization becomes even more
important. In response, some companies substitute slipsheets for
pallets, a common practice for truck trailers, but one that should be
adopted with caution for containers. The inches of clearance from the
floor provided by pallets can be cost-effective insurance against a wet
container bottom.
Strategic Opportunities for Package Engineering. A competitive
advantage accrues to companies with the most knowledge and control of
their containerized shipping. As earlier mentioned, geography makes
that difficult. It also provides opportunities for the package
engineering function - often regarded by senior management only in
tactical terms - to make strategic contributions.
Package engineering should step forward with protocols for the
evaluation of packaging and loading alternatives, not just for exports
but for imports. Another contribution would be standardized procedures
that assure that the weight of the cargo is balanced throughout the
container - what’s known as a planned stow.
It’s easier to standardize for frequently shipped homogeneous loads;
even so, heterogeneous, infrequent shipments lend themselves to some
standardization. One example is how cargo of varying sizes and weights
should be positioned and stacked so that the smaller and lighter items
are not damaged by the larger and heavier ones. Efficiencies can be
increased through computerized integration of the aforementioned with
shipping orders, whereby, for example, a load diagram is automatically
printed.
Another circumstance that can apply to homogeneous loads and
heterogeneous loads is different consignees, that is to say, the
container is unloaded over various stops. When the container is not
loaded first-in-last-out, costs and inefficiencies increase, and often
so does damage, when the remaining cargo is not properly secured. The
loading practice would seem common sense; nonetheless, it’s breached
time and again. It need never happen if every load is subject to the
proper document control.
Are all the foregoing standards, protocols, documents, etc., which in
no way constitute an exhaustive list, rightfully the responsibility of
the packaging function, or of some others within the
company - transportation, for example? A reasonable question, and one
best answered by keeping in mind that packaging is an interdisciplinary
function, and its place on the organizational chart varies widely among
companies. Packaging management should never shy from bringing forth
initiatives that impact its functionality, without concern over where
responsibility for execution is placed.
Federal inspection planning
Forward-thinking companies should be busy strategizing about federal
inspection of containers, a politically hot topic for years, that might
take form in the foreseeable future. How random it will be, how lengthy
a process, and whether it’ll be automated (i.e. scanners) or have a
manual component are key concerns. If manual, what’s the best way to
package and then load, brace, and block a container to accommodate that
type of inspection while insuring continued load integrity for the land
leg of the journey?
Containerized shipping will continue a steep growth curve,
particularly for routes between the U.S. and China, India, and Europe.
Container ships are being built bigger and bigger, the ultimate check
destined to be the navigational limitations of certain high-traffic
waterways, such as the Suez Canal. U.S. companies - big, medium, and
small - seeking their shares of world trade, would do well to
understand that at the heart of it all is the container, but it is
packaging that is the beat.
Before becoming a packaging consultant, Sterling Anthony worked for
Fortune 500 food, healthcare, and automotive companies, and has taught
packaging at the university level. He welcomes your comments by phone,
313/531-1875 or by e-mail, [email protected]. His Web site
is www.pkgconsultant.com.