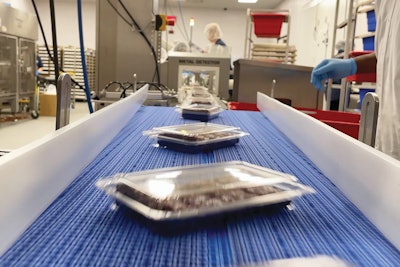
This content was written and submitted by the supplier. It has only been modified to comply with this publication’s space and style.
Multi-Conveyor recently caught up with Yates, along with Matt Tye, The Killer Brownie Company Packaging Operations Manager, at the recent PACK EXPO East trade show. Watch the video as Yates and Tye discuss the benefits of their new sanitary constructed, single tray dual lane product turning conveyor required to rotate single lane brownie containers 90°.
“We got the Multi-Conveyor about two weeks ago. So, last Tuesday we had a big run on product in this type of container (he holds up a plastic tray). Before, 80 to 90 packs a minute is about where we could go before our (t-arm) turner would fail and jam up. With the Multi-Conveyor, now we’re pushing between 100 to 110 packs per minute with no issues at all. And, actually, we had to upgrade other parts of the line to keep up with the Multi-Conveyor. Really, really happy with it so far", explains Tye.
To improve consistency, packaging speeds and boost capacity, Multi-Conveyor provided the 60 in. long dual strand system, sized to The Killer Brownie Company overall footprint specifications, designed to meet or exceed a requested 120 trays/min. Dual lane product turning conveyors are simultaneously straight running, moving at varying speeds that cause the required tray rotation needed for the labeling process downstream. Precise adjustments are calculated to ensure proper gap between the trays without collision.
A low profile infeed accommodated the existing wall opening. The stainless steel, hygienic wash down constructed conveyor included bolted stand-offs for guide rail brackets, flange bearings and floor supports.
All welds are continuous, cleaned, and passivated for sanitation. Pre-wired VFD’s and E-stops were also included for ease of operation. All equipment is fully assembled and tested prior to shipment at Multi-Conveyors facility.
Yates continues, “The customer service, working with Tom and your team at Multi-Conveyor, has been absolutely amazing. We appreciate the partnership.” “Wonderful, absolutely,” adds Tye.