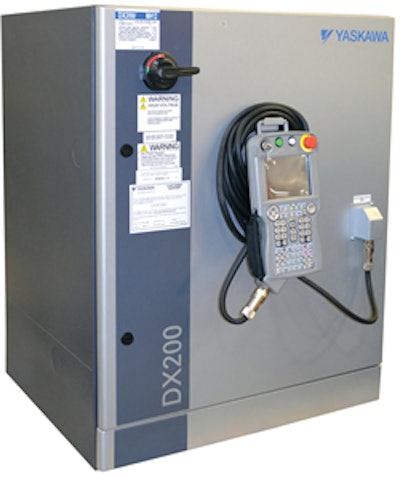
This content was written and submitted by the supplier. It has only been modified to comply with this publication’s space and style.
The EtherNet/IP safety interface can be used with or without Yaskawa Motoman’s Functional Safety Unit (FSU) capability, allowing a wide range of safety control options.
The EtherNet/IP safety software requires no additional hardware in the robot controller, and operates by allowing the exchange of safety input/output data between the DX200 robot controller and a safety PLC – typically a Rockwell Automation GuardLogix® PLC. When multiple robot controllers are managed by one master PLC, the GuardLogix PLC can manage the safety system (E-stops, safety gates, etc.). On multiple controller integrations, this replaces the unique dual channel wiring between the PLC and every controller, reducing redundant wiring and I/O modules, and allowing for easier troubleshooting.
“Reducing the wiring footprint and creating a safer work environment is just the start for the EtherNet/IP safety software option,” stated Dean Elkins, Senior General Sales Manager. “Real savings in integration time, troubleshooting time and lower engineering development hours are all very achievable benefits when adding an EtherNet/IP safety network.”
All machine safety signals, Functional Safety Unit (when included) signals and logic can be mapped to EtherNet/IP safety inputs and outputs. The safety communication interface is rated at Category 4 safety by TÜV Rheinland. It is also ODVA compliant. When EtherNet/IP safety is enabled, the standard (non-safe) EtherNet/IP communication interface is also provided with both scanner and adapter capabilities available for a non-safe EtherNet/IP network.