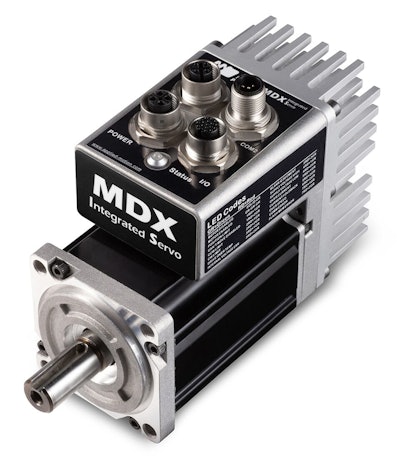
The MDX integrated servo motors provide greater design modularity and simplicity for a wide range of applications including automated guided vehicles and autonomous mobile robots in the accurate positioning of drive and lift axes.
MDX integrated servo motors house control electronics at the back, near the feedback device. No other external electronics package is required to drive or control the motor. The back of the motor also contains connectors for power, communications, and I/O. The MDX on-board controllers utilize the same command interfaces as external motor controllers including CANopen, RS-485, Modbus, and Ethernet connections as well as discrete I/O interfaces like pulse & direction. Command signals from a robot or machine’s central processing unit can be wired directly to the integrated servo motor.
Eliminating the need to connect motor power and feedback cables to an external motor controller, MDX integrated servo motors free space in a robot or machine to accommodate other critical components, such as material handling mechanisms, sensors, additional axes of motion, or operator-interface components. Robot designers can focus less on controller placement and wiring and more on non-motor system components for faster design iterations. MDX integrated servo motors benefit the robot designer in many areas by reducing the number of components in the system, eliminating cables or wire harnesses, freeing valuable space, simplifying the bill of materials, enabling faster design cycles, and saving money.
MDX integrated servo motors also provide a better solution to brushed DC and AC induction motors in serving as the main drive motors for forward/reverse motion and the material handling axes for accurate lifting, clamping, and engagement of the payload during transfer to different locations. In addition to providing more accurate speed and positioning than AC induction motors, MDX Integrated Servo Motors do not have motors brushes that wear out.
Every MDX integrated servo motors can run stored programs created with Q Programming that incorporates commands for various kinds of motion, I/O control, and machine sequencing, as well as math functions that enable users to create complex motion profiles and control algorithms. Two environmental ratings are available including IP65 and IP20. The most popular IP65 rated motor includes M12 connectors for all connection points. IP20 rated motors feature pluggable connectors that save cost in high volume, price-sensitive applications.