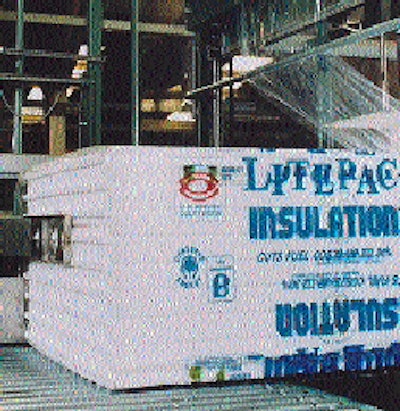
The system creates fully protected loads by tightly stretching bands of low density polyethylene around stacks of insulation board. The bands are stretched both vertically and horizontally, thus producing a fully enclosed and tightly wrapped bundle. Litepac uses a light-gauge, 50-micron LDPE, preprinted with the Litepac name. Seal jaws ensure full enclosure, while an adjustable stretch tension feature protects the boards from warping. This "stretch technology," as EDL refers to it, eliminates the need for a shrink tunnel, while reducing the amount of film used, thereby reducing costs.