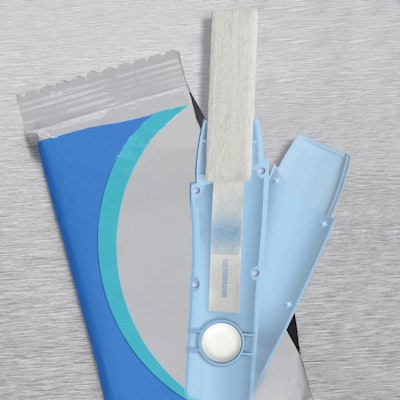
Today’s diagnostic tests, especially molecular diagnostics, are based on complex, innovative sample-to-solution technologies. Packaging the final device for optimal performance, stability and shelf life is every bit as important as the chemistry that drives the test. Leveraging sorbent technology can help you meet these objectives.
1. Identify moisture vulnerability and the optimal sorbent
Moisture is a primary pathway for product degradation. Hydrolysis accounts for the majority of reactions leading to degradation with chemical and environmental factors contributing significantly.
For example, the extreme heat and high humidity locations in which infectious disease diagnostic devices must perform can create stability and quality concerns. Additionally, the lyophilized formats of chemicals used in cartridges for PCR-based (polymerase chain reaction) technologies are extremely vulnerable to moisture issues.
In such instances, packaging devices with desiccants to control moisture is critical to assure test integrity. Quality by Design (QbD)-based pseudo-empirical modeling offers a quick way to assess moisture vulnerability and identify the optimal sorbent solution.
Pseudo-empirical modeling is based on parameters specific to your product including: degradation profile, packaging materials, sorbent type, and required shelf life. The accuracy and speed of these simulations can eliminate the need for lengthy sorbent ranging studies, helping you to reduce development time by six to 12 months.
2. Select the right format
Desiccants today are available in a wide range of formats, from those that you drop loosely into the package to ones that are built into the device itself. Selecting the one most suited for your application can offer unique benefits to your device.
Desiccant packets that are loosely dropped in can sometimes interfere with the opening of a foil package or become lodged in the test cartridge. A desiccant in the form of a compressed solid form can be snap-fit into the device itself, eliminating these issues. Compressed solid form desiccants can be tailored to meet many different sizes and shapes to address the unique stability requirements of your device.
Newer desiccant formats can be built into your device by replacing structural or functional parts. Extrusion- or injection-molded polymer components, loaded with desiccant, become part of the device themselves and provide a reduction in total components. These polymer-based desiccants also allow for increased handling time during packaging vs drop-in packets or loose desiccant beads.
3. Assess regulatory requirements
Make regulatory compliance easier by addressing these key questions with your vendors:
• Are all materials in contact with the device FDA-compliant?
• Do your sorbent products have a Type III Drug Master File?
• Are all quality requirements for 510(k) or PMA submissions being met?
• Is your sorbent manufactured in an ISO 9001-compliant facility?
For drop-in sorbents, the optimal sorbent dispenser can further support your regulatory compliance and quality initiatives by providing product traceability and integrating key manufacturing information into your SCADA system.
4. Build long-term partnerships with vendors
Vendors who are committed partners will work with you to overcome complex challenges and achieve success. Ask potential partners about their:
—Experience and reputation in the industry
—Specific capabilities to support diagnostic devices
—Ability to customize products to overcome complex challenges
—Commitment to innovation and ability to support new products
—Business continuity plans to minimize product disruptions
—Processes to effectively address and resolve quality events
5. Focus on quality and total cost
Today’s diagnostic device platforms require the highest innovation, and quality standards must be met. Focusing only on price-per-piece for sorbents can result in lower quality products and higher costs. Evaluating the correlation between efficiency, reliability and cost is a critical step in assuring quality.
Underperforming equipment or poorly performing sorbents can drive up hidden costs through increased downtimes, customer returns and management time required to resolve such issues. Uncovering these hidden expenses and factoring them into the total cost of operations will better allow you to improve quality and manage costs.
Quality and price are not mutually exclusive when total cost is considered. A committed, long-term partner can help you evaluate options.
In the end, a correct diagnosis depends on the test performing accurately. By leveraging the optimal sorbent for your packaging, you are taking the crucial steps in assuring test integrity.
Authors: Multisorb Technologies’ Chris Gilmor, Commercial Director, Healthcare Packaging – Americas, and Paige Weis, Business Development Leader, Healthcare Packaging.