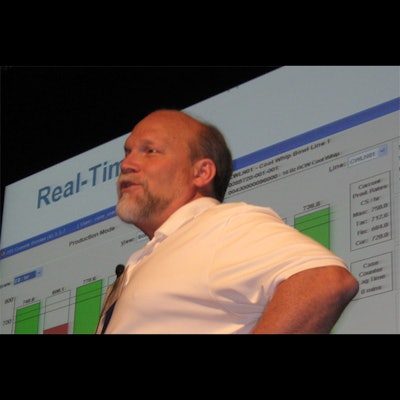
Your plant floor operators can and will make a difference in the efficiency of your packaging lines—if you give them the right information, the motivation, and the tools.
One case in point comes from Kraft Foods, the Northfield, IL-based food and beverage giant. “Real-time measures make it possible for the operators on the floor to affect OEE [overall equipment effectiveness] immediately. If they can see in front of them their [equipment] availability, performance, and quality—the three components of OEE—they can act immediately to make it better. That’s where it all begins,” declared Mark Hanley, Worldwide Reliability Lead at Kraft Foods Global (shown).
Indeed, according to Hanley, the savings attributable to a single OEE dashboard screen provided to Kraft packaging line operators has totaled $300 million to $400 million since the system was installed eight years ago. The screen, developed internally at Kraft, provides green, yellow, and red bars that show operators at a glance how they are doing on various real-time measures. “The plant floor people are competing between lines to see who can get the most green bars showing up on their screens,” Hanley observed. “And it’s really done a great job of increasing our productivity.”
Fourth annual PAF
Hanley made his remarks at the fourth annual Packaging Automation Forum sponsored by Packaging World and Automation World on March 31, in Rosemont, IL, near Chicago. Hanley’s presentation, titled “Real-Time Data Collection, OEE & Productivity,” was one of seven that covered a variety of packaging automation topics at the day-long event. The forum also included plenty of time for networking among the packaging end-users, original equipment manufacturers (OEMs), and vendors in attendance.
Forum attendees learned not only of the benefits to be gained from the use of advanced technology, but also about trials and tribulations along the way. Typical of that was a presentation by Allen D. Moore II, corporate electrical control manager at Lance Inc. (shown), the Charlotte, NC-based snack foods maker. Moore told the story of 12 years of continuous control evolution, in which the company went from two plants with legacy equipment and little plant-floor connectivity to a standards-based, networked automation architecture that provides shop-floor to top-floor connectivity in nine of the company’s 13 plants. “And we’re working on the others as we go, as quickly as we can,” he noted.
Lessons learned
But one pothole on that road to success involved the purchase of a large, OEM-developed OEE software package. “We thought we understood what was needed to implement this stuff, but we didn’t,” Moore said. “We spent a lot of money and a lot of time and got a real expensive software package that ended up on the shelf.” Among the lessons learned: “Big, fancy, and flashy isn’t always the best choice,” Moore told the audience, adding that starting simple and building up, working closely with OEM providers is a better course to follow.
Other topics covered at the forum included unit-level serialization in the pharmaceutical industry using radio-frequency identification (RFID); the use of wireless technology in packaging; and automation standardization in pharmaceuticals. In addition to Kraft Foods and Lance, other end-user presenters hailed from Nestle Purina, Niagara Bottling LLC, Pfizer Inc., and Purdue Pharma LP.