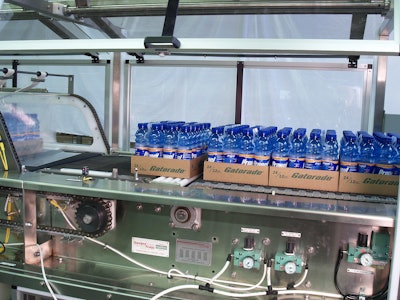
The 296TS uses an intuitive graphic operator interface. The system’s advanced diagnostic program automatically directs the operator to a fault screen in the event of a problem and also provides automatic scheduled maintenance alerts. The heavy-duty stainless steel-framed system also features easy “walk-by” maintenance, made possible by transparent guarding that allows the system’s parts to remain clearly visible.
The shrink-wrapping section of the 296TS features an on-demand film wrapping wand, a smart innovation controlled by a servo motor and sensor. Eliminating the continuous cycle operation of previous wands, the on-demand wand runs only when needed, eliminating wear and tear.
Addressing the challenge of time-consuming film rethreads, the system’s film feed redesign includes a simple, single-pass, error-free film thread system. The film bed has also been outfitted with an easy-access clamshell design that can easily be opened and removed for periodic maintenance.
Operating at speeds up to 80 trays/min., the 296TS provides a smooth transition during the product/tray merge. The system offers servo-driven Zero-Gap infeed technology that incorporates precise geometry and sensors to ensure a continuous container supply to the downstream lanes and grouping section, for balanced, jam-resistant packing lanes. Customers can choose between a free-standing or complete tray/shrink system, as well as an integrated tray stacker option.
Siad to handle the largest diameter range in the industry, the robust 296TS Continuum Tray/Shrink System is suitable for both loose containers and multipacks in a variety of materials, including glass, PET, HDPE, metal and fiber cans, HiCone, shrink bundles, and paperboard overwrap. These products can be packed into both corrugated and chipboard trays for added flexibility.