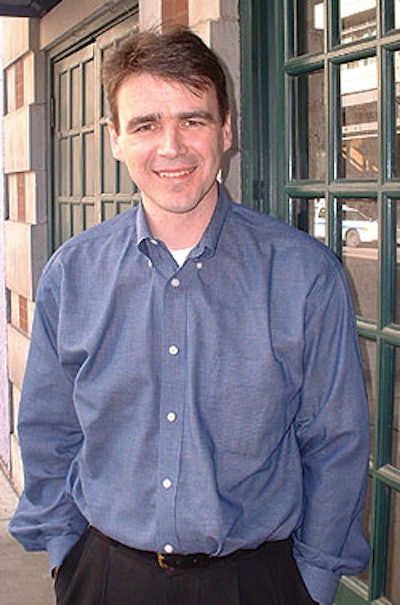
PW: What is one of your hot-button issues right now?
Atherton: Machine reliability. We have adopted Total Productive Manufacturing as our operational philosophy for our factories. It’s about eliminating the losses from the operation of your factory. There are 16 losses characterized by JIPM, the Japanese Institute of Plant Mainten-ance. Now we are systematically attacking and eliminating those losses through basic maintenance such as cleaning and lubrication, rather than investment in new assets. A very high percentage of failures are actually lubrication failures.
PW: That means it could have been predicted.
Atherton: Predicted and avoided. It’s about having the discipline and culture to care for your machines. The reliability that Southwest Airlines has, for example, is what we need. They aren’t doing it [attaining reliability] by massive investment programs and buying new airplanes every year. They’re doing it by systematic maintenance procedures every day—looking, touching, listening, smelling, and understanding what’s going on with their airplanes. If you can do it with an airplane, reliably putting liquid in a bottle should be achievable.
Some of the packing line operator interfaces have now got the maintenance routine built into the interface, saying before you start me up today, these are the things you’ve got to do. You’ve got to lubricate these fittings, and you’ve got to go inspect this belt, or whatever it might be.
I worked in Japan for two years before I came here. I worked in factories where the equipment was 30 years old. But it was spotless, and it ran like a Swiss watch, because it was carefully maintained.
PW: Once you achieve your reliability targets, what’s next?
Atherton: Improved factory floor information is going to become critical. And how we extract it out of our machinery is going to be key. We’ve got massive amounts of data and no information. And there’s nothing worse than having a $100ꯠ engineer trying to convert data into information. The technology exists that lets us present real information to people who can then use it to solve problems.
I believe a key element is to have a standardized language for data extraction and information management built into the controller of each machine [like PackML, which Unilever is helping to develop]. But to really exploit it, every machine on the line needs to really be talking the same language.
PW: What about machine flexibility?
Atherton: We serve essentially five classes of customers: mass merchandisers, club stores, food retailers, drugstores, and dollar stores. But what’s good for Wal-Mart, a mass merchandiser, is not necessarily what’s good for Walgreen’s, a drug outlet. We have the capability to put bottles in a case, but it is becoming more important that we are offering more customized solutions for our customers and ultimately our consumers. How do we get that sort of flexibility in our packaging assets to present our products to customers is something we need to improve. We just tend to go for “Well, this is what Wal-Mart wants, so this is what everybody else is going to get.”
PW: Are you willing to pay more for a flexible machine?
Atherton: If it enables us to grow our business by better servicing our customers and meeting the needs of our consumers, then absolutely.
PW: Is there any metric you have that can illustrate a trend toward increased number of changeovers in your factories?
Atherton: We’re trying to simplify our business by reducing the number of SKUs [stock-keeping units] we produce. It’s the old 80/20 rule...80% of our revenues come off of 20% of our SKUs. So we’re trying to cut that tail out. But the real pressing issue is, you can’t make this product on this line for 6 months and store all that inventory and sell it over the remaining six months of the year. Our goal is to make every SKU in our portfolio every week. That way we can minimize demand forecast error in the supply chain. And the nearer we can get to make-to-order instead of make-to-forecast, the more working capital we pull out of the supply chain and the more responsive we become to our customers’ needs. That requires a level of packing line flexibility that we do not really have today.
Right now we probably cycle through our portfolio on a monthly cycle. So we’re probably carrying a month’s worth of inventory, as a rule of thumb. A month’s worth of finished goods inventory has a considerable value. If we could cycle on a 2-week frequency, we can theoretically release a large amount of working capital to reinvest in our business innovation activities and growth agenda.
PW: What’s your view on third-generation servo-driven packaging equipment? Can it help your requirements for flexible packaging machinery?
Atherton: I have no doubt that flexibility and speed-to-market demands are forcing us down the path of servo technology. For instance, we have recently lost some production time after having to rework a mechanical cam for a pump placer to handle a new shampoo pump. The pressing business need to deliver the new package faster than we have in the past was hindered by the adjustment time. Obviously, a servo-driven pump placer would enable a faster response and enable multiple pump types to be handled with minimal changeover time versus the time-consuming cam-change.
PW: What about training? Can people in your plants support servo-driven equipment?
Atherton: There’s no doubt it’s a challenge to keep the skill base of our technicians and engineers up to date. The technology’s moving faster than we can train people, to be honest. But I don’t think we can afford to say “because we can’t train our people, put a cam on it.” The increasing marketplace demands to deliver variety and change to our customers and consumers on an ever-reducing cycle make this an imperative in my mind.
My profile for a packaging equipment engineer in our factories is rapidly becoming an electro-mechanical skill set. It can’t be a mechanical skill set, and it can’t be electrical only. It has to be an electro-mechanical [mechatronic] skill set.
PW: Are you looking into reducing the number of your key packaging machine vendors?
Atherton: Yes. If we can gang together our purchases and focus on key suppliers, the incremental cost [of flexible packaging equipment] is recovered through the scale benefit. Historically, Unilever has given a lot of local factory autonomy for machine purchases, but this is starting to change as we look to leverage our size. A standardized asset base also offers the supply chain sourcing flexibility, training benefits across factories and technologies, reduced spare parts carrying costs, and the opportunity to share best practices more effectively. —DN
For more, visit JIPM's Web site at: www.jipm.or.jp/en/home