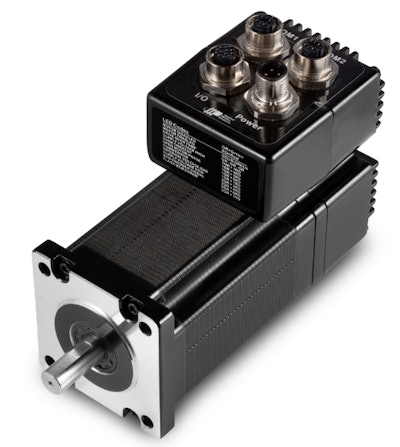
This content was written and submitted by the supplier. It has only been modified to comply with this publication’s space and style.
The encoders make use of a special energy harvesting technique to enable battery-less functionality. When power is removed from the motor and the shaft is free to turn, any movement of the motor shaft generates sufficient energy to power a dedicated electronic circuit that captures and retains the new encoder position. This can happen repeatedly and for any duration of time so that all changes in motor position are captured during power-off states.
The use of TruCount Encoders in motion control reduces downtime by shortening machine power up sequences and eliminates the need for homing runs after power cycles and emergency stops. With the ability to track more than 65,000 revolutions of the motor shaft, the integrated drive electronics track the absolute position of the motor shaft over a large working range. This reduces downtime and changeover time by eliminating time-consuming homing routines, which is advantageous in numerous applications including linear actuators with long strokes. There is no battery that can fail or that needs to be monitored and replaced over time.
Applied Motion Control's TruCount Encoders are available on select NEMA 23 and NEMA 24 frame StepSERVO Integrated Motors. StepSERVO Integrated Motors provide closed-loop servo control of high torque step motors, resulting in higher torque, greater acceleration, smoother motion, quieter operation, and better efficiency than conventional step motor systems. On-board, dual-port network connections for EtherNet/IP and Modbus protocols make these motors easy to install in new and existing applications in a variety of industries.