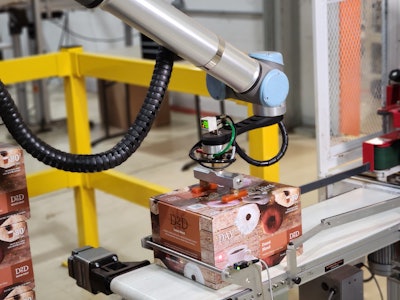
In 1897, Steve Papanicholas immigrated from Greece to Chicago, where he founded Overland Coffee Co., now Napco Brands, a family-owned coffee company that uses the same robust sourcing, roasting, and blending practices developed by Papanicholas at the turn of the century. Since its founding, the company has expanded from roasting and packaging a single in-house brand to producing four distinct coffee brands: Papanicholas, Day to Day, Versanto, and Basic Joe. It also offers a growing line of private-label coffees.
“At Napco, we have a lot of capability to pack for private label,” explains Eric Latsch, vice president of operations for Napco and Papanicholas’ great-grandson. “We have a lot of factory services we can offer, anywhere from roasting [the coffee] to packing it into a sealed container for retail sale or for restaurant or foodservice businesses.”
Eric Latsch, great-grandson of company founder Steve Papanicholas, is vice president of operations for Napco, which produces a range of its own coffee brands as well as private-label options.
Cobots prove cost effective, reliable
At its facility in Naperville, Ill., a suburb of Chicago, Napco has two production lines manufacturing single-serve coffee capsules. Before installing the robotic palletizers, all of the company’s operations were manual: An operator placed capsules into cartons and brought the cartons to another operator, who taped and palletized them.
To find areas where the process could be optimized, Latsch worked with Brian Einzig, sales engineer at FPE Automation, who evaluated the line to pinpoint areas of opportunity for automation. For the end-of-line palletizing task, Einzig recommended the AX10 Robotiq Palletizing Solution with a UR10e cobot due to the system’s ease of deployment and its ability to handle a wide variety of pallet heights. Einzig then enlisted Jeff Benning, chief executive officer of DesignHawk Innovations, to integrate the two new palletizers into the existing line.
Before he selected the Robotiq system, Latsch shares that he had considered many different types of packaging equipment to improve production, but he found the costs prohibitive. “There’s a large barrier to entry when you’re talking millions of dollars in a single packaging line that may or may not help you,” he says.
Collaborative robots were a much easier and more cost-effective option, he notes. In fact, the Robotiq Palletizing Solution paid for itself in less than a year, while other parts of the project returned their investment in about two years. The cobot palletizers run two shifts, operating 18 to 20 hours per day. Each day, each palletizing cell fills 1,500 cartons, totaling 180,000 single-serve coffee capsules packed daily between the two cells. The robots have helped increase productivity at Napco by about 15%.
According to Latsch, because costs are now fixed rather than variable and since the system has significantly reduced overtime, the company has been able to be more aggressive on bidding new business. “Having this automation with a higher efficiency has made it possible for us to acquire new customers,” he says. “We have several new private-label customers we couldn’t have dreamed of two years ago.”
He adds that the robots also provide the reliability that is so critical to Napco’s private-label business. “With our own brands, if you don’t get something out as soon as you can, you only have to answer to yourself. If we’re making a product for another customer, we have to make sure it’s done on time, and to get it done on time, we have to have something like a robot that’s going to show up and perform,” he says.
Eight operators freed up from palletizing
Napco has never had an employee layoff, and automation hasn’t changed that approach. Instead, in today’s tight labor market, the two robotic palletizers have allowed the company to redeploy eight valued workers per day. Rather than performing the manual task of palletizing, the employees have been reassigned to operate larger equipment at higher pay in specialized tasks that require human capabilities.
In addition, the robotic palletizers have eliminated employee injuries resulting from lifting and bending to palletize cartons, along with the high employee turnover associated with repetitive jobs. The cobots’ built-in safety features also provide employees with additional protection against injury. The UR10e features force-sensing technology and collision detection that allow the cobots to work alongside operators without the need for safety barriers or cages, promoting a safe working environment.
Up and running in a day
As Benning of DesignHawk explains, while Napco’s packaging line uses a PLC to communicate, the cobot palletizers use a built-in controller from UR, with no additional PLC required. “Each robot knows the other exists, so if there’s an issue with one, it’s transmitted to the other,” he says.
The built-in controller also eliminates the need for additional hardware. “It’s all right there,” Benning says. “There’s less to diagnose, there’s less to program, there’s less we have to teach Napco to maintain, and then ultimately, there’s just less that can go wrong.”
The palletizing system features an intuitive online configurator, which enabled Benning to quickly map out the application during setup. Once carton sizes, pallet dimensions, and format are entered, the simulation provides an accurate cycle time for the process. “That’s always one of the difficult parts of our job, determining exactly how the final system will run,” says Benning. “It was a huge benefit knowing that we’re going to meet the cycle time we need; we’re going to put enough material in boxes at the right rate for Napco. After seeing the simulation software and realizing that Robotiq had the whole palletizing package, it was a really obvious choice.”
When the palletizers were installed, Latsch was surprised by their small footprint and how fast they were to set up. “Installing the Robotiq Palletizing Solution with UR cobots was definitely the easiest thing we’ve ever done,” says Latsch. “I don’t even know if it was more than a shift to get it up and running from when they delivered it. I couldn’t imagine it going any better.”
Easy programming and minimal training
According to DesignHawk’s Benning, one advantage of the Robotiq palletizing system is the ease of programming and ongoing use. He adds that after deploying a new system at a customer’s site, his focus is on working with them to make sure they feel confident in maintaining the system and taking ownership of it over its lifetime. He says that UR’s intuitive cobots and Robotiq’s palletizing software have make his job simpler. “Once the system is set up, it’s very easy for Napco to add new boxes or different size pallets,” he explains.
Notes Robotiq, the palletizing software makes changeovers quick and easy. It takes less than a minute on the cobot’s touchscreen to change the size of a box, the number of boxes that go on a pallet, and the direction of the boxes. When a new product comes in, an operator is able to take an existing installed program and modify it for new requirements. “It’s a very simple process,” confirms Napco Brands Production Floor Manager Eric Matthews, who had no previous experience with robots before the new system was installed. “DesignHawk walked me through it—no more than five to 10 minutes of training—and I can take any size box, with any parameters, and program the system myself.”
One of Napco’s two Robotiq cobot palletizers picks a sealed carton of coffee capsules from a conveyor for placement on a pallet.
As Latsch looks across his business and the manual packaging processes still required for different coffee products, he sees many other opportunities for collaborative robots. “I think cobots would be helpful in almost any factory setting,” he says. “It depends on the task, of course, but I could find a use for them anywhere.” He also recognizes the importance of the right integrator and distributor, saying, “DesignHawk and FPE Automation made the process as easy as it could be.” PW
![]() | In the market for a palletizer? Click on this link to see a curated collection of palletizing case studies. |