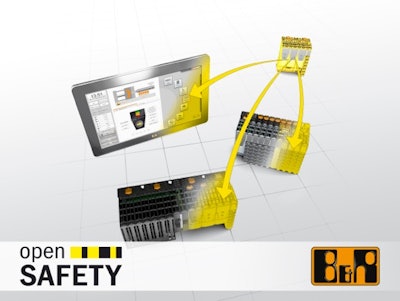
Programmed using the SafeDESIGNER editor in Automation Studio, the SafeLOGIC-X solution is just like the hardware-based SafeLOGIC solution. When a system outgrows its SafeLOGIC-X solution, it is easy to switch to a dedicated SafeLOGIC controller. The safety applications can be scaled and configured to meet the requirements of systems of any size. As safe input and output modules are added to a SafeLOGIC safety controller, existing programming code can simply be reused without having to make a single change. Switching over does not require recertification, another benefit that saves both time and money.
This type of unlimited scalability helps guarantee system continuity while also helping to ensure a uniform approach to engineering and diagnostics – two factors vital to increasing the availability of systems and machines.
SafeLOGIC-X is solely a software-based solution; extra safety controller hardware is not needed. Whereas safety functions are distributed across existing hardware components on the network, the safety application itself runs on a safe input module. All parameter and configuration management is handled on the standard controller. Safe user interface functionality is handled by the visualization device. The SafeLOGIC-X solution can be implemented on every single Automation PC, Panel PC, Power Panel, and modular control system from B&R.
The architecture used with SafeLOGIC-X is made possible by the openSAFETY standard. This safety protocol provides communication services that comply with SIL 3 requirements and helps ensure that parameters and configuration data are safely distributed and monitored over the entire network.